Induction furnace is the use of electromagnetic field induction principle of electrical energy into heat, so that the metal charge heat melting equipment, according to the structure is divided into core induction furnace and coreless induction furnace two categories.
Coreless induction furnace has the advantages of high efficiency, energy saving, low pollution, easy to adjust the composition, easy to control the atmosphere, strong heating capacity, can be intermittent operation, etc., and in steelmaking, foundry, non-ferrous metal melting precision alloy production and other aspects of widely used. Induction furnace is divided into different frequencies: industrial frequency induction furnace (50Hz or less); medium frequency induction furnace (50Hz-10000Hz) and high frequency induction furnace (10000Hz or more). In recent years, with the development of high-power thyristor frequency conversion power supply and improve the reliability of the intermediate frequency furnace gradually replace the industrial frequency furnace, compared with the industrial frequency furnace, the intermediate frequency furnace thermal and electrical efficiency, melting time is short, low power consumption, easy to realize the advantages of automation and so on. And induction furnace to large capacity, high power direction, the refractory material has higher requirements.
Refractory lining is an important factor in determining the yield of the induction furnace, the quality of castings and the safety and reliability of production and operation, to obtain good quality, long life refractory lining, first of all, we must understand the conditions of use:
(1) the thickness of the refractory lining is relatively thin, the lining of the temperature gradient is larger;
(2) electromagnetic stirring of the metal in the furnace, the lining of the refractory material produced by the mechanical etching;
(3) the refractory lining repeated rapid cold and heat Impact.
Therefore, the choice of refractory materials must have: high enough refractoriness and load softening temperature; good thermal shock stability; not with the metal and slag and other chemical reactions; with a certain degree of high-temperature mechanical strength; with good insulation and thermal insulation; there should be a good construction, high filler density, easy sintering, easy maintenance; refractory raw materials are abundant, inexpensive and so on. Induction furnace development and refractory material technology progress is closely related to the design of large-scale industrial crucible induction furnace, often from the choice of refractory materials and furnace lining simulation test. In any case, the choice of refractory materials for the furnace lining is based on the utilization and economy of the furnace as the main basis. For the sake of electrical close coupling, the thickness of the furnace lining is as thin as possible under the condition of striving not to affect the service life.
1、Coreless induction furnace structure and refractory lining construction method
1. Lining structure
The lining structure is made of copper tube with the coil on the outside of the lining. The traditional lining structure is to lay a layer of mica paper in the part immediately adjacent to the coil, followed by the alarm electrode, then a layer of asbestos sheet (cloth), and then a dry tamped lining. Dry tamping lining gradually forms sintered layer, transition layer and unsintered layer during baking and use, and the reasonable thickness of the three-layer structure is one of the important factors in determining the service life of the furnace lining. In order to meet the bottom-top-out furnace dismantling mode, the coil insulating cement appeared, and the cement replaces the mica layer, adding a layer of protective barrier to the coil. The mastic layer is generally thicker than the mica layer, but the thermal conductivity is higher than that of mica, so the lining structure containing mastic is called improved structure. Composite furnace lining structure is to adapt to the needs of some metal melting, with pre-fired crucible and filler instead of pounding the lining, this structure solves the dry material is difficult to sintering problems, while improving some metal melt or slag on the lining of the serious melting situation.
2.Types of refractory materials for coreless induction furnaces and construction methods for linings
(1)Pounding molding refractory lining: the use of mechanical or manual pounding lining, 5t the following induction furnace is mostly used in this way to construct the lining, it can be said that almost all coreless induction furnace with pounding material, the specific practice is: first in the inductor inside and at the bottom of a layer of asbestos sheet (or glass cloth), and then knotting the bottom of the furnace, after playing a good model of the crucible put (with 5 ~ 7mm steel welding), add a good mix of pounding material The crucible wall is pounded with air hammer or manually, and after knotting, the crucible is dried naturally first, and then baked with wood, and then baked with electricity. One of the model does not have to take out, inductively heated in the energized role in the melting of the first furnace with the charge to melt. There are also casting process molding, 100 kg to dozens of tons of capacity of the induction furnace is mostly used in this way.
