With the continuous acceleration of the industrialization process and the rapid growth of the economy, refractory materials, as key industrial raw materials, play a vital role in the field of high-temperature industry. In the process of widespread use and large-scale production of refractory materials, the environmental problems caused by waste refractory materials have become increasingly prominent. In particular, as one of the common refractory materials, alkaline magnesia refractory bricks will produce a large amount of waste materials during use, which brings considerable pressure to the environment. These waste alkaline magnesia refractory bricks, if not effectively treated and utilized, often become the source of environmental pollution, and also mean a waste of raw materials. Therefore, finding feasible resource utilization technology to convert waste alkaline magnesia refractory bricks into renewable resources can not only effectively reduce environmental pollution, but also contribute to resource conservation and sustainable development.
1.Characteristics and application prospects of basic magnesia refractories
Alkaline magnesia refractory materials play an important role in the industrial field with their unique characteristics. High-temperature stability is one of its distinctive features. It can maintain structural stability in high-temperature environments and is not susceptible to thermal shock and chemical erosion. Secondly, alkaline magnesia refractory materials have excellent alkali resistance, which makes them have good corrosion resistance in alkaline media and can be widely used in industrial equipment such as glass kilns and cement kilns. In addition, alkaline magnesia refractory materials also have good thermal conductivity and thermal conductivity, which can effectively conduct and disperse the heat in the furnace and improve the thermal efficiency and work efficiency of the equipment. With the continuous development of industrial technology and the improvement of performance requirements for high-temperature refractory materials, the application prospects of alkaline magnesia refractory materials will be broader. In the future, as the demand for high-temperature and high-refractory materials increases, alkaline magnesia refractory materials will be more widely used in steel, non-ferrous metals, building materials and other industries, providing more reliable guarantee for industrial production.
2.Preparation technology of basic magnesia refractory bricks
2.1 Selection and property analysis of magnesium raw materials
In the preparation of basic magnesia refractory bricks, the selection of magnesia raw materials directly affects the quality and performance of the final product. Common magnesia raw materials include light-burned magnesia, magnesium carbonate and serpentine. Light-burned magnesia has the characteristics of high purity and uniform particle structure, so it is widely used in the preparation of refractory materials. Its advantage is that it can still maintain a stable structure at high temperatures, resist thermal shock and chemical erosion, and is suitable for high-temperature industrial environments. Raw materials such as magnesium carbonate and serpentine are low in cost, but relatively speaking contain more impurities, so they need to be finely processed and treated. When selecting magnesia raw materials, factors such as its chemical composition, crystal structure and thermal properties need to be comprehensively considered to ensure that the final product has stable performance and excellent refractory properties.
2.2 Preparation method of basic magnesia refractory bricks
The impregnation method soaks the magnesium raw material in a solution containing specific additives, and the additives are evenly distributed on the surface of the raw material particles through adsorption and penetration, which has a dense structure and good performance. The preparation process is simple and easy to control, and a uniform additive coating can be formed on the surface of the brick body, which improves the slag resistance and alkali resistance of the refractory brick. In addition, the impregnation method can also achieve fine regulation of the microstructure and crystal structure of the brick body, further improving the overall performance of the alkaline magnesium refractory brick. Pressing and sintering process is one of the important methods for preparing alkaline magnesium refractory bricks. In the raw material preparation stage, it is necessary to select suitable magnesium raw materials and add appropriate amounts of binders and other auxiliary materials as needed. In the molding process, the mixture is pressed by a mold to form a brick of the desired size and shape. The key to pressing and molding is to control the pressure and molding speed to ensure the density and uniformity of the brick, thereby ensuring the quality of the final product. After molding, the brick needs to be dried. The purpose of drying is to remove moisture from the brick to prevent cracks and deformation during the sintering process. The dried brick is placed in a kiln for high-temperature sintering. The sintering process is one of the most critical links in the entire preparation process. Its purpose is to make the various components in the brick react chemically at high temperature to form a stable crystal structure, thereby giving the refractory brick excellent refractory properties.
