High alumina brick is a commonly used refractory material, the main component of which is alumina (Al₂O₃). Its alumina content is usually above 48%. According to the different alumina content, it can be divided into multiple grades, such as special grade, first grade, second grade, third grade, etc.
High alumina brick has many excellent properties. The refractoriness is usually between 1750-1790℃, and the load softening temperature is generally between 1420-1550℃. It has strong slag resistance and can resist the erosion of acidic slag and alkaline slag, but its resistance to alkaline slag is relatively weaker than that to acidic slag. High alumina brick has high compressive strength, which is generally between 50-80Mpa according to the different alumina content. It contains a large amount of mullite inside, which has high stability and can maintain the stability of the wall under high temperature environment. In addition, high alumina brick also has good wear resistance.
In terms of production, its production process is relatively complicated. For example, the selection of raw materials usually includes ultra-high alumina clinker, pyrophyllite fine powder, bonding clay, etc. During the molding process, some raw materials need to be crushed, screened, Raymond milled, etc.
High alumina bricks are widely used, mainly used for building blast furnaces, hot blast furnaces, electric furnace roofs, blast furnaces, reverberatory furnaces, rotary kiln linings, etc. In addition, they are also widely used as open-hearth heat storage checker bricks, plugs for pouring systems, nozzle bricks, etc. Different grades of high alumina bricks are suitable for kilns with different temperatures and working conditions. In actual applications, high alumina bricks of appropriate grades and specifications will be selected according to specific needs.
1.Composition of high alumina bricks
The components of high alumina bricks mainly include alumina (Al₂O₃) and silicate materials. The content of alumina is usually above 48%, and the specific content varies according to different grades of high alumina bricks. In addition to alumina, it may also contain a certain proportion of impurities such as silicon dioxide (SiO₂), iron oxide (Fe₂O₃), calcium oxide (CaO), etc. The raw materials of high alumina bricks come from various sources, such as bauxite, sillimanite group minerals, etc. These raw materials undergo a series of treatments and processing, such as crushing, grinding, mixing, etc., and finally form the components of high alumina bricks. In the production process, strict control of the purity and impurity content of the raw materials is crucial to ensure the quality and performance of high alumina bricks. For example, mineral components such as gibbsite and gibbsite in bauxite will have an important impact on the performance of high alumina bricks after calcination and other treatments.
2.Grade classification of high alumina bricks
High alumina bricks are usually classified into several grades according to their alumina (Al₂O₃) content. Extra high alumina bricks usually have an alumina content greater than 80%; first grade high alumina bricks have an alumina content between 75% and 80%; second grade high alumina bricks have an alumina content between 60% and 75%; and third grade high alumina bricks have an alumina content between 48% and 60%. Different grades of high alumina bricks differ in performance and use. For example, special grade high alumina bricks have higher refractoriness, load softening temperature and erosion resistance, and are suitable for higher temperatures and harsher working environments, while tertiary grade high alumina bricks are relatively weaker in terms of performance, and are suitable for occasions with lower temperatures and relatively relaxed working conditions. The classification of the grade helps to select the appropriate high alumina bricks according to the specific needs of use, in order to achieve the best results and economic benefits.
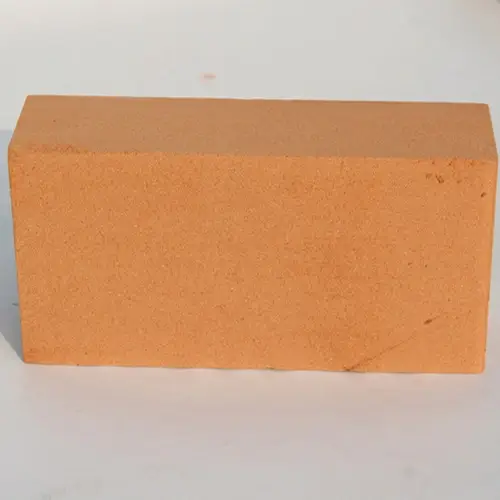
3.Chemical and physical indicators of high alumina bricks
The chemical and physical indexes of high alumina bricks are important standards for measuring their quality and performance. The chemical indexes mainly contain the content of alumina (Al₂O₃), silicon dioxide (SiO₂), iron trioxide (Fe₂O₃) and other components. The higher the alumina content, the better the refractory performance. Physical indicators include bulk density, compressive strength at room temperature, load softening temperature, refractoriness, apparent porosity, line change rate, slag resistance, etc. The bulk density is generally between 2.3 and 2.5 meters. Bulk density is generally between 2.3-2.65g/cm³, the higher the density, the denser the structure. Normal temperature compressive strength reflects the ability of bricks to withstand pressure, the compressive strength of first-grade high alumina bricks is usually around 60Mpa, second-grade around 55MPa, and third-grade around 50MPa. The load softening temperature reflects the deformation of the brick body under high temperature and pressure, which is generally above 1420-1550℃. The fire resistance is usually in the range of 1750-1790℃. The apparent porosity is low, less than 23%. The rate of linear change reflects the dimensional stability of the brick body after exposure to heat. Slag resistance indicates its ability to resist acidic and basic slag attack.