(2) Prefabricated crucible or furnace tile: The molding and drying of the crucible or furnace tile lining are carried out outside the furnace. This time the coil is protected by insulating cement, and put into the crucible filled with impermeable dry refractory materials, known as composite furnace lining. This structure solves the problem of difficult sintering of dry materials at lower temperatures, and improves the situation where some molten metals and slag have a greater fusion effect on the lining. This method is suitable for induction furnaces with small capacity (generally below 200 kg). Because of the prefabricated crucible method of easy replacement of the lining, mostly used for experiments and smelting of special metals.
(3) Masonry lining: the lining of the induction furnace is made of refractory bricks in layers, which is mainly used for large induction furnace.
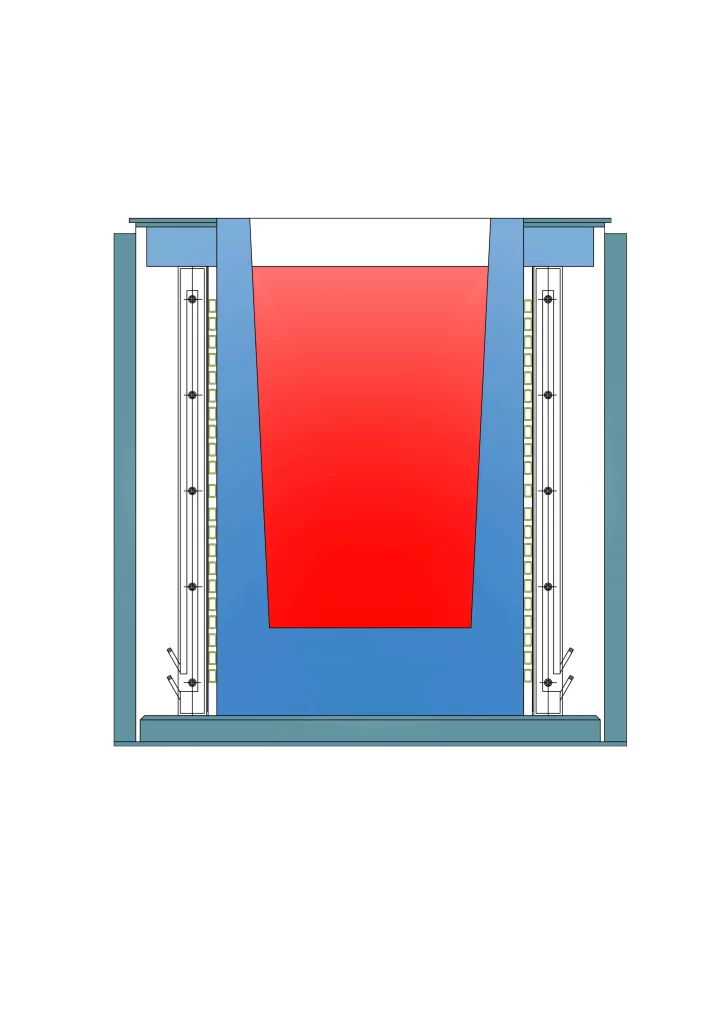
2、Selection of refractory materials for induction furnace
Induction furnace according to the type of molten metal, the nature of the slag, furnace capacity and operating conditions, such as the selection of different refractory materials.
1. Furnace lining refractories for melting and holding cast iron
Induction furnace can melt all kinds of cast iron, such as ductile iron, peristaltic cast iron and so on. In the past, most of the melting of cast iron using industrial frequency furnace, due to the medium frequency frequency induction furnace with high efficiency, energy saving and other advantages, in recent years the melting of cast iron more and more use of medium frequency or frequency furnace.
