Refractory furnace lining, an important component of crucible-type induction furnaces, affects the melting function of the furnace, the metallurgical quality of the steel, and, especially critical, the safety of the operation. As crucible type induction furnace is suitable for melting various casting alloys, such as cast iron, cast steel, copper alloy, aluminum alloy and zinc alloy, etc., small induction furnace, furnace lining can be purchased molded prefabricated crucible. The actual production of crucible-type induction furnace for steel casting, generally by the foundry according to the variety of alloy melting refractory materials, self-construction of the furnace lining, and do a good job of sintering operations.
1.The basic situation of refractory materials for furnace lining
Several refractory materials commonly used in crucible induction furnaces, including electrofused magnesium sand, metallurgical magnesium sand, alumina materials, and silica sand.
2.Lining refractories for steel furnaces
With the development of induction furnace application in the steel casting industry, since the 1980s, the application of aluminum-magnesium spinel-type furnace lining materials have gradually been attached importance to, at present, the crucible-type induction furnace used in the steel casting industry in various industrial countries, basically using spinel-type furnace lining.
In recent years, China also has some steel casting enterprises used spinel-type furnace lining materials, of which, some manufacturers are to buy foreign manufacturers pre-prepared materials, although the use of the effect is very good, but the cost of production to improve a lot, and its characteristics are not well understood. Here, I mainly want to introduce some of the characteristics of spinel-type refractory furnace lining for industry colleagues to formulate their own furnace lining materials, further improve the furnace lining materials for reference. At the same time, in view of the current silica sand lining, magnesium sand lining, alumina lining in China’s steel casting industry are still applied, but also by the way, the characteristics of these materials to make a brief introduction for reference.
(1) Silica sand furnace lining
Silica sand as the basic refractory materials for the construction of the furnace lining, usually also known as acid furnace lining. Silica sand has many advantages: first of all, abundant resources, low price; and silica sand as the basic refractory material made of crucible, close to its melting point at high temperatures still has good strength, resistance to sudden cold, sudden heat performance is good; should be mentioned is that, in the process of furnace lining sintering, silica sand quartz phase expansion can make up for the volume contraction in the process of sintering, so as to improve the densification of the sintered layer, reduce the sintered layer of the lining of the furnace. The porosity of the sintered layer of the furnace lining is reduced. Therefore, the foundry industry in various countries, for melting various cast iron crucible induction furnace are widely used in silica sand based furnace lining materials.
However, the low refractoriness of SiO2, basically can not adapt to the steelmaking temperature. In addition, SiO2 may also be some of the more active elements in the steel reduction. Therefore, silica sand furnace lining for steelmaking can neither guarantee the metallurgical quality of steel nor the life of the furnace lining. Since the late 1980s, the industrialized countries with induction furnace production of cast steel parts foundry, has not used silica sand furnace lining. As far as I know, there are still some enterprises using silica sand furnace lining melting cast steel, this situation is urgent to improve.
(2) Magnesia furnace lining
Commonly used furnace lining material is MgO content of 86% or more of the metallurgical magnesium sand, is made of magnesite by high temperature calcination.If the metallurgical magnesium sand in the electric arc furnace remelting, SiO2, Fe2O3 and other impurities can be reduced to obtain a higher purity (MgO content of 96% or more) of electrofusion magnesium sand. Electrofused magnesium sand is mostly used to make the lining of vacuum induction furnace.
The refractoriness of metallurgical magnesia is very high, and it is the conventional lining material for alkaline electric arc steelmaking furnace. Although its melting point is very high, it is not easy to be sintered, and the expansion coefficient is large, but due to the thick lining of the electric arc furnace, it can completely make up for the shortcomings in this aspect by adding a large amount of bonding material and knotting with wet method.
If the metallurgical magnesium sand as the induction furnace lining materials, due to the constraints of the thickness of the furnace lining, and not suitable for wet knotting, the negative effects of these shortcomings is very obvious, thus. Crucibles made of magnesium oxide materials are prone to cracking, which is particularly serious in furnaces with intermittent operation.
(3) Alumina Furnace Lining
Alumina and zirconia sand are neutral refractory materials, of which the most widely used is alumina, rarely used zirconia sand as furnace lining materials.
Single alumina for furnace lining materials, anti-cracking and prevent acidic slag erosion ability is stronger, but not suitable for making alkaline slag.Moreover, due to its high refractoriness and poor sintering performance, the furnace lining life is not very high.
(4) spinel-type furnace lining
Spinel minerals have the characteristics of homogeneity, many varieties, the composition is also more complex, its molecular formula can be written as M2 + O-M3 + 2O3, where: M2 + on behalf of a number of divalent metal atoms, such as Mg, Fe, Zn, Mn, etc.; M3 + on behalf of a number of trivalent metal atoms, such as Mg, Fe, Zn, etc.. Thus, it can also be written as (Mg,Fe,Zn,Mn)O-(Al,Cr,Fe)2O3 .
