Refractory bricks and refractory mortar
(1) The working conditions of the mud in the joints of refractory masonry bricks are exactly the same as those of refractory bricks. Therefore, the main technical indicators of the two, refractoriness and chemical composition, should also be the same or compatible.
(2) The type and brand of mud should be selected by the designer according to the working conditions of the furnace.
(3) The types and compositions of mud generally used in refractory products.
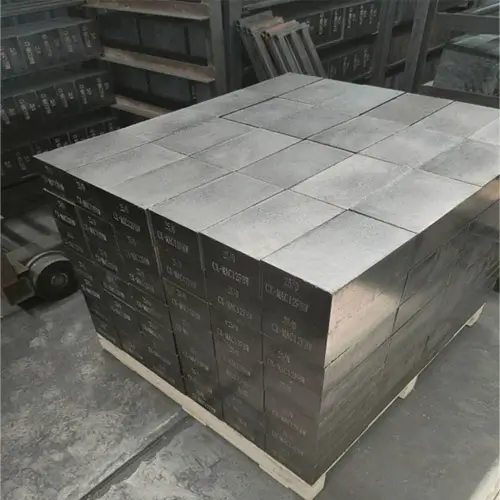
Refractory mortar consistency
Before refractory masonry is built, the consistency of the mud and the amount of water to be added should be determined through tests according to the type of masonry. Different types of masonry are suitable for muds of different consistencies. In recent years, finished muds mixed with admixtures have been widely used, basically eliminating the original ordinary refractory muds.
Bonding time
The bonding time of the mud depends on the material and size of the refractory product, and is preferably 1 to 1.5 minutes.
The determination of mud consistency should be carried out according to the method specified in the current industry standard “Test method for refractory mud consistency” YB/T 5121.
The determination of mud bonding time should be carried out according to the method specified in the current industry standard “Test method for refractory mud bonding time” YB/T 5122.
Maximum particle size of finished mud
Since construction units generally lack the necessary mixing, screening and testing equipment, it is difficult to accurately mix the ingredients and mix them evenly. Therefore, finished mud should generally be used instead of preparing mud on site. The maximum particle size of the mud should not be greater than 30% of the specified brick joint thickness.
Refractory mortar preparation
When preparing mud, various components must be accurately measured and stirred evenly. It is strictly forbidden to add water or binders to the prepared mud at will, otherwise the specified consistency or mix ratio of the mud will be changed, affecting its masonry performance and reducing its high temperature performance.
When preparing mud with admixtures in coastal areas, the stirring water should be tested and its chloride ion content should not be greater than 300mg/L. Because the higher the chloride ion concentration, the shorter the bonding time of the mud, the faster the solidification and hardening, which is not conducive to masonry operations. Secondly, the shear strength and flexural strength of the mud will decrease due to the increase in chloride ion concentration in the water.
Since cement refractory mud is a hydraulic mud, water glass refractory mud is an air-hardening mud, and brine and magnesia in brine magnesia refractory mud are chemically combined. These three kinds of mud will harden after being left for a period of time. It is stipulated that they should not be prepared too early and should be used up before the initial setting. If the mud has initial setting, it will lose its strength during masonry, so it should not be used again.
In recent years, the phosphate mud used in the construction site has rarely been prepared on site with phosphoric acid and high-aluminum clinker powder, and basically the finished mud produced by the factory is used. The finished mud is accompanied by a product instruction manual, which stipulates parameters such as the time of entrapment and the amount of water added, so it is not allowed to be diluted with water at will.
Mixers and slurry tanks
Since there are many types of mud in large-scale furnace construction projects, when preparing or using mud of different brands, mixers, mud tanks and other machines and containers must not be mixed, so as not to affect the masonry performance of the mud and cause a decrease in the high-temperature performance of the mud.
More details about refractory mortar
What is refractory mortar?
Refractory mortar is a mix of cement, sand, fireclay and, other specialized ingredients such as calcium aluminate. Fireclay is a set of various clays that can resist heat up to 3,000 degrees Fahrenheit. Just think of this as clay that has special heat resistant properties.
Is refractory mortar the same as fire cement?
Refractory cement is used for constructing or repairing the structural elements of a furnace or other high-temperature equipment, while refractory mortar is typically used for filling in gaps and joints between refractory bricks or other masonry units.
How do you make refractory mortar?
When you mix fireclay with Portland cement, sand, and lime, you create a product that is more heat resistant than basic mason’s mortar (Portland cement with sand and lime). Measure your ingredients by volume (use a bucket or shovel to measure), and mix only the amount you will use within an hour or so.
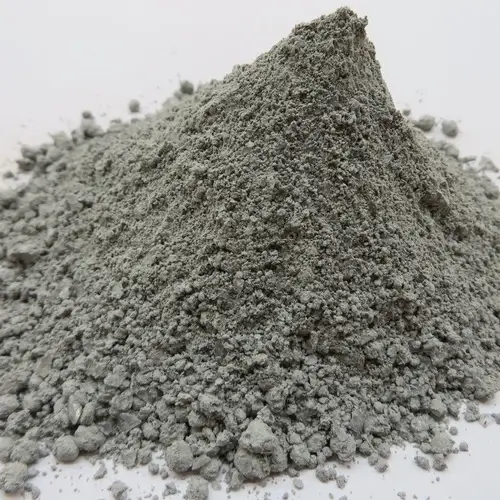