Cast iron induction furnace lining is generally used quartz pounding material, boric acid for the sintering agent of the acidic lining. Natural quartz in the use of the process due to the volume effect of crystalline transformation, the coefficient of thermal expansion is larger, poor thermal shock resistance, not suitable for intermittent operation of the furnace, the requirements of the furnace operation can not be emptied, continuous operation is better. At present, the domestic life of such furnace lining in the 60 ~ 150 furnaces, some can reach 200 furnaces. It is worth mentioning: in recent years some places quartz lining service life significantly improved, mainly by using high purity, large grain quartz and different sintering agents.
Sintering process is mainly:
(1) Knotting the coil
Selection of insulating mastic evenly coated on the surface of the induction coil, mastic layer thickness of 8 ~ 15 mm, after drying with good insulating properties, in the coil insulation layer paved layer of asbestos sheet and a layer of glass cloth, paving the manual leveling compaction of the layers of materials, and then taut with spring ring up and down. When pounding quartz sand, move the spring ring one by one from top to bottom until the lining is knotted;
(2) Knotting the furnace bottom
Furnace bottom thickness of 280 mm, four times sand filling, must strictly control the thickness of sand filling is not greater than 100 mm / time, manual knotting each 30 min, slowly rotating around the furnace to change position, even pounding, to prevent uneven density. When the knot is knotted to the required height, scrape it flat and place the crucible mold. Must ensure that the crucible mold and induction ring concentric, and the bottom of the furnace combined tightly, adjust the peripheral gap uniformity with a wooden wedge card tight, to avoid knotting the lining wall displacement.
(3) Knotting the furnace wall
Furnace lining thickness 110 ~120 mm, batch charging, packing thickness not more than 60 mm/time, manual knotting for 15 min, until flush with the upper edge of the induction ring. The crucible mold is not taken out after knotting, and plays the role of induction heating during drying and sintering. There is also a reasonable baking and sintering process to obtain a three-layer structure (i.e., sintered layer, overlayer, loose layer) lining, and to do a good job of daily maintenance in order to achieve a high life of the furnace lining.
Fused silica sintering material is also used as acidic lining, especially abroad. Fused quartz has a small coefficient of thermal expansion, and the tamping material is characterized by good impact resistance. At the same time to overcome the natural quartz in the long-term use of the phenomenon of thicker sintered layer or even burned-through, retaining enough unsintered layer, to avoid crack penetration, to ensure the safe and stable operation of the induction furnace. This kind of tamping material is used in the lining of 50 kg-10 t induction furnace, the service life is 250~450 times, and the service life of 20 furnace lining reaches 300 times.
In addition, high alumina bauxite-based tamping material can also be used as the lining of molten iron induction furnace, and better resistance to thermal shock performance. With Al₂O₃ mass fraction of 55 ~ 66% of the three bauxite clinker, can meet the requirements of cast iron induction furnace lining.
2.Cast steel, special steel melting furnace lining refractory materials
At present, cast steel, special steel melting most of the use of 500kg below the medium frequency furnace, the village refractory materials were quartz (occasionally used), magnesium oxide, magnesium spinel dry battering material, service life of 50 ~ 150 furnace times. Magnesia pounding material is the lining refractory material with electrofused magnesia sand as the main raw material, which has high refractoriness, excellent erosion resistance, especially very stable to alkaline solution and slag. However, its coefficient of thermal expansion is large, high sintering temperature, in the process of use due to expansion and contraction, the lining will produce cracks and spalling, therefore, magnesium battered material is more suitable for the use of the furnace below 500 kg. Magnesia spinel pounding material is made of magnesia sand as the main raw material, adding appropriate amount of spinel, due to its coefficient of thermal expansion is less than that of magnesia, while the secondary spinelization in use makes the material expand, which can inhibit the generation and development of cracks, and the spinel has excellent anti-slagging, which can be used for the lining of induction melting furnace with a capacity of 1 t or so.