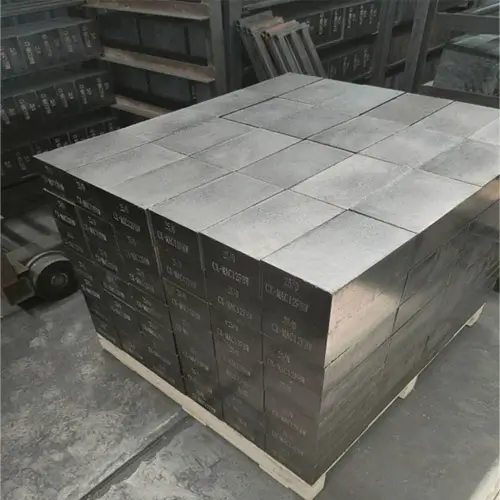
2.3 Refractory brick structure and performance control strategy
2.3.1 Additives to regulate structure
In the preparation process of alkaline magnesia refractory bricks, the selection and control of additives play a vital role in the structure and performance of the bricks. Additives regulate the microstructure and pore structure of the bricks by changing the chemical composition and crystal structure of the raw materials, thereby affecting their refractory performance and durability. By adding an appropriate amount of stabilizers and crystallization controllers, the growth and crystallization of grains can be effectively prevented, and the thermal stability and thermal shock resistance of the bricks can be improved. By adding an appropriate amount of fillers and expanders, the pores of the bricks can be effectively filled and compacted, the porosity of the bricks can be reduced, and its thermal conductivity and refractory performance can be improved. By adding an appropriate amount of anti-corrosion agents and anti-alkali agents, the bricks can be effectively prevented from being eroded by high-temperature atmospheres and chemical media, and their corrosion resistance and chemical stability can be improved.
2.3.2 Effect of process parameters on performance
In the process of preparing alkaline magnesia refractory bricks, the selection and control of process parameters have an important influence on the performance of the final product. Appropriate sintering temperature can promote the bonding between raw material particles and improve the density and mechanical strength of the brick body. However, too high sintering temperature may cause the grains to grow too fast, thereby reducing the thermal shock resistance of the brick body. Therefore, in the preparation process, it is necessary to accurately control the sintering temperature according to the characteristics and requirements of the specific materials to obtain the best brick performance. Properly extended sintering time helps to ensure the uniformity and stability of the internal structure of the brick body and improve its refractoriness and alkali resistance. However, too long sintering time may lead to increased energy consumption and reduced production efficiency. Therefore, it is necessary to reasonably control the sintering time while ensuring product quality to achieve economical and efficient production. Appropriate pressing pressure can promote the close bonding between raw material particles, improve the density and mechanical strength of the brick body, thereby improving its refractoriness and slag resistance.
3.Research on the recycling and resource utilization technology of refractory materials
3.1 Overview of recycling technology
3.1.1 Recycling and treatment methods of waste refractory bricks
In the recycling process of waste refractory bricks, common methods include crushing, pulverizing, and sorting. Use mechanical equipment to crush or pulverize waste refractory bricks to decompose them into smaller particles or powders. Use screening, airflow separation and other methods to sort the particles and separate materials of different particle sizes. For waste refractory bricks containing harmful substances, special treatment is required, such as chemical cleaning, heat treatment, etc., to ensure that the treated materials meet the requirements of safety and environmental protection. In the treatment process of waste refractory bricks, the treated waste refractory bricks are used as raw materials for the production of new materials. By adding appropriate additives and controlling process parameters, waste refractory bricks can be mixed with other raw materials to prepare new refractory materials or building materials, such as recycled refractory bricks, recycled concrete, etc., for use in construction, metallurgy and other fields. Another method is to heat treat waste refractory bricks to extract valuable substances, such as metals such as iron and aluminum, or convert them into alternative raw materials such as fly ash and slag for cement production or soil improvement. In addition to the above methods, waste refractory bricks can also be considered as fillers for roadbed construction, landfill covering, etc., to achieve simple and effective treatment and utilization.
3.1.2 Overview of resource utilization technology
In resource utilization technology, common methods include heat treatment, chemical treatment, physical treatment, etc. Heat treatment can convert waste refractory bricks into alternative raw materials such as fly ash and slag by high-temperature treatment. Chemical treatment can extract valuable metals or compounds such as iron and aluminum from waste refractory bricks through chemical methods, thereby realizing resource recycling. For example, by extracting the metal components from waste refractory bricks by leaching and extraction methods, and then refining and processing them, high-purity metal products can be obtained, realizing the reuse of valuable substances in waste refractory bricks. Physical treatment can achieve the recycling of waste refractory bricks by treating them by physical methods. For example, by using equipment such as vibrating screens and magnetic separators to screen and magnetically separate waste refractory bricks, materials of different particle sizes and compositions can be obtained, which can be used in different fields.
