Converter is an important equipment for steel making, it is a kind of steel making furnace which does not need external heat source and mainly takes hot pig iron, scrap steel and iron alloy as raw material. According to the nature of the lining refractory material is divided into acid converter and alkaline converter, according to the part of the gas blowing into the furnace is divided into bottom blowing converter, top blowing converter, side blowing converter and top and bottom composite blowing converter.
Converter steelmaking method has a long history, as early as 1856 British Bessemer (Bessemer) invented the bottom-blowing acid converter, for the beginning of modern steelmaking method. 1879 and Thomas alkaline converter, which can deal with high-phosphorus pig iron. 1864 Frenchman Martin used the principle of heat storage to create a flat furnace steelmaking method, which once became the world’s main steelmaking equipment, in the 1950s, about 85% of crude steel smelting by the flat furnace world. In 1952, Austria appeared pure oxygen top-blowing converter, solved the problem of the content of nitrogen and other harmful impurities in the steel, and at the same time reduce the loss of heat with the exhaust gas, can be blown with a lower temperature of pig iron, saving the consumption of blast furnace coke, and can use more scrap steel, steelmaking speed is particularly fast (a furnace of steel in about 10 min, while the flat furnace to 7 h), 1968 and the emergence of oxygen bottom-blowing converter. Oxygen bottom blowing converter appeared in 1968, in 1970 and invented the bottom blowing method with hydrocarbon protection of the double casing bottom blowing oxygen gun, various types of bottom blowing method (such as OBM, Q-BOP, LSW, etc.) in the actual production of many advantages over the top blowing place. Austrians in 1973 to study the top and bottom blowing steelmaking process, the early 1980s into production, which is superior to the top and bottom blowing, some countries have basically eliminated the simple top blowing converter.
In our country, in 1951 Tangshan steel plant air side-blowing converter steelmaking method test success, put into production in 1952, 1954 small oxygen top-blowing converter test success, 1962 Shougang air side-blowing converter into 3 t oxygen top-blowing converter, put into production in 1964, two 30 t top-blowing oxygen converter, with the Tangshan, Shanghai, Hangzhou and other places in the iron and steel mills have converted the 3.5-5 t top-blowing oxygen converter, followed by some large-scale steel enterprises, such as Anshan Steel, Wisco, etc. will be flat furnace to 250-300 t oxygen top-blowing converter, put into production in 1985, with advanced technology, Baosteel is also using 300 t large-scale top-blowing oxygen Converter, followed by some large iron and steel enterprises, such as Anshan Iron and Steel, Wuhan Iron and Steel and other flat furnaces into 250-300 t oxygen top-blowing converter, put into operation in 1985, with advanced technology, Baosteel is also using 300 t of large oxygen top-blowing converter for steelmaking, since then, China basically eliminated the flat furnaces for steelmaking. In recent years, the emergence of top and bottom blowing composite blowing converter, sliding plate slag technology, so that the smelting time is shortened, the steel composition and temperature is more uniform, to reduce inclusions in the steel, improve the cleanliness of the steel, etc., some of China’s steel mills are also commonly used top and bottom composite blowing technology. According to statistics, converter steel accounts for more than 70% of the world’s total crude steel production, and China accounts for 90%.
Basically, the converter is built by refractory materials, and the cost of refractory materials for steelmaking accounts for about 9% to 13% of the cost of steelmaking process. Due to the different composition of the iron and refractory raw material resources in different countries, the choice of refractory materials for the furnace lining also has its own focus, Europe and the United States, Russia and other industrially developed countries have developed from the dolomite, magnesium products to the current magnesium carbon bricks, Japan was the first to use magnesium carbon bricks of the country. China’s converter lining through the tar dolomite, tar magnesium, magnesium dolomite, magnesium dolomite carbon bricks to the current widespread use of magnesium carbon bricks. Due to the magnesium carbon brick erosion resistance, thermal shock resistance, wear resistance, good thermal conductivity, anti-flaking, stable performance at high temperature, converter lining commonly used in various countries. The performance and quality of refractory materials, directly affecting the converter steelmaking method and service life, to improve product quality and economic efficiency has a very important significance, refractory materials for converter problem has attracted people’s attention, emergence of a number of refractory materials, such as spraying technology, spattering slag to protect the furnace technology, sliding slag slag sliding water mouth blocking technology, and so on.
