Aluminum-magnesium refractory castable is a cutting-edge lining product that is currently widely used in ladles. Refractory material workers at home and abroad have done a lot of work on aluminum-magnesium castables, mainly introducing the factors affecting the performance of aluminum-magnesium castables from several aspects such as aggregate, magnesia, corundum fine powder and powder, and silica powder.
1.Aggregate selection
Aggregates play a skeleton role in refractory materials. The alumina aggregates used in aluminum-magnesium refractory castables mainly include fused alumina, sintered alumina and natural bauxite clinker. ]The effects of high-alumina bauxite clinker, high-purity fused corundum and electrometallurgical bauxite corundum on the performance of aluminum-spinel castables were studied. The results showed that the castable with fused high-alumina corundum as aggregate had the best fluidity, while the thermal shock stability of bauxite spinel castables was the worst. Starting from the selection of aggregates for aluminum-magnesium castables for ladle, the effects of three aggregates, fused white corundum, brown corundum and special grade bauxite clinker, on the performance of aluminum-magnesium castables were studied. The results showed that the brown corundum aggregate sample had the best fluidity. In terms of thermal shock stability, the white corundum aggregate sample was the best, followed by the brown corundum aggregate sample, and the bauxite clinker aggregate sample was the worst. The performance of replacing the 88-grade high-aluminum material with the 88-grade homogenized material and the 85-grade homogenized high-aluminum material with the 88-grade high-aluminum material was studied. It is pointed out that it is more profitable and feasible to use only 85-grade homogenized material to replace slightly higher-grade high-aluminum materials for 3~1mm, 1~0mm and fine powder.
2.Selection of corundum fine powder
Al2O3 in the fine corundum powder can react with CaO in the slag to form high melting point CA2 and CA6. At the same time, the presence of cation defects in the aluminum-rich spinel can capture FeO and MnO in the slag to form (Mg,Fe,Mn)O·Al2O3. The SiO2 content in the slag increases, and the viscosity of the slag increases, thereby improving the sample’s resistance to slag erosion and slag penetration.
The effect of alumina fine powder on the formation of spinel in aluminum-magnesium castables was studied. The results showed that when the castable contains active alumina, magnesium oxide is used as the substrate for spinel formation, and sufficient alumina can be obtained from the active alumina to form magnesium-rich spinel through diffusion; on the other hand, sintered alumina is not very active. When alumina and magnesium oxide come into contact, time for mutual diffusion is required. Due to the contact area of diffusion, aluminum-rich spinel is generated at this time, which has better slag resistance. At the same time, sintered alumina is cheaper than active alumina, so it is better to use sintered alumina. Adding an appropriate amount of active α-Al2O3 powder to the aluminum-magnesium castable can increase the density of the sample, thereby improving the slag resistance of the castable. A high-purity aluminum-magnesium castable combined with ρ-Al2O3 was prepared. The results showed that compared with the castable combined with pure calcium aluminate cement, the matrix of the castable combined with ρ-Al2O3 was purer and the service life of the castable was extended.
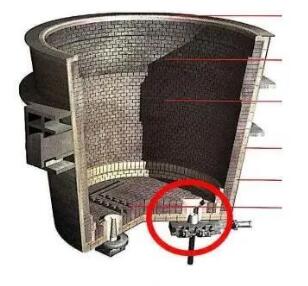
3.Spinel Proportion
The chemical formula of magnesium-aluminum spinel is MgO·Al2O3, and the theoretical content is MgO28.3%, Al2O371.7%. The ratio of synthetic magnesium-aluminum spinel, that is, the molar ratio of MgO/Al2O3, directly affects the performance of the generated magnesium-aluminum spinel. Magnesium-rich spinel usually has a MgO/Al2O3 ratio greater than 1, and the structure is relatively dense; while aluminum-rich spinel has more pores in the crystal. This may be related to the different growth mechanisms of the MgO side and the Al2O3 side during the growth of spinel. In actual production, the MgO/Al2O3 ratio of synthetic spinel should be determined according to its purpose. Magnesium-rich spinel is usually used as the kiln lining of large cement kilns. Aluminum-rich spinel is often combined with Al2O3 raw materials to mainly manufacture large and medium-sized ladle castables or prefabricated parts and ladle air bricks, seat bricks and other special parts. The alumina-based spinel castable synthesized from natural raw materials is mainly used for small ladle castables.
