Only refractory materials with the following two characteristics can be used as the lining of the VOD furnace:
1) It can resist the erosion of high-temperature slag;
2) It has excellent resistance to spalling in a sudden cold and hot environment. At present, the refractory materials used in VOD furnaces are generally magnesia dolomite bricks and magnesia chrome bricks.
1.Magnesium Dolomite Brick
MgO is the main component of magnesia dolomite fire brick. When the impurity elements are less than 1.5%, its high temperature strength will be very good. The magnesium oxide composition of magnesia dolomite bricks designed and produced in Japan and some European countries fluctuates from 60% to 90%, but the sum of magnesium oxide and calcium oxide reaches about 98%. Magnesia dolomite fire bricks have more outstanding thermal shock resistance than magnesia chrome bricks, because the calcium oxide in the refractory bricks can form a new phase with a very high melting point with the slag, and the erosion of the refractory bricks will also be weakened. The calcium oxide in the fire lining can increase the wetting angle and strengthen the ability of fire bricks to resist corrosion by molten steel.
2.Magnesia Chrome Brick
VOD furnaces mainly use magnesia-chrome bricks with strong corrosion resistance at high temperatures as the inner lining of the ladle. In Japan, it is mainly constructed with different synthetic methods and different composition methods. Generally, the ring-bonded refractory bricks are mainly used in the part except the slag line, and the semi-recombined bricks are used in the slag line. Generally, the refractory fire bricks used in AOD and VOD use co-sintered magnesia chrome bricks because of its resistance to heat peeling and structural cracking. Its composition should be controlled within the range of SiO2<1.5%, Fe2O3<6%, Cr2O3>21% and CaO<1.0%. The content of Fe2O3, CaO and SiO2 must be within this range.
3.VOD furnace using MgO-CaO refractory materials
The lining of the refined ladle of VOD is made of refractory materials or MgO-Cr2O3 series refractories, and at the bottom, MgO–CaO series refractories or MgO–Cr2O3 series refractories are also used in addition to high aluminum. High-quality refractories, and refractories containing zirconium have recently been used. The use of MgO-CaO refractory materials on the lining of the V0D furnace can purify molten steel and also dephosphorize. Related research shows that when the content of MgO reaches 30-50%, the desulfurization rate is the highest. In the refining process, because dolomite contains CaO, it is desulfurized, so that the sulfur in molten steel is transferred to the slag with high sulfur content and low oxygen potential and lower viscosity.
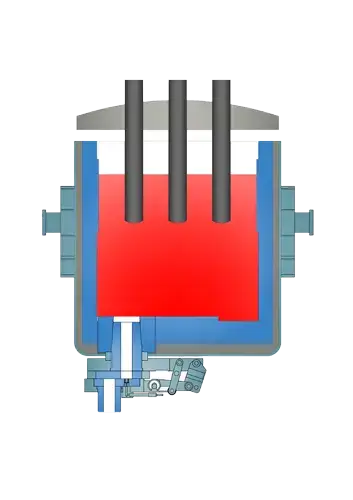
More details about ladle lining
What is ladle lining?
It is the refractory lining that stops the steel vessel from suffering damage when the ladle is used to transport metals with high melting temperatures that, if the molten metal came in direct contact with the ladle shell, would rapidly melt through the shell.
What materials are used in ladle lining?
Types of refractory materials: Various types of refractory materials are used for ladle linings, including high alumina, magnesia-carbon, alumina-magnesia-carbon, and spinel.
What is ladle refractory?
In the realm of refractories, the ladle is a term used for a vessel that is capable of withstanding extremely high temperatures of molten metals. This vessel is the primary medium to carry and transport these molten materials. As for the size of a ladle, it can hugely vary as per the requirement.