Many people buy refractory castables but do not know how to construct them in a standardized manner (see the refractory castable construction standards for details), what procedures are involved, and what details should be paid attention to during construction. As a result, the refractory castables have a short service life and often have problems. If you are still at this stage, quickly read the refractory castable construction process and construct according to the standards.
Refractory castable construction process steps
1.Anchors and formwork
a. The material of the anchor has a great influence on the quality of the castable. Generally, heat-resistant stainless steel 1Cr18Ni9ti is used. Ocr25Ni20 is used in high-temperature areas (above 1280℃). Both sides of the anchor are required to be fully welded and the welding should be firm. The surface should be painted with a 1-2mm thick layer of asphalt paint or wrapped with tape to offset its expansion under high temperature.
b. During the formwork construction, the formwork should be waterproofed, the surface should be smooth, and asphalt or engine oil should be applied on the surface. A layer of felt paper can also be applied to prevent it from absorbing moisture in the cast body, and it can also be easier to remove the formwork. The joints of the formwork should be dense to prevent leakage.
2.Stirring and adding water
a. The construction site and mixing container (forced mixer) should be clean and free of debris, and there should not be lime, sand and other debris mixed into the castables, which must be mechanically mixed, and it is forbidden to mix the castables of different numbers.
b. Each package of pouring material contains sachet powder, need to be pre-mixed for 1-2 minutes, mixing evenly before adding water for mixing; the weight of each mixing of pouring material should be controlled at 150-200 kg, mixing for about 5 minutes until the slurry to meet the requirements of the use of pouring material, but it should be noted that: the pouring material must be used in a whole bag to ensure the homogeneity of the pouring material, the pouring material must be used up within 15 minutes after adding water for mixing (counting from the time of adding water), and the specified time is not allowed to use. After adding water and mixing, the castables must be used up within 15 minutes (counting from the time of adding water). If the castables are not used up within the stipulated time or have been hardened, they can not be re-mixed and re-used, and should be firmly discarded.
c. The quantity of water added has a great influence on the quality of the castables, and should be strictly controlled, generally at 5%-8%; when adding water for the second time, it should be added slowly to prevent the water from being too much, and the water used for the construction should be clean drinking water (PH value between 6.5-7.5).
d. When constructing in summer, the casting material and mixing water should be avoided to be exposed to sunlight for a long time, and shade treatment should be taken, and the through temperature should be lower than 38℃; when constructing in winter, the casting material and mixing water should be put in the room, and the casting material should be stirred by using warm water and the time of maintenance in mold should be prolonged, and it must be ensured that the ambient temperature should be not lower than 0℃ in the period of casting and maintenance.
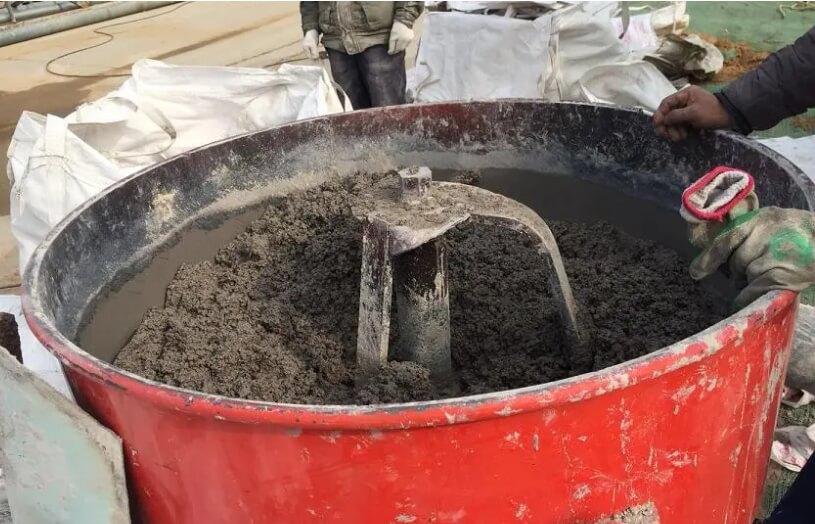
3.Pouring
a. Before pouring, the inside of the equipment should be cleaned up; when pouring a large area, the construction should be divided into pieces, and the area of each pouring area should be about 1.5-2m2, with a height of not more than 300mm; vibrate the material while adding material to make a large amount of air in the material overflow, and it is appropriate to see the surface of the material flooded with slurry; the vibrating rod should be pulled out slowly when moving out to avoid causing a hollow in the body of the material, and there is no interval between the 1m2 to reserve 2-3mm. Expansion joints, cross, shall not be missed.