At present, the capacity of more than 1t melting and holding furnace gradually increased, and to the multi-species melting, high-temperature melting and high-power rapid melting direction, so that the use of induction furnace lining conditions are extremely harsh. Therefore, large-scale cast steel, special steel melting on the induction furnace lining refractory performance to put forward higher requirements. Therefore, the requirements of cast steel special steel melting furnace lining refractory materials must have excellent high temperature performance, that is, erosion resistance, contact with the heated surface of the steel does not produce cracks, does not occur seepage liquid leakage of liquid steel and other issues. In order to meet these requirements, the general choice of electrofused white corundum or dense corundum, adding the appropriate amount of magnesium sand or aluminum-magnesium spinel, with this corundum-spinel-quality pounding material, in the large-scale molten steel induction furnace to promote the application. Fused corundum has good refractory performance, strong erosion resistance, compared with magnesite or spinel, corundum thermal expansion coefficient is small, thermal volume stability, etc., at the same time in the use of the process of generating a second spinelization of the volume expansion can effectively inhibit the generation of lining cracking. Therefore, the use of aluminum spinel tamping material lining, lining hot surface cracking to obtain control, microcracks significantly reduced. The service life of this material in 3t~5t induction furnace is 200~400 furnace times.
3.Refractories for copper and copper alloy melting furnace linings
For general copper melting furnaces, quartz, high alumina bauxite, mullite and corundum materials can meet the requirements. Because of the low cost of quartz tamping material, and easy to build the furnace, in the 300 ~ 700kg furnace can be used up to 200 times. Continuous use of large coreless induction furnace can be used on the use of mullite or high alumina mastic or castables, continuous service life generally up to one year and above. When the working temperature increases, the use of more demanding conditions, available corundum lining. In recent years, foreign countries have appeared more than 30t large coreless induction furnace, China’s Suzhou Copper Factory 16t frequency melting copper furnace using corundum lining materials, add anti-seepage agent, and copper in the Mn, Ni, Al, etc. do not react, does not occur slag, service life of more than 3 years (more than 700 times). Copper for the copper alloy in the permeability of a strong, melting point of 1083 ℃, melting, the melt to the lining of the internal infiltration, oxidation and accompanied by volume expansion and the generation of low melting point material, the occurrence of melting phenomenon, reducing the service life of the lining material. In 30 t of molten copper induction furnace, melting nickel-aluminum bronze, the highest temperature of 1350 ℃, the use of critical particles up to 10 mm mullite pounding material, the use of good condition.
There are also pre-synthesized graphite crucible or silicon carbide crucible, the advantage is that it can be quickly replaced to save sintering time, improve the electrical efficiency of the induction furnace, so the temperature inside the crucible is also high, saving energy. However, compared with corundum pounding material, the cost is high, and the stirring effect inside the crucible is reduced, which is unfavorable to the uniformity of the furnace temperature.
4.Refractories for Aluminum and Aluminum Alloy Melting Furnace Linings
Metallic aluminum and aluminum alloy is a very strong reducing agent at high temperature, although the melting temperature is not high (furnace temperature does not exceed 850 C), but the viscosity of the aluminum liquid is very low, the lining refractory material has a strong wetting and permeability. Therefore, the lining refractories require high thermal shock resistance and resistance to aluminum liquid permeability. At present its furnace lining refractories are mainly:
(1) Casting or wet pounding of high alumina, mullite lining, its general construction and baking cycle is longer, requiring continuous work, the use of better results, the service life is generally more than one year.
(2) Composite lining: that is, the hot surface using pre-fired crucible or furnace tile, coil protection with insulating mastic, filled with anti-penetration, stop leakage of dry refractory materials. The use of better results.
(3) Quartz, mullite, corundum and other dry pounding material, is the most widely used aluminum melting furnace lining materials, although the service life is not as long as the first two materials, but the use of stable.
5.Refractories for nickel melting furnace linings
A non-ferrous metal company has several 1t coreless medium frequency induction furnace production of water quenching nickel, the use of the inner village refractory material by the metal liquid electromagnetic stirring effect of mechanical scouring, but also by the rapid cold and hot repeated intense cycle, and nickel liquid has a very strong penetration, often the bottom of the furnace burn through and the coil fire accident, the service life of a dozen furnaces. A refractory group of companies through the magnesium, magnesium spinel, aluminum spinel pounding material of in-depth and detailed experimental research, concluded that aluminum spinel pounding material is more appropriate.