3.2 Key technology research and process optimization
3.2.1 Optimization of the treatment process of waste refractory bricks
The optimization of the treatment process of waste refractory bricks is a key link in achieving recycling and resource utilization. First of all, according to the characteristics and
treatment requirements of waste refractory bricks, it is necessary to design a suitable treatment process flow, including crushing, pulverizing, screening, magnetic separation and other links. Each step needs to be precisely controlled to ensure that the treatment process is efficient and environmentally friendly. Secondly, it is necessary to select appropriate treatment equipment and process parameters. For example, in the crushing and pulverizing links, crushers and pulverizers suitable for the characteristics of waste refractory bricks should be selected, and appropriate parameters such as speed and pressure should be controlled to ensure the uniformity and stability of particle size. At the same time, for waste refractory bricks containing harmful substances, special chemical treatment methods such as acid and alkali leaching and roasting are also required to transform or decompose harmful substances into harmless substances to ensure that the treated materials meet environmental protection standards. In addition, the optimization of the treatment process of waste refractory bricks also includes the simplification of the process flow and the reduction of energy consumption. By optimizing the process flow and reducing the processing steps and energy consumption, the processing efficiency can be improved and the production cost can be reduced.
3.2.2 Discussion on key technologies in recycling process
In the recycling process, key technologies include the following aspects: ① Efficient recovery and separation technology of waste refractory brick materials. Effective recovery and separation technology can improve the recovery rate of raw materials and reduce resource waste. For example, the use of technologies such as vibrating screens and airflow sorting can realize the particle sorting of waste refractory bricks, separate materials of different particle sizes and compositions, and provide a variety of raw material options for subsequent use. ② Recycling technology of waste refractory brick materials. Recycling technology is the key to converting waste refractory bricks into new materials or products. For example, through reasonable formula design and process control, waste refractory bricks can be mixed with other raw materials to prepare new refractory materials or building materials, such as recycled refractory bricks, recycled concrete, etc., for use in construction, metallurgy and other fields. In addition, heat treatment technology can also be used to convert waste refractory bricks into alternative raw materials such as fly ash and slag for use in cement production or soil improvement. ③ Environmental protection treatment technology of waste refractory brick materials. In the process of recycling, it is necessary to fully consider the requirements of environmental protection and take effective measures to reduce the impact on the environment. For example, efficient waste gas treatment equipment and wastewater treatment technologies can be used to effectively treat waste gas, wastewater and other pollutants generated during the treatment of waste refractory bricks, ensuring that the treatment process meets environmental protection standards.
4.Research on resource utilization technology of basic magnesia refractory bricks
4.1 Analysis of the characteristics of discarded alkaline magnesia refractory bricks
Waste alkaline magnesia refractory bricks are refractory materials that are eliminated or damaged after being used in high temperature and harsh environment. Waste alkaline magnesia refractory bricks have excellent refractory properties. Their main components are magnesium oxide and alkaline oxides, which enable them to maintain stable structure and performance at high temperatures. The chemical composition of waste alkaline magnesia refractory bricks is relatively complex. They may contain magnesium oxide, calcium oxide, iron oxide and other elements. The content and proportion of these components affect their performance. Waste alkaline magnesia refractory bricks may be affected by the use environment and process conditions, resulting in burnout, thermal shock cracks, etc., resulting in a decrease in their performance. Therefore, a detailed analysis of the characteristics of waste alkaline magnesia refractory bricks can provide an important reference for subsequent resource utilization. A deep understanding of its chemical composition, crystal structure and microstructure will help to select appropriate treatment methods and utilization methods to maximize resource reuse and environmental protection.