1. Structure of the converter lining and refractory damage mechanisms
Furnace lining structure can be divided into furnace bottom, melting pool, furnace wall, furnace cap, slag line, trunnion, furnace mouth, steel outlet, bottom blowing gas supply brick and other parts. Converter lining consists of adiabatic layer, permanent layer and working layer. Insulation layer is generally used asbestos board or polycrystalline refractory fiber masonry, and now some of the magnesium sand filling layer instead of the cap insulation layer made of resin magnesium sand; permanent layer of the parts are not the same, more low-grade magnesium-carbon bricks, or tar dolomite bricks or sintered magnesium bricks masonry; working layer of magnesium-carbon bricks all masonry. There are three grades of magnesium carbon bricks in China. Converter different parts of the use of magnesium carbon brick has different performance requirements, Japan Shinagawa refractory company developed to meet the requirements of different parts of the series of magnesium carbon brick products, see table 1. in the converter production process, due to the working layer is directly affected by the addition of the mechanical impact of scrap steel and abrasion, and high temperature slag direct contact with the hot steel slag, by the high temperature slag and the infiltration of the hot water and erosion of the molten steel, as well as by the molten steel, slag and the furnace gas scouring, etc., the working conditions are very harsh, the working conditions are very harsh, the working conditions are very harsh, the working conditions are very harsh. Role, the working conditions are very poor, the working conditions of each part is different, and the degree of damage is also different. In the process of use, generally have to repeatedly remove the working layer, and the permanent layer is more intact, it will not be replaced.
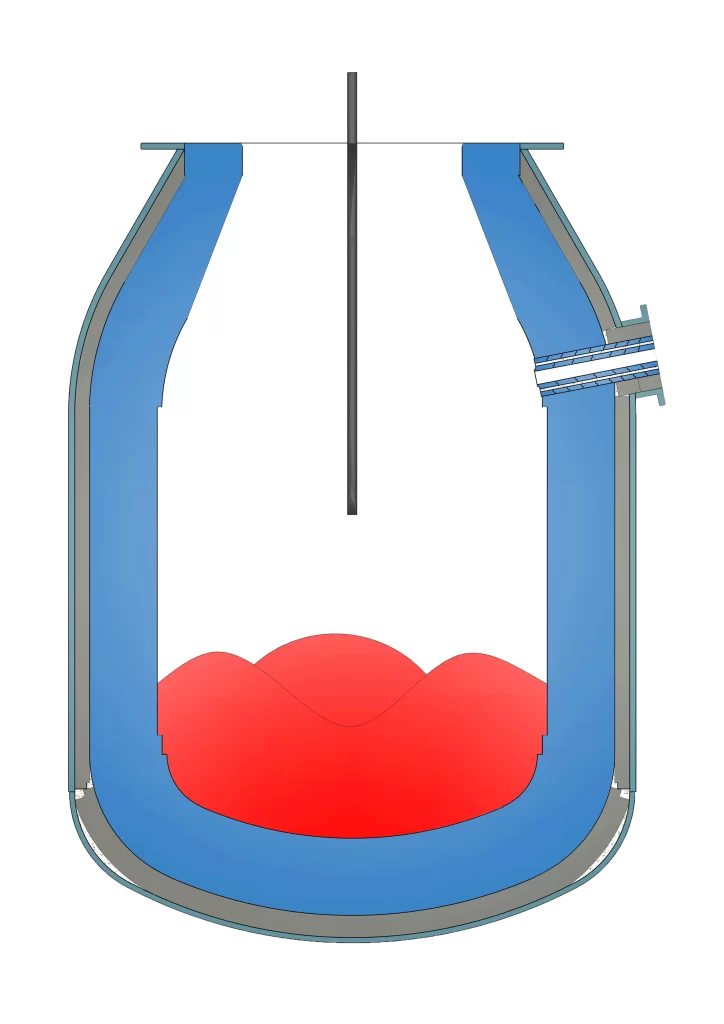
2.Technological advances in refractory materials for converter applications
Furnace age is an important technical index of converter steelmaking. Improving furnace age not only reduces the production cost, but also improves the production efficiency. The refractory material of converter lining is the main factor affecting the age of furnace, in recent years, through the development and research of scientific and technological personnel, the life of the lining has been significantly improved, and the unit consumption of refractory material has been reduced to 2~0.38 kg/t steel. Specific measures are as follows.