4.Magnesia content
Magnesium oxide, as the main raw material for in-situ spinel generation in aluminum-magnesium castables, has a significant impact on the strength, volume stability, slag resistance and thermal shock stability of the sample. In addition, since MgO is easily hydrated, magnesia also has a significant impact on the construction performance of the sample.
The effect of magnesia fine powder content on the slag resistance of aluminum-magnesium castables was studied. The results show that as the addition amount of magnesia increases, the slag erosion resistance of the sample decreases and the slag penetration resistance increases. However, when too much magnesia is added, the material structure becomes loose, resulting in a decrease in slag resistance. The effect of the content of fused magnesia on the properties of unburned alumina magnesite materials was studied, and it was pointed out that the starting temperature of the reaction to generate spinel is 1050°C. By adjusting the size and addition amount of magnesia particles, it can effectively prevent the material from peeling, bulging and Penetration of slag. Based on the use of my country’s abundant high-alumina bauxite resources and the actual usage capabilities of small and medium-sized steel plants, the Al2O3-MgO series refractory castables were prepared using Shanxi Xiaoyi special-grade high-alumina bauxite clinker and fused magnesite as the main raw materials. Research shows that increasing the magnesia content in the matrix can improve the erosion resistance of the matrix, but the anti-penetration ability of the castable will decrease.
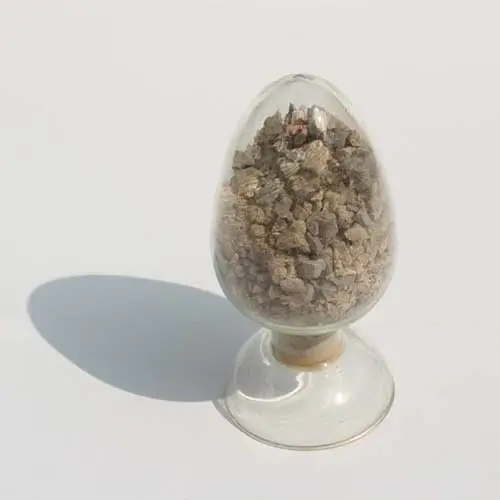
5.Silica Micropowder
Silica powder has an important impact on the performance of aluminum-magnesium castables, which is mainly reflected in: using silica powder in aluminum-magnesium castables can significantly reduce the amount of water added, inhibit magnesia hydration, increase fluidity, and improve Construction performance: On the one hand, adding silica powder will form a low melting phase (anorthite, anorthite, forsterite and rhodonite) with MgO, CaO, and Fe2O3 in the sample, which is detrimental to the high temperature performance of the sample. But on the other hand, it can be used to adjust the volume expansion accompanying the spinel reaction and accelerate the spinel formation reaction.
The relationship between microsilica powder and the phase composition changes and properties of high-purity aluminum-magnesium castables was studied. Studies have shown that if too much silica powder is added, the liquid phase will penetrate into the crystal grains or between particles of corundum, periclase and spinel at high temperatures, causing the castable to be overfired, leading to cracking and peeling. On the other hand, adding silica powder can improve the cold strength of the castable at different temperatures and reduce the residual expansion rate of the castable. On the basis of not increasing the cost, alumina-based ladle castables were prepared using special-grade alumina and fused magnesia as the main raw materials, and a combination of MgO-SiO2-H2O. It was pointed out that the addition of silica powder should be minimized to avoid significantly increasing the cost. The amount of water added to the castable shall prevail.