4.Characteristics of high alumina bricks
The chemical and physical indexes of high alumina bricks are important standards for measuring their quality and performance. The chemical indexes mainly contain the content of alumina (Al₂O₃), silicon dioxide (SiO₂), iron trioxide (Fe₂O₃) and other components. The higher the alumina content, the better the refractory performance. Physical indicators include bulk density, compressive strength at room temperature, load softening temperature, refractoriness, apparent porosity, line change rate, slag resistance, etc. The bulk density is generally between 2.3 and 2.5 meters. Bulk density is generally between 2.3-2.65g/cm³, the higher the density, the denser the structure. Normal temperature compressive strength reflects the ability of bricks to withstand pressure, the compressive strength of first-grade high alumina bricks is usually around 60Mpa, second-grade around 55MPa, and third-grade around 50MPa. The load softening temperature reflects the deformation of the brick body under high temperature and pressure, which is generally above 1420-1550℃. The fire resistance is usually in the range of 1750-1790℃. The apparent porosity is low, less than 23%. The rate of linear change reflects the dimensional stability of the brick body after exposure to heat. Slag resistance indicates its ability to resist acidic and basic slag attack.
5.Production process of high alumina bricks
The production process of high alumina bricks is relatively complex, including raw material preparation, batching, molding, drying and sintering and so on. First of all, the raw materials are strictly screened and graded to ensure the quality and purity of raw materials. Then according to a certain proportion of ingredients, the raw materials will be mixed evenly. The molding process usually uses a press to press the mixed raw materials into shape. After molding, the bricks need to be dried to eliminate moisture. After drying, the bricks enter the high-temperature kiln for sintering, and the sintering temperature is determined according to the grade of high alumina bricks and the characteristics of raw materials. In the production process, it is necessary to strictly control the process parameters of each link, such as pressure, temperature, time, etc., to ensure the quality and performance of high alumina bricks. For example, when batching, the proportion of various raw materials should be precisely controlled according to the characteristics of the raw materials and product requirements; in the sintering process, the heating speed and holding time should be reasonably controlled to avoid problems such as under-firing or over-firing.
6.High alumina brick usage
High alumina bricks are widely used, commonly used in metallurgy, building materials, chemical industry, electric power and other industries of high temperature industrial furnace. In the metallurgical industry, such as blast furnace, hot blast furnace, electric furnace roof and other parts, high alumina brick can withstand high temperature and slag erosion. In the building materials industry, cement kilns, rotary kilns and other equipment lining is also often used high alumina bricks. In the chemical industry, the reactor, cracking furnace and other high-temperature equipment in the high alumina brick plays an important role. High-alumina bricks are also used for boiler linings in the power industry. In addition, high alumina bricks are also widely used as heat storage type lattice bricks for flat furnaces, plugs for pouring systems, water spout bricks and so on. For example, in the ironmaking blast furnace, high alumina brick as a lining material, can effectively resist the high temperature and the erosion of iron, slag, to extend the service life of the blast furnace; in the cement rotary kiln, high alumina bricks can withstand high temperatures and material wear and tear, to ensure the normal operation of the kiln.
With its excellent performance and wide applicability, high alumina brick occupies a pivotal position in the field of high temperature industry. With the continuous progress of science and technology and the continuous development of industry, high alumina brick production process will continue to optimize, the performance will be further enhanced for the various industries of high temperature equipment to provide more reliable refractory protection. I believe that in the future, high alumina bricks will continue to play an irreplaceable and important role in promoting industrial development and ensuring production safety.