3.Induction furnace maintenance and repair
Maintaining the induction furnace lining and making appropriate repairs is an important way to improve service life.
1.Induction furnace lining damage is roughly:
(1) Thermal stress cracking, due to the thin thickness of the lining, the inner side is in contact with the high temperature metal liquid, and the outer side is close to the water-cooled coil, the temperature difference between the two sides is very large, coupled with the cyclic hot and cold cycles, resulting in thermal stress cracking of the lining;
(2) Erosion by metal liquid and slag, especially electromagnetic stirring and overheating caused by mechanical erosion;
(3) Spalling, due to thermal stress or mechanical collision and other reasons, resulting in the lining material in the form of blocks or flakes from the lining surface;
(4) Infiltration and slagging.
2.Induction Furnace Maintenance
Maintenance and repair work is very important, not only can timely detection of various hidden dangers, to avoid major accidents, but also to ensure safe production, prolong the service life, improve the quality of castings, reduce production costs. Daily production should pay attention to the following points:
(1) The raw material added to the furnace for melting must be clean, in order to prevent the charging process from scratching the furnace lining, the size of the raw material should not be too large, and do not directly hit the bottom of the furnace.
(2) Continuous melting, not out of the net metal liquid, to leave about 10% to protect the lining. Pay attention to prevent the melting temperature is too high, etching the lining. Stick in the lining of the slag, to clean up in a timely manner, once a week to measure the size of the furnace, found that the problem is dealt with in a timely manner.
(3) Regularly record the parameters of the relevant electricity, cooling water temperature and shell temperature of the key parts of the furnace body, and monitor the use of the furnace at any time.
(4) Daily observation of the water pressure gauge, water temperature gauge and water flow and the aging of the hose, found that the problem is dealt with in a timely manner.
(5) Stage melting is completed, the furnace body covered with a heat preservation cover to prevent the furnace body from cooling too quickly, resulting in deep cracks. When the furnace body produces large cracks or serious erosion, remove the damaged part of the sintered layer, knot repair.
3.Induction furnace repair
Local damage to the furnace lining repair, not only to extend the service life of the induction furnace, but also save a lot of refractory materials, thermal insulation materials and insulation materials, reduce the furnace baking consumption of electricity, save man hours and furnace construction costs. Such as a 0.5 t medium frequency induction furnace with aluminum spinel lining, melting aluminum silicon manganese alloy, general service life of about 50 times. When the use of 40 furnace or so using silicon powder combined with magnesium repair material on the lining of the cracks flaking and erosion of the serious parts of the coating repair, repair after the use of the residual heat of the furnace for 10 min natural drying, the use of smelting temperature for baking and high temperature treatment, found that the repair material and the original lining combined firmly. After two repairs can make the lining life increased to 90 ~ 100 furnace times.
There are many kinds of repair methods, depending on the damage of the lining, flexible use. Roughly, there are small repair, medium repair, repair, less than 1 mm of cracks can not repair, more than 1 mm of cracks, especially in the horizontal direction of the cracks must be repaired, can be added to the boric acid refractory material after sieving, with wire and other tools to fill in, and in the patch after the surface of the wet mix of sand with water glass smoothing. If there is a small range of erosion or damage, after removing the slag and residual iron, coated with water glass, and then patched with a good mix of refractory materials with the addition of water glass, or with an unshaped refractory material containing Al₂O₃.
Medium repair has the following kinds:
(1) Hot patch method: commonly used in the mouth of the furnace, the original lining of the loose in addition to remove, clean up the height and diameter of the appropriate mold into the bowl-shaped slope, adding bulk refractory material pounding, first sent to the low-pressure electricity 3 ~ 4 h, and then sent to high-pressure electricity chemical material.