b. Due to the dead space produced by some obstacles, it is difficult to install the template to pour, then it can be pounded manually in layers, and also can appropriately increase the amount of water added to the pouring material, and pay attention to not leaving any unpoured dead space.
4.Conservation
a, after pouring, the casting body generally need to take the mold maintenance for 24 hours, before demolding, after demolding natural maintenance for 24 hours is good.
b. After demolding, the quality of casting should be checked, and honeycomb, spalling, hollow should be repaired or reworked in time. If the problem is serious, the defective parts should be chiseled off to reveal the anchors, and then the same quality of casting material should be used to fill in and pounded, and it is forbidden to cover up the problem by cement smoothing. Non-engineering requirements of the concave and convex parts, should also be promptly repaired.
5.Baking
After the refractory castables have gone through the above maintenance process, they must also be baked in a fixed regime before use, with the specific heating curve being formulated according to the actual situation.
6.Attention
Instructions for storing potting compound:
- The potting compound should be stored in a dry warehouse without rain or moisture.
- The potting compound should be stored in a dry warehouse without rain and moisture.
- The best storage date for the potting compound is 6 months.
- The best storage date for the potting compound is 6 months. ⑤ The different numbers of potting compound must be stacked separately, keep the distance, and be well labeled.
Refractory castables winter construction process
a. Water for mixing, when the ambient temperature is lower than 5℃, warm water should be used for mixing materials for construction. Heavy casting water temperature can be controlled at 10 ℃ -50 ℃, light casting water temperature control at 10 ℃ -30 ℃. Implementation measures: in each construction mixing machine, make only 3 cubic meters of water storage tank, the outside with aluminum silicate fiber board insulation 200mm, will be provided by the owner of the fast boiler to heating low-pressure steam into the tank, the water will be heated to the appropriate temperature for mixing pouring materials.
b. Set up winter construction mixing workshop with heat preservation board, and install heaters in the mixing workshop, and utilize the heat source of quick-loading heating boiler provided by the owner for heating, in order to maintain the temperature of the mixing area above 0℃.
c, the preservation of materials: winter construction materials should be placed indoors or rain-proof shed, the site does not have the conditions, should be covered with a raincover tightly, snow days should be cleaned up snow.
d, in the construction area when the temperature is lower than 5 ℃ to take appropriate heating measures: when the construction work surface to stop construction with quilt or thermal insulation cotton felt cover, and increase the construction range of tungsten iodine lamps, or far-infrared heater or low-pressure heating steam into the construction work surface, in the cover quilt below the two rows of DN20 steel pipe drilling φ2 holes in the steam maintenance. At night, coal can be used for heating to increase the temperature. Coal can not be placed directly on the casting surface and boiler parts. It is necessary to use a large honeycomb coal stove or a coal stove made of iron drum. And a chimney must be installed to exhaust the smoke, and manned at night. During the daytime construction, the coal stove should be extinguished to prevent gas poisoning. Use insulating materials to cover the upwind part of the construction site to minimize the intrusion of cold wind. Close the doors and holes where no one and materials go in and out, and block all the holes at night when no one is working or when the construction has been completed, so as to prevent air convection and reduce heat loss.
Attention
Construction workers in the winter construction must wear good labor insurance products, Du wear plastic hard-soled shoes on the site and climbing scaffolding, after the rain and snow should be swept in a timely manner on the scaffolding and aisle snow and ice to prevent slippery and ice injuries.