1.Comprehensive and balanced masonry furnace
For different parts of the erosion of different parts of the furnace lining, choose 3 to 6 different grades of magnesium carbon bricks, respectively, masonry in the slag line, trunnion, furnace wall, melt pool and other parts, in order to seek the best economic benefits. The most serious erosion parts, masonry quality of the best brick. Lining are used magnesium carbon bricks dry masonry, or mud masonry some carbon containing magnesium dolomite bricks, these bricks have different degrees of expansion at high temperatures, do not have to masonry too close. Each part of the working conditions are roughly as follows:
(1) the mouth of the furnace temperature changes dramatically, slag and high-temperature furnace gas scouring, charging and cleaning residual steel residue, the mouth of the furnace by the impact, therefore, the requirements of magnesium-carbon bricks have a high resistance to thermal shock and slag, and not easy to stick to the slag;
(2) the furnace cap by the slag erosion is the most serious, and at the same time by the rapid change in temperature and the impact of the exhaust gas scouring, the magnesium-carbon bricks to use the stability of the thermal shock and good slag resistance;
(3) Charge side of the furnace lining in the process of blowing in addition to steel, slag scouring and chemical erosion, but also by the scrap steel loaded and molten iron into the impact and erosion, the requirements of masonry high slag resistance, high strength, high resistance to thermal shock of magnesium carbon bricks;
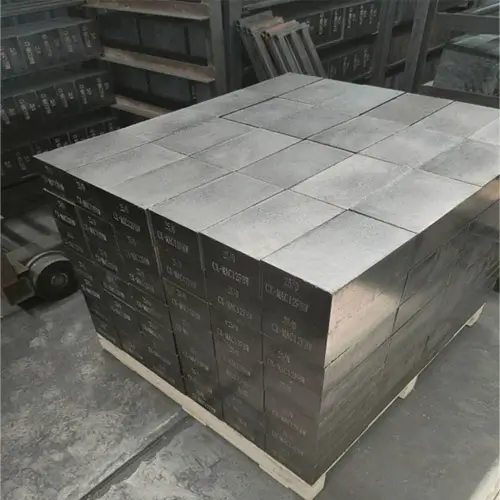
(4) out of the side of the furnace lining is mainly out of the steel by the steel thermal shock and scouring effect, the damage rate is lower than the charge side, such as the same magnesium carbon bricks with the same two sides can be a little bit thinner;
(5) slag line in the Blowing process of furnace lining and slag long-term contact, especially the slag side of the strong erosion by the slag, the furnace lining damage is more serious, to use good slag resistance of magnesium carbon bricks;
(6) trunnion parts of the furnace lining surface without a protective slag cover, magnesium carbon bricks in the carbon is very easy to be oxidized, and is difficult to repair, so we must build slag resistance, oxidation resistance of high-grade magnesium carbon bricks;
(7) molten pool and the bottom of the furnace by the erosion of the steel, but the damage compared to other parts is less severe, but the damage is less severe. Compared with other parts of the damage is light, can be built with lower carbon content of magnesium carbon bricks. If it is the top and bottom double blowing converter, the center part of the furnace bottom is easy to be damaged, and the same quality of magnesium carbon bricks can be built with the charging side.
2.Improve the quality of magnesium carbon bricks
It has been explained that magnesium-carbon bricks have excellent properties such as thermal shock resistance and erosion resistance, and are widely used for converter lining. However, in the process of use, it is found that the magnesium carbon bricks are easy to oxidize, resulting in deterioration of thermal shock and erosion resistance. Researchers have explored a new type of antioxidant self-repairing composite antioxidant: the use of metal Al, Si powder or Al-Si composite powder as an antioxidant, heat treatment or high temperature service in situ generation of Si C, AIN and other highly erosion-resistant material phases; but also add a variety of pre-synthesized nanocarbon, such as carbon black, nano-graphite oxide composite powders, the selection of suitable transition elements (Fe, Co, Ni) inorganic or organic compounds as catalysts, phenolic resin cracking to produce CO, C2H2, CH4 and other gases, under the catalytic action of transition metals, the formation of carbon nanotubes, carbon nanofibers and other low-dimensional graphitized carbon. Through these techniques, magnesium carbon bricks maintain good erosion resistance and thermal shock resistance.
3.Development of amorphous refractory materials for repairing furnace linings
In order to improve the service life of the converter lining, localized damage is readily repaired. The application of new type of non-shaped refractory materials and repair technology has significantly improved the service life of the converter lining, which is generally above 8,000 hearths, and in some cases above 20,000 hearths. At present, large-surface hot repair is commonly used to maintain the charging side, furnace bottom and steel outlet side. Spray patching material is used for the rounded corners of the melt pool and trunnions, and grout is used for caulking and maintenance of the outlet area when the converter outlet is replaced. Among them, the large surface repair material mainly has Mg O-Si O2 quality (also known as water-based large surface material), Mg O-C quality, Mg O-Ca O quality, etc.; spray patching material mainly has Mg O quality, Mg O-Ca O quality, Mg O-Cr2O3 quality, etc.. These unshaped refractories are divided into anhydrous patching materials (mainly asphalt, coal tar and asphalt powder, resin, etc.) and water-based patching materials (Mg O-Si O2-H2O combination and phosphate combination) according to the binding agent.