(2) Cold patching method: repair the furnace after cooling. There may be the following cases:
① Large area of local damage, in addition to the replacement of the oxide layer, put the appropriate crucible mold, filled with the original lining material pounding, according to the old furnace baking curve baking furnace; ② the whole furnace lining thinning, first of all, will be the oxidation layer of the lining of the eradication of stripping, the bottom of the bottom of the put pounding material pounding, and then into the overall furnace liner, and then into the pounding material batch pounding, finished according to the new furnace baking; ③ the bottom of the “elephant foot” part of the repair, the original sintering layer cut (do not have to shovel all the way out, put into the crucible with material pounding can be. Elephant’s foot” part of the repair, the original sintered layer cut (not all shoveling), into the crucible, add material pounding can be.
(3) Induction coil repair: clean up the broken place, and then evenly coated insulation cement, general cement is added refractory cement, is a water-hardened substance, dry too slow, easy to flow deformation, dry too fast, can not be repaired, so we must master the cement of the initial and final setting time.
Repair is simple and easy, can be repeated continuously, after repair can be up to the effect of the new lining, greatly extending the service life. If the repair repeatedly extended indefinitely, may be able to do the induction furnace with refractory material zero emissions, energy saving and environmental protection. It is recommended that the induction furnace using spray patching technology for medium repair, the efficiency will be better.
The so-called overhaul, that is, remove all the refractory materials, rebuild the furnace.
Conclusion
Refractories for coreless induction furnaces are selected according to the type of metal to be melted, the nature of the slag, the size of the furnace capacity, the operating conditions and other factors. Cast iron and part of the cast steel, copper, aluminum and alloy melting furnace with acidic quartz refractories. Requirements for high purity (w (SiO₂) > 99%), crystalline particles, pounding material particles in reasonable proportion, the right sintering agent. The lining is knotted and solid. Cast steel and part of the cast iron, copper, aluminum and alloys, nickel melting furnace with high alumina bauxite and corundum spinel-based neutral and magnesium and magnesium spinel-based alkaline refractory materials, can be dry pounding or prefabricated crucible composite lining. According to the furnace capacity size, the use of conditions selected. Furnace fine maintenance, found that there are damaged parts of the timely repair, is to extend the service life of the induction furnace is an important way. Should be used to spray patching technology, mechanized operations, repeated spray patching, and strive to achieve zero discharge of refractory materials after use, to the direction of permanent lining.
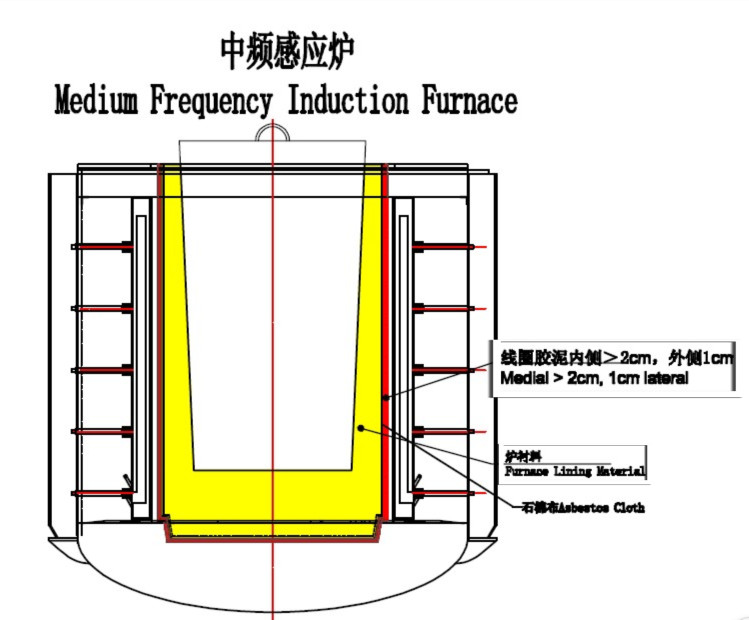