Refractory castables construction process
1.Pre-construction preparation and strict inspection content
To be casting equipment and site cleanup; construction machinery with components intact; anchors material, type, size, layout and welding (fixed) quality, metal anchors for expansion compensation treatment; and surrounding refractory bricks and other casting material wet water precautions; pre-testing of the casting material is not lost; the quality of the water should be up to the standard of drinking water; the above acceptance of the experience and to ensure that the construction will not be interrupted.
2.Construction requirements
a. Mould making: made of steel plate or hardwood board, steel plate coated with mold releasing agent, wood board should be brushed with waterproof paint should not leak slurry, and should have enough strength.
b. Mixing: use forced mixer, pour the castables into the machine, dry mix for 2-3 minutes, add water and wet mix for 3-5 minutes, add water should be less rather than more, add water 7.0-7.5%.
c. Vibrating: Pouring the castables into the mold should be vibrated immediately with vibrating rod, and should not be omitted and vibrated in the same position for a long time and vibrated to avoid segregation and holes of castables. The stirred castables must be used up within 20-30 minutes from the time of adding water, and the initial material should be discarded. Expansion joints should be set according to the design.
d. Maintenance: After the surface of the castables is dry and reaches 70% strength before demolding, the demolding time is ≥24 hours, and the maintenance time is ensured to be ≥24 hours.
e, drying: according to different numbers and thickness of castable liner and site climate conditions, the user must provide enough baking time to ensure that the moisture excluded from the phenomenon of cracking. Requirements for the cumulative baking time ≥ 72 hours.
3.Cautions
a. Strictly control the amount of water, winter construction room temperature must be greater than 5 ℃, and have a set of anti-freezing measures.
b, must use forced mixer mixing, strictly prohibit manual mixing.
c. Anchor nail must be added expansion cap or brush asphalt paint.
d. This product is strictly prohibited to mix and match with other castables.
Refractory castables construction methods
1、Painting construction method
a. Apply the mixture directly on the working surface by manual application.
b. The furnace wall is coated continuously in layers from bottom to top, the height of each layer is 700~1000mm, the thickness of each coating is 50~100mm, and it can be coated continuously for several times, and when the thickness reaches the required size, it is compacted and wiped out with trowel, and it can be constructed for the second layer with natural maintenance for 3~4h after the construction of each layer.
c, the top of the furnace section continuous coating, two expansion joints for the section, each coated thickness of 30 ~ 50mm, can be coated continuously, until the thickness reaches the required size, with a trowel compaction wipe.
d, large-diameter horizontal pipe insulation lining layer, it is appropriate to use the first segmented construction lining, and then set up the connection method. When the pipe is constructed in sections, place the pipe horizontally, apply the lower half-circle lining layer first, and after 48h of natural maintenance, turn the pipe 180° to apply the other half-circle lining layer, and do the joint treatment after the pipe is connected. In the production of refractory castables often join some different diameters of fibrous products in which the fiber is what we refer to as heat-resistant steel fiber which is produced with stainless steel or heat-resistant steel containing chromium-nickel and other alloying elements. The manufacturing method is divided into: steel wire cutting and pressing method, steel block cutting method and steel melt pumping method. The first two methods of quality and stability, high strength, but more expensive: the latter method is simple, strange shape, strong grip, low cost, there are a number of production, and therefore widely used.
2、Pouring construction method
a. Layers and parts of the casting, can be cross-work. The furnace wall is poured in layers, the height of each layer is 700~1000mm. the furnace top is constructed in sections, and the top of the furnace between the two expansion joints should be poured at the same time.
b, according to the design requirements of the size of the support template, the template inside the layer of plastic film, mixing and pouring into the template, the fabric should be uniform, not with a vibrating rod vibration.
c, the density is not greater than 0.8g/cm3 of the casting material, after pouring with a trowel layered compaction, the density is not less than 1.0g/cm3 of the casting material, after pouring with a tool to compact pounding.
d, maintenance and demolding: ambient temperature is not less than 20 ℃, natural maintenance 4h can be demolded, the ambient temperature is not greater than 20 ℃, natural maintenance 5 ~ 7h can be demolded, demolding, such as the occurrence of local angular damage, can be repaired. After demolding, if there is local corner breakage, it can be repaired. The demolding time of the furnace top should be extended as appropriate.
