Refractory bricks are an important refractory material, widely used in various high-temperature industrial furnaces. For those who are not familiar with the refractory industry, they may think that refractory bricks are only square in shape, but in fact, there are many types of refractory bricks. In terms of material, the most commonly used refractory bricks include clay bricks, high-alumina bricks, lightweight clay bricks, lightweight high-alumina bricks and mullite lightweight bricks. The following will introduce these commonly used refractory bricks in detail.
1.Clay Brick
Clay bricks are made of clay clinker as aggregate and refractory clay (soft clay or semi-soft clay) as binder, with an Al2O3 content between 30% and 48%. It is a refractory product with wide range of uses and large output.
The properties of clay bricks vary depending on their chemical composition and production process. Generally speaking, clay bricks have the following properties:
- Chemical and mineral composition: Al2O3 content is 30% to 48%, SiO2 content is 50% to 65%, and also contains a small amount of alkali metal and alkaline earth metal oxides TiO2, Fe2O3, etc. Its mineral composition is generally mullite, cristobalite, quartz, and glass phases.
- Refractoriness: generally between 1580℃ and 1750℃, increasing with the increase of Al2O3/SiO2 ratio. When the content of low-melting impurities is high, the refractory resistance of the product will be significantly reduced.
- Load softening temperature: approximately 1250°C to 1450°C, with a wide range of changes. The starting deformation temperature is relatively low, about 200°C to 250°C different from the 40% deformation temperature.
- Linear expansion coefficient: lower, its thermal conductivity is also lower.
- Thermal shock resistance: good, with wide fluctuation range. The 1100°C water cooling cycle is generally more than 10 times, which is related to the low linear expansion coefficient of clay products, the insignificant crystal transformation effect and the plasticity at high temperatures.
- Resistance to chemical erosion: Because it is weakly acidic, it has strong resistance to acidic slag erosion, but weak resistance to alkaline material erosion.
Clay bricks are acidic refractory products, and their acidity increases as the SiO2 content increases. It has a certain resistance to acidic slag erosion, but has poor resistance to alkaline slag erosion. Therefore, clay bricks are suitable for use as linings of acidic kilns, and can also be used in blast furnaces, hot blast furnaces, glass kilns, carbon High-temperature kilns such as roasting furnaces.
2.High Alumina Brick
The production process of high-alumina bricks is similar to that of multi-clinker clay products, but the specific production process needs to be determined based on actual production conditions, raw material characteristics, product requirements and production conditions. Generally speaking, it is necessary to take measures such as strict classification of clinker blocks before crushing, graded storage and iron removal of granular materials, and fine grinding of clinker and combined clay.
High-alumina bricks have the following characteristics:
- Load softening temperature: The load softening temperature of ordinary high-aluminum refractory products is generally above 1420°C to 1550°C, which is higher than that of clay refractory products, and increases with the increase in Al2O3 content. When Al2O3<70%, its load softening temperature increases with the increase in the ratio of mullite phase to glass phase. The quantity and nature of the liquid phase have a significant impact on the load softening temperature. Therefore, reducing the impurity content in the raw materials is beneficial to improving the load softening temperature and high temperature creep properties; when Al2O3>70%, as the Al2O3 content increases, the load softening temperature does not increase significantly.
- Thermal shock resistance: The thermal shock resistance of ordinary high-aluminum refractory products mainly depends on the chemical mineral composition and microstructure, and is generally worse than clay products.
- Chemical corrosion resistance: Ordinary high-aluminum refractory products have good resistance to corrosion by acidic or alkaline slag and molten metal, as well as oxidation and reduction reactivity, and are enhanced as the Al2O3 content increases and the harmful impurity content decreases.
High alumina bricks are generally used in industrial kilns such as blast furnaces, hot blast furnaces, and electric furnaces.
The physical and chemical indicators of high alumina bricks are divided into several grades such as LZ-80, LZ-75, LZ-65, LZ-55, and LZ-48.
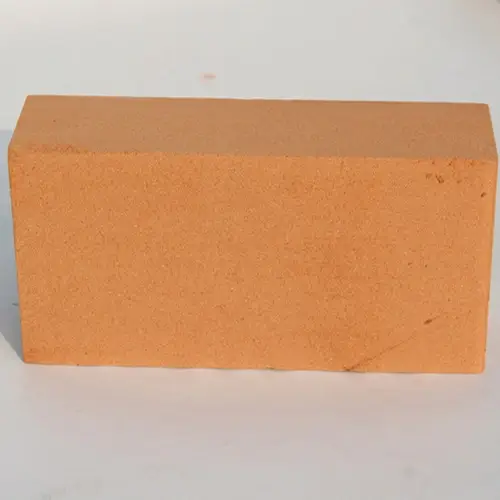
3.Lightweight clay bricks
Lightweight clay bricks refer to lightweight refractory products containing 30% to 46% Al2O3. They are made of clay clinker or lightweight clinker and plastic clay as the main raw materials. They are usually produced by the combustible method, and can also be produced by chemical method or foam method to form a porous structure. The ingredients are mixed with water to form plastic mud or mud, which is extruded or cast, and then dried and fired in an oxidizing atmosphere at 1250℃ to 1350℃. The volume density of commonly used lightweight clay bricks is 0.75g/cm3 to 1.20g/cm3, and the compressive strength is 2.0MPa to 5.9MPa.