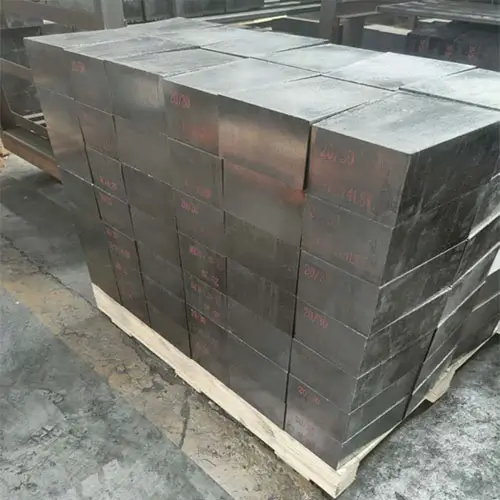
4.2.2 Recycling of waste refractory bricks to prepare new materials
Recycling and preparing new materials from waste refractory bricks Through reasonable process and formula design, waste refractory bricks are mixed with other suitable raw materials, and through molding, sintering and other process steps, new materials with certain properties and uses are prepared. In the process of recycling and preparing new materials, it is necessary to consider the characteristics and properties of waste refractory bricks and the requirements of the target products. According to the chemical composition, crystal structure, pore structure and other characteristics of waste refractory bricks, appropriate raw material ratios and process parameters are selected to ensure that the final product has good performance and stable quality. Through mixing, stirring and other process steps, the waste refractory bricks are fully mixed with other raw materials to form a uniform slurry or mixture. During the mixing process, additives or modifiers can be appropriately added to adjust the raw material ratio to improve the mixing performance and product performance. The mixture is molded. Common molding methods include extrusion molding, compression molding, injection molding, etc. Through the molding process, the mixture is molded into a shape and size that meets the requirements, preparing for the subsequent sintering process. The molded product is sintered. The sintering process is a key step in the entire preparation process. High-temperature sintering can combine the particles in the raw materials into a whole to form a strong new material. During the sintering process, it is necessary to control the sintering temperature and maintain a suitable insulation time to ensure that the structure and performance of the product are well guaranteed.
4.3 Process optimization and performance improvement
4.3.1 Process parameter optimization and control strategy
In the process of resource utilization of waste alkaline magnesia refractory bricks to prepare new materials, the optimization and control strategy of process parameters is crucial. According to the properties and requirements of raw materials, the process parameters are reasonably selected and controlled. For example, parameters such as pressure, temperature, speed in the molding process, and parameters such as sintering temperature and holding time in the sintering process need to be systematically optimized and adjusted. The optimization of process parameters can achieve efficient production and good performance of products. For example, in the molding process, by adjusting parameters such as pressure and temperature, the density and molding accuracy of the product can be controlled; in the sintering process, by controlling the sintering temperature and holding time, the performance indicators such as crystallinity and mechanical strength of the product can be adjusted. The use of automated control systems and online monitoring equipment can monitor and adjust process parameters in real time to ensure the stability and consistency of product quality.
4.3.2 Material performance improvement and process optimization
In the recycling process of waste alkaline magnesia refractory brick materials, material performance improvement and process optimization are crucial. Reasonable formula design and process optimization can effectively improve the performance of materials. For example, an appropriate amount of additives or modifiers can be added to adjust the composition ratio and structure of the material to improve the material’s strength, wear resistance, corrosion resistance and other performance indicators. At the same time, by optimizing the process flow and control parameters, the stability and consistency of the production process can be improved to ensure the stability and reliability of product quality. In the process of formula design and process optimization, environmentally friendly and renewable raw materials and additives should be selected as much as possible to reduce the impact on the environment. At the same time, by improving production efficiency and reducing energy consumption, effective utilization of resources can be achieved, production costs can be reduced, and economic benefits can be improved. Introduce advanced production equipment and technology, strengthen the automation and intelligence of the process flow, improve the accuracy and stability of the production process, and achieve effective control and improvement of material performance and production quality.
In the research on resource utilization of alkaline magnesia refractory bricks, by making full use of discarded refractory brick materials, we can not only effectively reduce resource waste and environmental pollution, but also promote the development of circular economy and realize sustainable utilization and recycling of resources. In the future, we will deepen the research on resource utilization technology of alkaline magnesia refractory bricks, continuously improve the technical level and innovation ability, and make greater contributions to promoting the green and sustainable development of industrial production. At the same time, we will strengthen the cooperation between industry, academia and research, promote the transformation and application of scientific and technological achievements, and transform scientific research results into actual productivity.