Spinel minerals contain divalent metal atoms, Mg2 + and Fe2 + can replace each other in any proportion; contained in the trivalent metal atoms, to Al3 + mostly, but Cr3 + can be replaced by any proportion of Al3 +, Fe3 + can only be replaced in a certain limit Al3 + or Cr3 +. Common spinels are of the following types:
Magnesia-aluminum spinel MgO-Al2O3
Iron aluminum spinel FeO-Al2O3
Chromite (ferrochromium spinel) FeO-Cr2O3
Magnetite (Fe Spinel) FeO-Fe2O3
Magnesia-iron spinel (Mg,Fe)O-(Al,Fe)2O3
Zinc-aluminum spinel ZnO-Al2O3
Magnesium-chromium spinel MgO-Cr2O3
Zinc-iron spinel ZnO-Fe2O3
Mn-Cr spinel FeO-Cr2O3
Manganese Aluminum Spinel MnO-Al2O3
At present, in various industrial countries, used as steelmaking induction furnace lining materials, mainly magnesium aluminum spinel (MgO-Al2O3), usually referred to as ‘spinel’. Pure magnesium-aluminum spinel, MgO content is only 28.2%, but still belongs to the alkaline refractory materials.
Magnesia-aluminum spinel materials have high refractoriness, small coefficient of thermal expansion, good thermal stability at high temperatures, and strong resistance to alkaline slag erosion. Especially should be mentioned: MgO and Al2O3 in the sintering process to form spinel has 7.9% volume expansion, can make up for the volume contraction in the sintering process, reduce the porosity of the sintered layer, which is the same with the important advantages of silica sand furnace lining.
Magnesium-aluminum spinel basically no natural minerals, are synthesized by artificial, prepared by electrofusion and sintering two ways. China’s metallurgical industry in 1997, that is, with reference to the specifications of the Alcoa Chemical Company MR66 and AR76 materials, the development of YB/T 131-1997 “sintered magnesium-aluminum spinel” industry standard.
Spinel-type furnace lining materials, in fact, not all composed of spinel, but to granular Al2O3 or granular MgO materials as the basis, in which with the corresponding powder, or fine grain spinel formation materials, so that it is uniformly distributed in the particles of refractory materials between the formation of magnesium-aluminum spinel network between the alumina particles during the sintering process, the role of the combination. In addition, it is also necessary to add a small amount of boric acid or boronic anhydride, so that it can be at a lower temperature (1300 ℃ or so) that the formation of spinel network.
United Minerals Corporation, France, Minac Mining Company, Calderys and other well-known refractory supply manufacturers, there are a variety of pre-prepared spinel furnace lining material supply, according to the enterprise’s furnace and melting steel type selection, but the price is relatively high.
I thought the best solution is: the cast steel enterprises, according to their own specific conditions, through the test optimization, selected the most appropriate ratio, the preparation of their own furnace lining materials. In this way, not only can ensure that the furnace lining life long, high metallurgical quality of steel, but also can significantly reduce production costs.
As for the composition of the furnace lining material ratio, should be selected according to the actual composition of the various raw materials used, and determined by the test. Determine the ratio of furnace lining materials, can be calculated according to the following target composition:
Aluminum oxide as the basis of granular materials to maintain the furnace lining material in the mass fraction of Al2O3 for about 85 ~ 88%, the mass fraction of MgO for about 22%;
When magnesium oxide is used as the basic granular material, the mass fraction of MgO in the lining material is 75-85%, and the mass fraction of Al2O3 is 15-22%.
3.Granularity gradation of furnace lining materials
The degree of densification of the crucible has an extremely important influence on its service life. In order to make the crucible densified and to keep the porosity as low as possible, attention must be paid to the particle size gradation of the refractory material, so that the voids in the large-particle refractory material can be filled by fine-grained material.
In order to let you have a more specific impression of the void rate after the granular material is knotted, here, the case of ideal sphere stacking is made as a simple explanation.
(1) The case of average tightness
The case of spheres of the same size, stacked in a square staggered arrangement is shown in the figure. Each ball is in contact with 6 neighboring balls (4 balls around and 1 ball above and below) with a porosity of 47.64%. From the figure, it is easy to find the maximum diameter of a small ball that can fit in the gap of a large ball of diameter D.
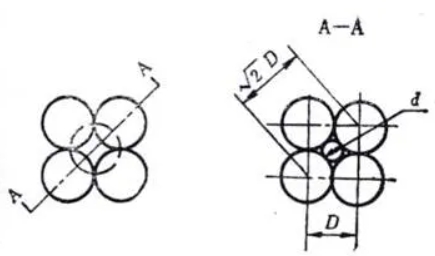
(2) The more compact case
When the balls are stacked in a diagonal arrangement, each ball is in contact with 8 neighboring balls (6 balls around and 1 ball above and below) with a porosity clearance of 39.55%.
