The reasons for steel leakage between ladle slide plates are manifold, and poor control of sliding spout machinery, slide plate installation operation, slide plate quality, ladle steel pouring operation, steel smelting and other aspects may lead to steel leakage between slide plates. For different reasons to develop appropriate preventive measures, can reduce the chances of steel leakage slide plate.
1.Strict control of the end point [Ca] content of the molten steel
As can be seen from the phase diagram of the CaO-Al2O3 system, when the Ca, Al mass ratio in the steel > 0.10, Al2O3-like inclusions basically react with CaO to 12CaO-7Al2O3 or low-melting compositions close to 12CaO-7Al2O3, which are easy to be discharged from the steel. Therefore, in actual production, the control of calcium line feeding is mainly based on the requirements of the steel Ca, Al quality ratio to control, but the following reasons may lead to fluctuations in [Ca] content: a) feeding calcium line process ladle blowing argon is too large; b) fluctuations in the amount of steel, did not adjust the amount of feeding line in a timely manner; c) feeding calcium line sampling too soon after the steel is not evenly mixed, [Ca] content is not representative of the; d) Add steel core aluminium for deoxidation, blowing argon is too small, steel mixing is not uniform or sampling too early, resulting in unrepresentative samples; e) Calcium wire itself fluctuations in material.
Therefore, in order to prevent [Ca] excess, before feeding calcium line must be temperature sampling, according to the amount of steel, steel temperature, the content of [Als] in the steel, calcium line of the rate of collection and steel required by the Ca, Al quality ratio to control the calcium line feeding volume (tonnes of steel 3 ~ 4m), the bottom of the argon blowing volume (50L-min-1) and feeding calcium line temperature (1590 ~ 1605 ℃), to ensure that the end point of the steel [Ca] content within the control range. Ca] content is within the control range. (Note: Reference data for steel grade A are shown in parentheses).
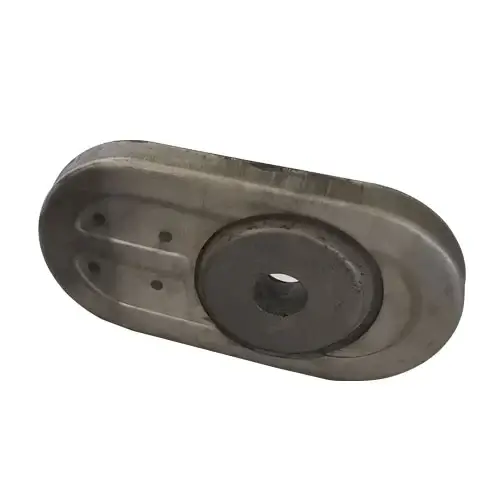
2.Enhanced maintenance of the ladle slide gate mechanism
Check whether the mechanism of the mould frame deformation; spring loaded to the surface pressure of the slide plate is appropriate; timely replacement of wear parts; need to lubricate the part of the frequent refuelling.
3.Determine whether the slide plate can continue to be used continuously according to the requirements of the steel grade to be made
Observe the surface of the slide gate plate for deep hair pulling, cracks and abnormal fusion damage, etc.; judge whether the effective residual travel of the slide gate plate meets the requirements for re-use.
4.Installation of slide gate in strict accordance with the operating points
Clean the debris on the working surface and back of the mould frame and ladle slide plate; keep the ladle slide plate in full open state when burning oxygen.
5.Careful handling during pouring
In the process of steel pouring, try to reduce the number of pulling times of the ladle slide plate to reduce the possibility of wear and tear; for the tundish of multi-stream steel pouring, if there is more than 1/2 of the casting stream can not be poured, the continuous casting machine should stop pouring; should be satisfied with the normal control of the flow of the ladle slide plate to minimise the distance between the ladle slide plate’s pulling, in order to protect the ladle slide plate’s effective residual stroke; in the end of the pouring period to prevent slag under the mouth of the water, in order to prevent unnecessary erosion of the slide gate plate.
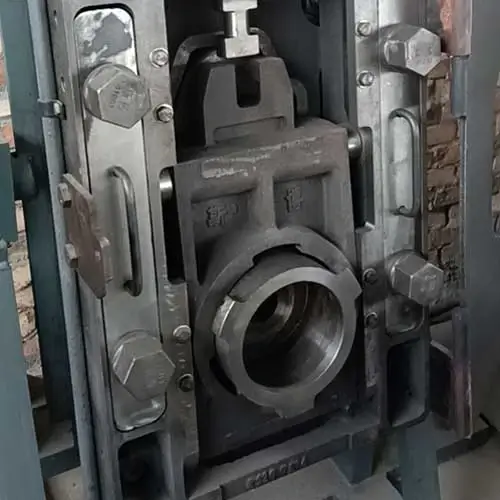
More details about ladle slide gate plate
1.What is slide gate refractory?
Slide gate system is one of the crucial components of steel making process. It is this slide gate that controls the flow of molten steel. It is seen that the performance of this slide gate is heavily dependent upon the refractories used in conjunction with it.
2.What is the composition of slide gate plate?
Aluminum-zirconium carbon slide gate plate
The slide plate of this material uses low expansion rate of Al2O3-SiO2-ZrO2 raw materials, made into a refractory material characterized by carbon bonding with oblique zircon, mullite, corundum, etc.
3.What is slide gate mechanism?
An automatic sliding gate is an efficient way to automate a gate for a commercial or residential building. It is a combination of two wheel assemblies and rear guide wheels that travels smoothly through a sloped opening. The mechanism can be programmed to open and close the gate at the push of a button.