In addition, the amount of steel fiber in the castable material should not be too large. Because too much steel fiber will make the high-temperature physical and chemical properties of refractory castables worse, such as steel fiber will make the castables by high temperature after burning the residual linear expansion. At the same time, the iron oxide content in the castable will increase, reduce its resistance to erosion, and affect the workability of the castable in the construction, so the selection of the amount of addition should be based on the type of kiln to use the part of the use of the temperature to judge the appropriateness.
3、Projection construction method
a, the mixture will be projected on the working surface by artificial projection method, layer by layer, when the thickness of projection reaches the design size, compacted and smoothed by trowel.
b. The lining layer of furnace wall and vertical pipe is constructed in layers from bottom to top, and the height of each layer is 700~1000mm, and the second layer can be constructed after natural maintenance of 3~4h after each layer is constructed.
c. This method is not applicable to the construction of lining layer on top of the furnace.
Preparatory procedures before the construction of refractory castables
Before the construction of castables, the working area and the surrounding environment must be enclosed and kept clean to prevent unclean substances from contaminating the refractory materials, and the tools and equipment used for construction should also be kept clean. The construction of refractory castables consists of three parts, i.e. mixing, pouring and maintenance. Here will be mixed and before the preparatory work as a refractory castable construction before the preparatory process, in this point introduces the following nine aspects.
1、Construction water and refractory castable water, should be used clean water. The water used for stirring span in coastal area should be tested, and its chlorine ion content should not be more than 0.03% (300ppm).
2、The mixing of castables and refractory castables should be mixed mechanically, and it is appropriate to use forced concrete mixer. Water glass refractory castables and phosphoric acid, phosphate refractory castables can be used oscillating mixing machine mixing, accompanied by artificial mixing. When changing the material number, the mixing machine and hopper, weighing container should be clean. The mixing time and the amount of liquid participation should be strictly according to the construction instructions. Mechanical equipment should be firmly installed, and the interval between mechanical equipment and pouring address should be shortened as much as possible. Mechanical equipment should be qualified after maintenance and debugging before use. It is necessary to measure the casting material according to the cooperation ratio, and it is necessary to pass the measurement verification for the scale, measuring cup and measuring cylinder. All kinds of appliances used in each construction link of refractory castables must be free of defects and clean, and should be moist with water before use.
3、Site view of raw materials
① Where the moisture caking cement shall not be used; there is a slight moisture phenomenon, but not caking (touching the bulk) of the unexpired cement, shall not be used for the main parts.
② different kinds of cement, such as mixing, shall not be used.
③ modulus and density of water glass and planning requirements do not match, should be adjusted; deposits should be filtered, and send samples for retesting.
④ all kinds of materials, such as moisture or powder mixed with other impurities, should be the second check, qualified before use.
⑤ All kinds of aggregate particle size and should match the set juice request.
4、Sampling and testing of raw materials
① Refractory castables raw materials such as no commodity certification or inspection statement, shall not be used; such as the site view of its quality in doubt, should be taken representative samples, sent to the department with the qualification of the analysis of the test.
② the results of secondary inspection, such as meet the requirements, should be used as a qualified product; if not, should be reduced or not used.
5、The ingredients refractory castables should be manufactured according to the planning ratio, the measurement of aggregate promised error of 3%, coagulant, water and a variety of binder and powder measurement of the promised error of 2%.
Strictly control the water-cement ratio of the refractory castables, the moisture content of the aggregate should be measured, and thus adjust the water consumption of the refractory castables.
6、Mechanical mixing and refractory castables are usually mixed mechanically and according to the following procedures:
① Before feeding, start the mixer idling for 2 minutes, after normal operation, you can feed; ② feeding order: first into the powder, binder, then into the aggregate dry mix; ① before feeding, start the mixer idling for 2 minutes, after normal operation, you can feed.
② feeding order: first into the powder, binder, then into the aggregate dry mix; ③ feeding immediately after opening the valve to add water, the amount of water for the control of two-thirds of the water.