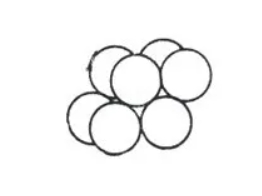
(3) The case with the highest degree of compactness
The stacks with the highest degree of compactness are the orthogonal staggered arrangement and the tetrahedral-like arrangement. When uniform spheres are stacked in a square staggered arrangement, each ball is in contact with the neighboring 12 balls, 4 balls around it, and 4 balls above and below it, and the porosity is 25.95%. The case of uniform spheres stacked in a tetrahedral-like arrangement is shown in Fig. 3. each ball is in contact with the neighboring 12 balls, surrounded by 6 balls, 3 balls each on the top and bottom, and the porosity is 25.95%. from the figure, the maximum diameter d of small balls that can be accommodated in the pores of a uniform sphere with a diameter D can be calculated.
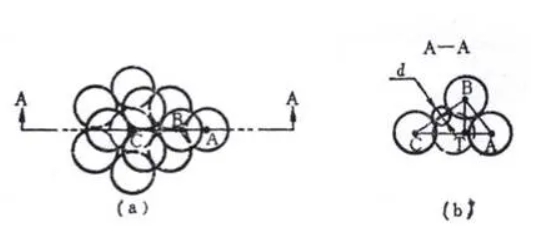
As seen from the case of several stacks of spheres, the porosity is determined only by the arrangement and is independent of the size of the sphere diameter. Ball diameter is large, the size of the pore is large but the number is small. The production of furnace lining particles of refractory materials are polygonal, or even sharp-edged, its mobility is very poor, no matter what kind of knotting method, pounded the tightest, its porosity will not be less than 30%. In order to reduce the porosity of the furnace lining, simple and easy measures is to make the lining material in the particle size is not so uniform, and fine-grained material can enter the tightly arranged between the coarse particles, the minimum requirement is of course, there must be d <0.414D fine particles. This is where the requirement for particle size gradation comes in.
Of course, the refractory particle condition is much more complex than the ideal sphere, particle size distribution is also very irregular, it is impossible to simply rely on calculations to find the best particle size grading program. The best way is: each foundry on their own raw materials, the actual situation, through the test, to find the most appropriate grading program.
Test method is very simple: the material will be different particle size according to a certain ratio of mixing, under a certain pressure to make it compact molding, and then determine its bulk density. Raw material supply conditions change, but also by the test to assess the particle size grading program.
Since the purpose of particle size grading is to densify the pile of particles, independent of the nature of the material, this principle can be applied to all kinds of refractory materials. Germany also recommends different particle size gradings for materials with different crucible capacities.
Sintering of furnace lining materials
Crucible-type furnace linings are made of granular refractory materials that are knotted, pounded and then sintered. “Sintering” is an important measure to ensure that the furnace lining is dense and has considerable strength. “Sintering” is the process of making liquid phase appear on the contact surface of particles in the granular/powder aggregate at high temperature, gradually forming a continuous network, which connects the particles into a whole and minimizes the porosity by diffusion, mass transfer and other mechanisms, and finally becomes a solid and dense sintered body.
“Sintering” is a relatively old process and has been studied in greater depth in recent decades. However, the current understanding is still only established by the macroscopic observation of the sintering process and the assessment of simplified models. With the continuous expansion of the application of induction furnace, in this regard, the research and improvement of the space is very broad.
As a result of a number of constraints, crucible induction furnace lining thickness is thin is an important feature, however, by knotting, sintering after the furnace lining can not be sintered into a whole, because, the whole sintered lining, if a weak link exists somewhere due to uncontrollable factors, and in the repeated thermal stresses under the action of cracks, cracks are easy to extend to the whole, so that the liquid metal penetrates into the induction coil, resulting in major accidents. resulting in a major accident.
Furnace lining sintered, the section should be a 3-layer structure: the formation of the furnace, and the liquid steel contact layer is a sintered layer, the thickness of about 35 ~ 40% of the thickness of the furnace lining, which is characterized by a dense sintered network, low porosity, high strength; with the sintered layer connected to the sintered layer is a semi-sintered layer, the thickness of the same as the sintered layer is generally characterized by the sintered network is incomplete, the strength of the high strength, and thus can buffer the sintered layer of thermal stresses, if cracks occur. If the sintered layer produces cracks, can stop the cracks to the outside; furnace lining of the outer edge, in the induction coil and half-sintered layer between the unsintered layer, refractory still maintains the knotted particles state. This layer, the role of thermal insulation, and can slow down the sintered layer to the coil heat conduction, its thickness accounts for about 25-30% of the thickness of the furnace lining.
The sintering process of spinel-type furnace lining can be roughly divided into three stages:
The first stage: heating temperature below 850 ℃, the main role is to make the furnace lining material more thoroughly dehydrated;
The second stage: heating to 850 ~ 1400 ℃, the main role is to form a spinel network;
The third stage: heating to 1300 ~ 1700 ℃, spinel network growth, driven by surface tension to enhance the function of diffusion, mass transfer, porosity is significantly reduced, the sintered layer tends to be close.