The use of organic materials such as coal tar, asphalt, and resin as binding agents has the problems of polluting the environment, long sintering time, and intolerance to erosion. Qin Yan et al [5] developed a carbon-free and environmentally friendly large surface repair material using high purity magnesium sand powder (Mg O97.02%) and medium block magnesium sand (Mg O94.80%) particles as the main raw material, and Si O2 ultrafine powder (Si O2=97.02%) as the binding agent. This water-based large surface repair material, the use of wet DC casting, high-temperature spreading good, high-temperature sintering process does not produce harmful gases, the formation of ceramic bonding, sintering time shortened by more than 50%, dense structure, oxidation resistance, resistance to scouring, after a number of use, the site without smoke and dust, service life is extended by 2 to 3 times.
For easy to damage the trunnion and slag line and other parts of the spray repair method. At present, the domestic common use of magnesium spray patching material [6], the service life is relatively low. Some people have developed a magnesium-carbon spray patch, the main raw materials for 3 ~ 0 mm magnesium sand (Mg O95.2%), 3 ~ 0 mm carbon (C = 94.2%), asphalt A (fixed C = 46.3%, softening point of 140 ~ 160 ° C), asphalt B (fixed C = 43.5%, softening point of 100 ~ 120 ° C) as well as additives and so on. After the actual use of its low rebound rate, good adhesion, high sintering strength, service life than magnesium spray patching material to improve 30%, reducing the number of converter repair.
There are also iron block slag furnace repair technology, is the use of iron block and high temperature liquid slag rapid heat transfer, and efficient cold solid bonding, the local weak parts of the repair, saving the cost of repairing the furnace material, slag operation saves the slagging material consumption, reduce the slow erosion of the furnace lining, improve the metal yield, and prolonged the life of the furnace lining. Fujian Sanan Iron and Steel Company [7] through the control of slag alkalinity, Mg O content, Fe O content and other parameters, the use of an appropriate amount of pig iron blocks to accelerate the cooling of slag, so that the slag mixed with pig iron block condensation bonded in the converter scrap, molten iron impact area, to achieve the purpose of replenishment of the furnace. This method can make use of the production gap to make up the furnace, a only 10 min, compared with the conventional make-up furnace to save more than 1 h, and very environmentally friendly.
In order to solve the mouth of the furnace, the furnace cap of the sticky slag problem, the use of a kind of anti-stick slag spray patch, is used after the regeneration of magnesium-carbon bricks as the main raw material, through the semi-dry spray patching construction, spray patching layer thickness of 35 ~ 50 mm, adhesion rate of 80% or more, and achieved a better use of the results.
4.Furnace protection
Through good operation to protect the furnace lining. 1990s the United States developed a successful converter slag protection technology, that is, after the end of the steel, the furnace liquid slag is not poured off, and to the furnace to add some light burned magnesium ball or dolomite material, so that the melting point of the slag and the viscosity of the slag to rise, through the oxygen gun to the furnace to put nitrogen, so that the liquid slag splashed to the lining of the furnace, because of the composition of slag has a Mg O, the lining of the furnace has a beneficial effect. China’s promotion of splash slag furnace protection, furnace age increased by 3 to 4 times, generally more than 20,000 times, ton of steel refractory consumption decreased by 0.2 to 1.0 kg, make-up material consumption decreased by 0.5 to 1.0 kg / t, the utilization factor of the converter increased by 2% to 3%. Splash slag furnace protection than make-up furnace cost is low, but the use of the effect is not as good as make-up furnace, but also unstable.
5.Improvement of the life of the gas supply elements of the top and bottom re-blowing converter
The molten pool is stirred by blowing gas in the low part to improve the steel yield and steel quality. The gas supply element is divided into two categories: nozzle type and brick type. Brick type is the mainstream of the application, the brick type mainly has a diffuse type, ring slit type and through-hole type. Through-hole type air supply resistance is small, airflow adjustment range, airtightness, not easy to leak, metal tube on the brick has enhanced the role of the brick is not easy to spalling, cracking and other advantages, is the mainstream of development. Luonai hospital with high-purity magnesium sand, flake graphite as the main raw material, plus Al, Si powder and B4C antioxidant, with thermosetting asphalt modified resin as a bonding agent, add the right amount of asphalt powder of the ingredients, the mud mixing, with isostatic molding to prepare the Mg O-C quality gas supply components, the use of the results are: the erosion rate of 0.28mm/furnace, the highest service life of up to 2,113 furnaces. In order to reduce the carburization rate of stainless steel tube, improve service life, the surface coating greater than 1mm coating, so that the stainless steel surface to form a thermally stable, carbon-reduction-resistant dense protective isolation layer.