③ open the valve to add water immediately after feeding, the amount of water for the control of two-thirds of the amount of water, and then follow the mixing and adding the other one-third of the water; ④ mixing should be continuous, the mixing should be continuous, the mixing should be continuous, the mixing should be continuous.
④ Mixing should be continuous, halfway without stopping, when mixing to the rules of the moment (not less than 5min), can be discharged, discharging process should not stop; ⑤ Mixing is completed, the water should be used for the dry mixing, and then the water should be added to the other third of the water.
⑤ After mixing, flush the inside of the mixer with water.
7、 Artificial mixing when the amount of refractory castable material is small or unconditional selection of mechanical mixing, can choose artificial mixing, mixing address should be selected in the solid and flat to facilitate the scouring of the location, and should be carried out in accordance with the following procedures:
① Dry mix of dry materials spread out, in the center of the pit and put the appropriate amount of water, penetration immersion time of not less than 3 minutes;
②when the water is simply taken out of the dry material, the dry material is not less than 3 minutes.
③ when the water is simply absorbed by the dry material, you can use the shovel from the neighborhood gradually to the middle of the mix, there shall be no dry material, and then the Department of turning the shovel, and shall not be less than three times, until the refractory castable material mixed and uniform.
8、Water-cement ratio control mixing refractory castables should be strictly controlled water-cement ratio, elected to use mechanical vibration, the slump of the refractory castables should be no more than 3-4cm; with artificial pounding, it should be no more than 5-6cm; special parts, such as dense pipe through the wall can be adjusted appropriately water-cement ratio.
9、Pouring time limit mixing good refractory castables, should be poured within 30min, or according to the requirements of the construction of the articulation in the rules of the time pouring.
Refractory castables construction details
1、 Refractory castables construction details:
Before the construction of castable material, the construction site should be cleaned up first, out of the surface of the rust impurities, to avoid the phenomenon of too many impurities easy to fall off and crack after the casting of refractory castable material.
2、Refractory castables construction details:
Refractory castables in the casting mixing, add water can not be too much or too little, must be based on the implementation of the decision, if too much water will lead to the separation of the aggregate and base material, affecting the performance of the castables, but also to reduce the density of the castables, strength, alkali resistance and abrasion resistance and so on. If the amount of water is not enough, it will lead to poor construction performance, the material can not flow normally and achieve dense filling, the air bubbles can not be discharged, and can not form a tight pile, which will also directly affect the use of performance of the castables.
3、Refractory castable construction details:
Part of the castables in the use of the time, need to use forced mixer mixing mixer, strictly prohibit manual mixing, and the use of the anchor nails must be added expansion cap or brush asphalt paint and so on. Therefore, in the construction, should carefully check the instructions on the instructions to strictly use the refractory castables.
4、Refractory castable construction details
Refractory castables maintenance problems, under normal circumstances, refractory castables are required to 24h of time to maintain, which can be conducive to enhance the use of refractory castables, and after the solidification of refractory castables, to avoid the second direct addition of water, or so made out of the castables can not be used. So the maintenance after solidification is also very important.
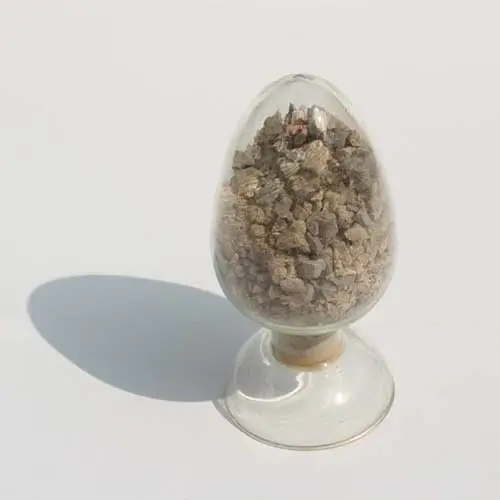
Refractory castables construction precautions
The construction of refractory castables consists of three components, namely mixing, pouring and maintenance.
1、Mixing: must use forced mixer or mortar mixer mixing, not with artificial mixing.
① Equipment and tools: forced or mortar mixer, bucket, scale, vibrating rod, tool spade, wheelbarrow and so on.
