According to different working environments, the furnace wall can be divided into ordinary furnace wall area, slag line area and hot spot area. Furnace wall is often subjected to high temperature effect and the impact of rapid temperature changes, but also by the direct scouring of liquid steel, slag chemical erosion, as well as mechanical collision of the charge and other thermal shock. So to improve the service life of the furnace wall and those technical means?
Further improving the quality of refractory linings
1. The use of large crystalline magnesium sand
The erosion of slag on refractory materials and MgO-C redox reaction starts from the grain boundary and the foreign material located at the grain boundary. The use of high purity, large crystallization magnesium sand helps to improve the erosion resistance and oxidation resistance of magnesium carbon bricks.
At high temperatures, the MgO+C→Mg+CO reaction increases the porosity of the bricks decreasing the strength and service life.In the migration of M(g) to the surface, a dense layer of Mg0 is formed near the refractory-slag interface. The dense layer is favorable for improving slag resistance and oxidation resistance. In addition to temperature, it is mainly affected by the purity and grain size of magnesium sand. Impurities such as SiO₂, B₂O₃, and Fe₂O₃ in magnesium sand increase the MgO-C reaction rate and increase the distance between the dense zone and the hot surface. This is because SiO₂ is more likely to react with C and volatilize or form a melt in which MgO is also more volatile, and magnesia with a high CaO/SiO₂ ratio is less volatile. So the raw material chemical composition of magnesium sand tends to choose high purity, low SiO₂, B₂O₃ and high CaO/SiO₂ ratio. In the composition of similar, large grain, high-density electrofused magnesium sand is better than sintered magnesium sand. Therefore, the production of large grain sintered magnesium sand with an average grain size greater than 150 um has also been initiated.
An Austrian company were used grain size 160pm large crystalline sintered magnesium sand and the average grain size of 80μm of ordinary dead burned magnesium sand made of magnesium-carbon bricks containing C10% with a resin bond to do anti-erosion comparison test, the result is that the large crystalline magnesium-carbon bricks erosion index than the latter 23% lower.
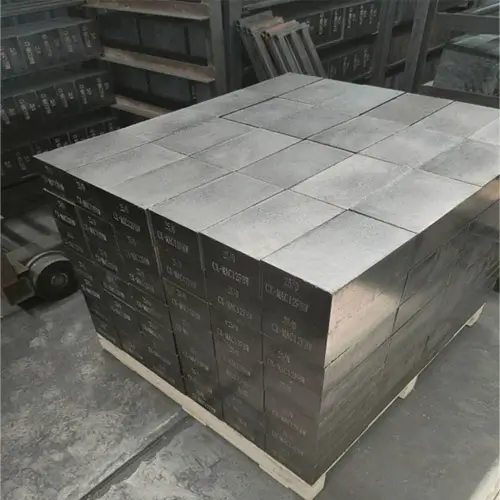
2.The role of high purity graphite
The use of high-purity graphite to make bricks has also been emphasized, the type of graphite, particle size distribution on the brick carbonization porosity in the oxidizing and reducing atmosphere of the high temperature strength and MgO-C reaction have an effect.
About 95% of the ash in flake graphite is composed of oxides such as SiO2, Al2O3, Fe2O3, K₂0, N2O, etc., of which SiO₂, again, accounts for a high proportion.SiO₂ reacts with C at high temperatures as follows.
SiO₂+C→SiO(g)+CO(g)
The reaction starts at 1160°C. Other ash compositions such as Fe2O₃; etc. also undergo a reduction reaction, resulting in a loose brick structure. And these impurity oxides react with magnesium sand at high temperatures to form low-melting materials, which will definitely affect the high-temperature strength of the bricks.
3.Behavior of additives
Metal additives such as Al, Si, Mg or their mixtures and alloys play a role in preventing the oxidation of graphite by reacting with oxygen more readily than graphite, and the carbide formed improves the mechanical properties of the brick. For the addition of two kinds of metal powder such as Al-Si, Mg-Al favorable dry to broaden the temperature range of anti-oxidation. Reduce the particle size of the metal powder can make the structure dense, less oxidation, high strength, and promote graphite development. The addition of >3% has a significant effect, which is a powerful measure to improve the antioxidant property of MgO-C bricks. However, it has been shown through in-depth research that the additions also have side effects. For example, the final product of Al powder, Al₂O₃, and silicate impurities in magnesium sand start to form a melt at 1400°C. If the SiOz content of 2%, so that 1540 ℃ high-temperature strength reduced by 50%, will have a negative impact on the service life. Al4C3 at low temperatures are easy to hydrate, in the stopping of the furnace leads to crack formation. The additives increase the coefficient of linear expansion of the brick, potentially creating excessive stress in the masonry within the brick.
The increased research on non-oxide additives is mainly due to the fact that borides, carbides, and nitrides have a high degree of oxygenophilicity, while their oxides can form a liquid-phase protective layer on the surface of the brick.
Various additives are used and CO (g) reaction caused by C condensation and the volume expansion of the accompanying oxide generation and the final formation of the surface oxide protective layer or the formation of low co-melts play a role in preventing or delaying further oxidation. The reactions of the additives are as follows.
(1) Borides (ZrB₂, CaB6, Mg2B₃).
ZrB2(s)+5CO(g)=ZrO2(s)+B2O3(g)+5C(s)
Mg2B3(s)+13/2CO(g)=2MgO(s)+3/2B2O3(s)+13/2C(s)
CaB6(s)+6CO(g)=CaB₂C2(s)+2B₂O3(g)+4C(s)
(2) Carbide (B4C):
B4C(s)+6CO(g)=2B2O3(s)+7C(s)
The appearance of B2O3 liquid phase (melting point 557°C) can play a role in filling the air holes. B2O3 at high temperatures, evaporates at 1200-1300°C, but the evaporation of gaseous B2O3 has an effect on oxidation resistance. Carbide or boride is also effective when used alone, and metal additives and often appear to multiply the effect.