Lightweight clay bricks are widely used, mainly as heat insulation materials in various industrial kilns that do not contact molten materials and corrosive gases, and the use temperature is 1200℃ to 1400℃. my country’s standard (GB3994-1983) divides lightweight clay bricks into ten grades according to volume density: NG-1.5, NG-1.3a, NG-1.3b, NG-1.0, NG-0.9, NG-0.8, NG-0.7, NG-0.6.
4.Lightweight high alumina brick
Lightweight high-alumina bricks generally refer to various lightweight refractory products containing more than 45% Al2O3, which are usually divided into two categories: one is ordinary lightweight high-alumina bricks made from natural high-alumina bauxite clinker as raw material; the other is lightweight high-alumina products made from fused or sintered alumina as raw material. Because its main crystal phase is corundum, it is also called lightweight corundum bricks.
Lightweight high-alumina bricks are generally produced by the foam method. The clinker is ground and mixed with a binder (such as clay) and a foaming agent to prepare mud, which is cast and sintered at 1350℃ to 1500℃. The volume density of general lightweight high-alumina bricks is 0.4g/cm3 to 1.35g/cm3, the porosity is 66% to 73%, the compressive strength is 1.3MPa to 8.1MPa, and the thermal conductivity is 0.291W/(m·K) to 0.582W/(m·K) (350℃).
Lightweight high-alumina bricks have high refractoriness and good thermal shock resistance, and are often used as high-temperature insulation layers for kilns. Lightweight high-alumina bricks can be used for kiln linings that are in direct contact with flames, but should not be used in places where they are directly corroded by slag. Since lightweight high-alumina bricks have good chemical stability in a reducing atmosphere, kilns that use gases such as hydrogen and carbon monoxide as protective atmospheres generally use lightweight high-alumina bricks as insulation linings. The operating temperature of lightweight high-alumina bricks is 1350℃ to 1500℃, and the operating temperature of high-purity products can reach 1650℃ to 1800℃. According to the Chinese standard, lightweight high-alumina bricks are divided into several grades such as LG-1.0, LG-0.9, LG-0.8, LG-0.7, and LG-0.6 according to volume density.
5.Mullite lightweight brick
Mullite-based lightweight bricks are a new type of heat-insulating refractory material containing between 50% and 85% Al2O3, with mullite (3Al2O3·2SiO2) as the main crystal phase and binding phase.
Because mullite has excellent high-temperature mechanical properties and chemical stability, mullite-based lightweight bricks have high high-temperature structural strength, low high-temperature creep rate, small thermal expansion coefficient, strong resistance to chemical erosion and good thermal shock resistance. With excellent performance, it can be used as the lining of the working surface of the kiln in direct contact with the flame, which can significantly improve the energy-saving effect of the kiln. The use temperature of mullite-based lightweight bricks ranges from 1350°C to 1700°C depending on the alumina content and volume density of the product.
6.Recycling Refractory Bricks
With the development of industry, the demand for refractory bricks has been increasing, and a large number of waste refractory bricks have also been generated. If these waste refractory bricks are not recycled, it will not only cause a waste of resources, but also pollute the environment. Therefore, recycling refractory bricks is of great significance.
There are mainly the following methods to recycle refractory bricks:
- Classification and recycling: Classify waste refractory bricks according to material, shape, size, etc. for subsequent processing and utilization.
- Crushing: Crushing the classified waste refractory bricks into small pieces for subsequent processing and utilization.
- Processing: Processing the crushed waste refractory bricks, such as crushing, grinding, screening, etc., to make them reusable refractory materials.
- Reuse: Use the processed waste refractory bricks to produce new refractory products, such as refractory bricks, refractory mud, refractory castables, etc., and can also be used in construction, metallurgy, chemical industry and other fields.
Recycling refractory bricks can not only save resources and reduce environmental pollution, but also reduce production costs and improve economic benefits.
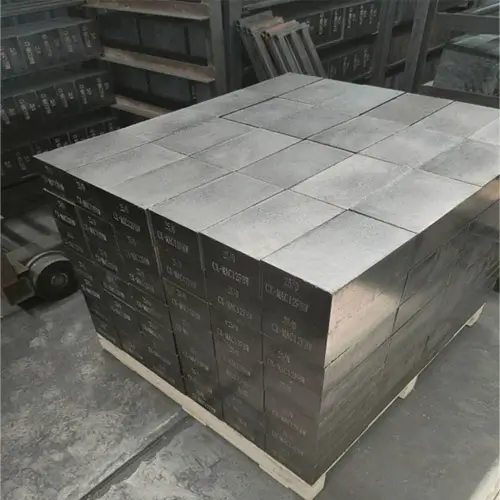