② Mixing: first to the mixer to add a large bag of material, and then add a small bag of material, dry mixing 1-2 minutes before discharging the material for pouring.
③ Judgment method of water content: In order to judge whether the water content of the mixing material is suitable or not, you can use a kind of simple “hand-knead into a ball” method of testing: if the ball is deformed and flows out from the hand slit, then it means that the water content is too much: if the ball is cracked and scattered, then it means that the water content is too small.
④ Water consumption for mixing: take the water consumption given in the instruction manual of the batch of products as the standard, strictly control the water consumption and measure it accurately.
Cautions:
①Tools used in the construction process, such as mixer, bucket, tool spade, etc., should be cleaned up in advance, and should not be mixed with other sundries such as lime, gravel, and silicate cement.
② Mixing water must be clean tap water. In the case of vibration slurry, as little water as possible, has achieved better construction results.
③ The quantity of each mixing is not too much, it should be according to the type and model of the mixer, otherwise it will cause the mixer to stagnate and stop. The solidified lumps remaining after pouring should not be mixed again with water.
④ The temperature of the construction site must be between 5-30℃, if the temperature of the construction site is lower than 5℃, corresponding warming protection measures must be taken before the construction: if the temperature of the site is higher than 30℃, corresponding cooling protection measures must be adopted before the construction: Otherwise, it will result in the difficulty of the construction of the product or the decline in performance.
2、Pouring construction:
①Check: Before the construction of the casting material, the anchors must be checked to see if they are welded firmly, and heat-resistant grasping nails should be used for the parts above 500℃. The surface of anchors should be coated with 0.5-1mm thick paint or wrapped with plastic tape to cushion the expansion force after being heated, and the debris should be removed from the mold.
② Pouring time control: the newly mixed casting material should be poured quickly, generally should be poured within 20 minutes.
③ Pouring: Pour the mixed material into the mold and insert the vibrating rod in time, the vibration should be uniform, and move the vibrating rod when the slurry on the surface of the material is in the flowing state, and the moving speed should be 1-2 meters/minute. Move the vibrating rod at a speed of 1-2 meters/minute. When pulling out the vibrating rod, the speed should be slow.
④ After pouring, the site temperature requirement control: after pouring is completed before condensation, the site temperature must be maintained above 5℃ (5-30℃), the site temperature is lower than 5℃, corresponding warming protection measures must be taken, otherwise it will cause retardation of coagulation, resulting in a decline in the performance of the product.
Cautions:
① The surface of the castables after vibration should be kept natural, and it is not suitable to be wiped out with tools, not to mention that it is not allowed to be wiped out by sprinkling cement fine powder on the surface.
② vibrating rod to have a spare, so that when the vibrating rod fails, the spare rod can be activated in time.
③After the construction is completed, the construction body within 24 hours, not to mention the casting material in the hardening before, it is strictly prohibited to move, vibration or pounding, otherwise, the casting body will produce cracks or even finished destruction.
④ The castables should be constructed continuously, when it can not be constructed continuously due to various reasons, construction joints can be left, and stay at the expansion joints, otherwise, the construction joints will be made into hemp surface, i.e., cross grooves on the castables with a depth of 10mm and a width of 20mm or so, and a spacing of 100mm or so.
Conservation:
① Tools: polyethylene plastic film, straw bags, etc..
② Environmental temperature requirements and control: the maintenance temperature of the casting body between 15-35 ℃ is appropriate, beyond this temperature range, should take the appropriate measures to warm up or cool down, otherwise it will cause a decline in the performance of the product.
③ Conservation: after the hardening of the casting material, it is necessary to cover the surface of the construction body with polyethylene plastic film immediately, and then cover the wet straw bag on top to prevent the evaporation of water and promote the activation of cement. After hardening, it is forbidden to knock and vibrate within days, according to the hardening condition, it can be demolded after 24-30 hours of hardening. After demolding, according to the need for maintenance for 2 days, maintenance continue to cover the polyethylene plastic film and wet straw bags. After 3 days of oxidization, remove the polyethylene plastic film and wet straw bags. Let the casting body dry naturally in the air for 1 day, and then bake.