However, magnesium-carbon bricks can be used without metal additives in parts that are not dominated by oxidative damage.
4.Vacuum oil immersion
At high temperatures, CO escapes from within the magnesium-carbon bricks leading to carbon depletion. The increase of apparent porosity after carbonization will affect its service life. Oil immersion treatment of the brick can close the pores, reduce the porosity after carbonization, and improve erosion resistance is also a way to improve the quality of magnesium-carbon bricks.
Magnesium-carbon bricks after vacuum oil immersion, used in the high temperature area of the electric furnace wall, slag line, hot spot parts, it not only improves the performance of the brick. And avoid the use of metal additives brought about by the potential hazards.
5.Binding agent
Phenolic resin bonding agent, has been pursued after pyrolysis with high residual carbon, the higher residual carbon amount of 50%-60%, not many up to 70%. After hardening, the high polymerization resin has good uniformity, fewer defects in reticular structure, high strength and less environmental pollution.
Asphalt binding agent can be better graphitization and has high antioxidant stability. However, it is easy to produce cracks inside the bonded carbon, and the strength of the products is reduced. Europe generally use additives to improve the carbonized structure, improve the asphalt residual carbon.
Asphalt – resin composite application to form a fine mosaic structure, enhanced carbon binding fracture toughness, strengthen the carbon binding to improve the antioxidant, the practical application of good results.
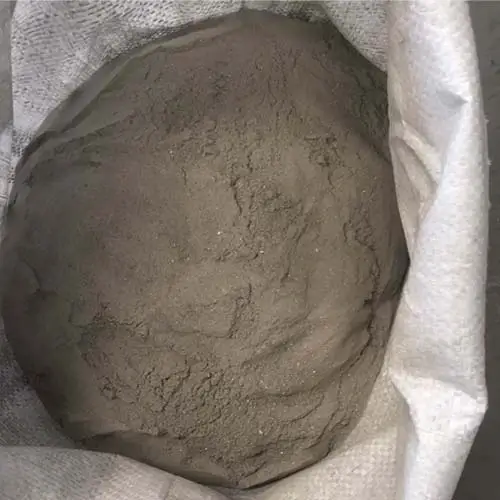
Enhanced Furnace Wall Spray Patching Technology
“Spraying” is one of the effective measures to protect the furnace. The use of phosphate binding agent, and add an appropriate amount of hardener and plasticizer to improve the workability of magnesium spray patching material for the wall of the furnace has a high adhesion rate and better spray patching effect.
Magnesium spray patching material for seamless 150tUHP electric furnace, the use of imported centrifuge spray patching, each spray patching amount of about 1-1.4t, spray patching time an average of 12-17min. spray patching adhesion rate in the No. 1, No. 2 hot spot 80%, No. 3 hot spot of 70%-75% each spray patching can be smelted after 1-3 furnaces, the effect is good.
Spray patching material with the bonding agent is the key to the effectiveness of spray patching, according to the bonding method of chemical bonding and ceramic bonding. According to the bonding temperature, there are low temperature and high temperature bonding. Commonly used binding agent for the silicate, phosphate, chromate, sulfate and various magnesium salts. In the steel does not increase carbon under the premise of phosphate bonding spray patch material adhesion strength, life than the silicate bonding material high. A steel 50tUHP electric furnace with silicate bonded spray patch life only once. The use of composite salts as a binding agent life of 3-4 times.
Strict control of smelting process
1.Make good foam slag
The shielding effect of the foam slag not only improves the thermal efficiency of the electric furnace, but also effectively protects the furnace wall from the role of high temperature arc radiation, thus significantly reducing consumption. A steel 50tUHP electric furnace, power consumption reduction of 10-30kW-h/t saving refractory materials about 50%, saving electrode about 20%, to extend the life of the furnace wall plays a very good role.
2.Preferred slagging agent
Hamburg, Germany 110tUHP electric furnace, in the case of no intermediate repair and do not carry out any spray patching, the life of the furnace up to 1000 furnace. Furnace long life of the key measures, in addition to the lining structure is reasonable selection of refractory materials properly, effectively create a good foam slag and hot spots with dolomite material spray patching, slagging agent is also very important to optimize the selection.
Slagging agent selection of lime: CaO94%, MgO0.5%, granular material 20-40mm, fine powder 0-0.1mm; high purity dolomite: Mg030%-40%, CaO56%-59%, particle size of 2-5mm or 2-7mm; lime and dolomite used in conjunction with the slagging system in accordance with strict operation.
In addition, in the operation of UHP furnaces, the use of laser thickness gauges to monitor the degree of damage in order to correctly determine the remaining thickness of the bricks in service is a necessary means of ensuring safety and improving longevity.
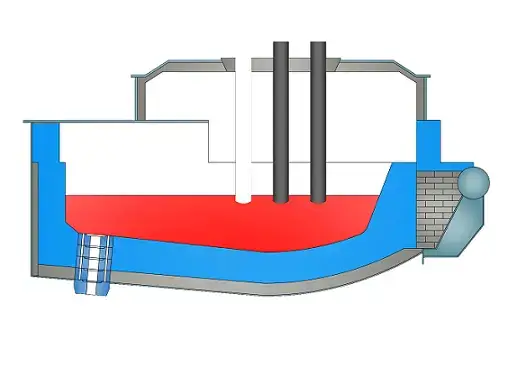
EAF Furnace