Shinagawa Refractory Company, Japan, has developed a gas permeable brick with high fracture toughness and excellent thermal shock resistance. Used in 220 t converter, compared with the traditional permeable bricks, the loss rate is reduced by about 40%, the converter runs 4000 furnace without replacing the permeable bricks.
Xuanshan Iron and Steel Group steelmaking plant used metal tube type magnesium carbon permeable brick, each brick embedded in 30 stainless steel tube, with 300 t brick press machine stamping molding. Breathable brick in the 80 t re-blowing converter low part of the blowing into the N2, Ar gas, converter age up to 5 000 furnace times, the low part of the gas supply with the age of the furnace synchronization, and strive to synchronize the 10 000 furnace times.
6.Adoption of slide plate slag blocking technology to improve the quality of slide plate
Sliding plate slag blocking technology is a new technology rapidly developed in recent years. Sliding plate slag blocking equipment is similar to the ladle sliding spout mechanism system transplanted to the part of the converter outlet, to open or close the outlet by mechanical or hydraulic control, to achieve the purpose of slag blocking. Sliding spout slag blocking technology has outstanding advantages in improving molten steel yield, reducing inclusions in steel, improving molten steel cleanliness, reducing ladle slag sticking, and prolonging ladle life.
The inner spout is connected to the end of the spout brick and the upper spout slide plate, while the outer spout is connected to the lower spout slide plate. Inner/outer spout and slide plate should have better resistance to slag erosion, high-temperature oxidation resistance, thermal shock resistance and other properties, the slide plate should also have wear resistance. At present, the outer spout is mainly non-burning magnesium carbon, non-burning aluminum zirconium carbon and zirconium oxide (inlaid core) products, most of the non-burning spout through the asphalt impregnation treatment, the service life of 30 ~ 90 furnace times.
The service life is low, some studies have shown that the introduction of expanded graphite, Si powder can promote the formation of Si C whiskers in the brick, improve the toughness of the skateboard, resistance to crack expansion, improve the thermal shock resistance of the skateboard, and extend the service life.
Luonaiyuan summarized the causes of slag slide damage, and found that the upper slide in contact with steel, mainly erosion and expansion damage, and the lower slide in contact with the outside air, mainly thermal shock crack expansion damage. Therefore, through the process of inlaying zirconium ring on the upper slide plate and zirconium plate on the lower slide plate, the erosion and thermal shock resistance of the zirconium ring and zirconium plate have been improved to stabilize the service life of the slide plate at about 20 furnace times. Development of 3 series of products to meet the needs of different working conditions.
3.The development trend and optimization technology direction of refractory materials for converter
The development of converter steelmaking technology promotes the technical progress of refractory materials, but some parts of the refractory service life and the use of the method is still unsatisfactory, the future development trend is:
(1) the development of high-performance, abrasion-resistant, thermal shock-resistant low-carbon magnesium-carbon bricks;
(2) the development of rapid sintering, non-polluting environmentally friendly hot patching material, long-life spray patching material and good repair methods;
(3) the development of flame spray patching, large water-based Semi-dry spray patching material, although no soot, but there is moisture, easy to produce steam, to the bonding of the work surface and the use of hidden dangers, while the flame spray patching and the work surface immediately fused and sintered into a single body, a short period of time, long service life;
(4) the development of the furnace cooling process to further improve the life of the furnace lining, sputtering slag to protect the furnace, the age of the furnace, but the furnace age of the furnace lining, but thinned, the furnace shell will be deformed, the cooling technology can inhibit the deformation of the furnace shell to increase the life of the furnace shell To 10 ~ 15 years;
(5) the development of long-life composite blowing gas supply components, such as composite gas supply components, optimize the bottom air outlet structure arrangement, adapt to the top and bottom of the double blowing, low oxygen out of the steel, the low part of the powder spraying, the low part of the oxygen supply, the low part of the blowing of CO2 and other advanced technologies;
(6) to improve the performance of slag sliding performance and structure, such as composite sliding, etc., to extend the service life, reducing the number of times of replacement;
(7) the development of lightweight energy saving type and has a good Develop lightweight and energy-saving refractory materials with good high-temperature performance;
(8) Research and develop long-life water-cooled hoods, flues and other ancillary equipment.