Ferroalloy electric furnace furnaces, especially cold stamped paste villages, when the knotting quality does not meet the required requirements, and the oven lining time and heating rate are not closely controlled during baking, the baking quality of the furnace village will not be achieved. To normal production requirements. According to the reasons for the damage of the furnace lining of the ferroalloy electric furnace to extend the furnace village, the main measures to extend the life are as follows:
1.Selected furnace lining carbonaceous raw materials
For refractory charcoal blocks, the ash content is generally not higher than 6%, the volatile content is not higher than 0.6%, the high pressure strength is not lower than 260kg / cm3, and the 1.2m-long standing carbon block is required to fall to the ground without damage cracks.
Cold stamping requires that the ash content is not higher than 8%, the volatile content is controlled from 9.5% to 10.5%, and the bulk density after knotting is not less than 1.9g / cm3.
2.Matters needing special attention when building a furnace
For the carbon block furnace bottom furnace village, a large amount of tar and asphalt are volatilized when the furnace is built, and the operating environment is poor. Therefore, the number of fans at the furnace mouth should be increased before the furnace is built. Supply air in the furnace, quickly replenish the oxygen content in the furnace, and improve the operating environment in the furnace. After each layer of carbon block is built, because there will be a certain amount of moisture in the burnt powder, it is best to pre-bake with wood fire. Maintain the temperature of 90 ~ 110 ℃ for 4-8h. After the last layer of carbon block is laid, cover the brick gap with a layer of 3-5cm thick hot stamping paste. When used as an oven, the hot stamping paste will melt. Supplement when immersed downwards. When cold stamping is used for the hearth lining, the knotting quality is mainly required. Therefore, the supervision of knotting quality on site is very important. It is best to sample each part, especially the central part, for each knotting layer. Bulk density analysis. For those that fail to reach the standard after being further knotted, the old knotted material should be dug out and re-knotted until it meets the requirements of the standard. In addition, for the cold stamping furnace lining, the cumulative height of knotting should not exceed 0.8m, and it is best to lay a layer of 400 ~ 600mm thick dense carbon blocks under the knotting material to prevent the upper layer The molten iron penetrates further down after the local damage in the cold mash, which can significantly extend the life of the furnace village. In addition, whether it is built with carbon blocks or cold-paste, in addition to leaving a wide enough expansion joint in the furnace wall, a 30-50mm thick expansion joint must also be considered at the bottom of the furnace to prevent expansion damage when the overall temperature of the furnace lining rises.
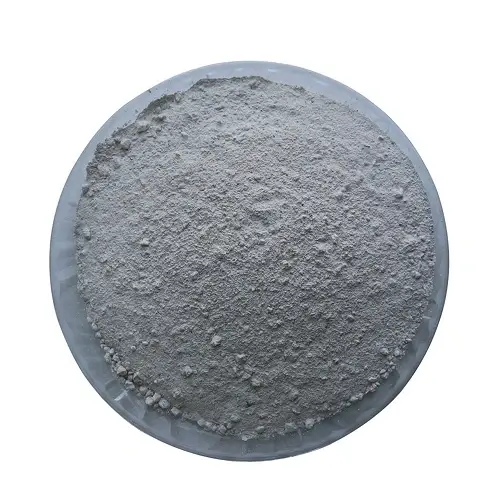
3.Oven operation
For charcoal-lined linings, there are not too many requirements for opening furnaces. You only need to adapt to the load of a few days before the furnace is opened. Do not use the full load, but if you use cold stamping for lining, The requirements for opening the oven are relatively high. A more detailed oven plan and temperature rise curve should be developed before the oven. In general, the temperature in the furnace should be controlled by wood fire and a small amount of coke within the first to second days. Within -250 ℃, the cold stamping paste is mainly in a softened state, and an electric oven is used after 1-2 days.
The load is gradually increased during the electric oven, so that the temperature rise rate is maintained at 10-15 ° C / h in the initial stage of the oven. After the temperature in the furnace rises above 400 ° C, the temperature rise rate can be appropriately increased to 20-30 ° C / h. After the temperature in the furnace rises above 700-800 ° C, stop lifting the load and keep it for one day. After one day, you can continue to increase the load until 90% of the full load is stopped and maintain the load for about a week.
The load can be increased to full load or more after one week. In the oven, special attention should be paid to not staying too long in the low temperature section of the oven at the initial stage to prevent the volatilization of the volatiles from premature and excessive volatilization, which causes the overall strength of the furnace lining to be significantly reduced.
4. Control of electrode operation
On the one hand, it is necessary to control the depth of electrode insertion to be appropriate and a sufficient distance from the furnace bottom to avoid damage to the furnace bottom lining by the high temperature of the arc of the electrode. In addition, it is necessary to avoid the electrode pressing on the furnace bottom within 1h before tapping.
5. Other measures
For cold stamping furnace lining, when there is a long period of thermal shutdown (more than 15 days), if protective measures are not adopted, a large shrinkage crack will occur after the furnace bottom is cooled, and the power will be retransmitted to full load. After that, there will be iron leakage at the bottom of the furnace, and serious furnace wear-out accidents may occur. For this kind of thermal shutdown, in addition to regularly spraying insulation coke in the furnace, try to send a certain load before the furnace is stopped. , So that the bottom of the furnace has a normal load of molten iron generated for at least two hours to avoid the furnace bottom temperature falling too quickly. In addition, after a long thermal shutdown, the load at the initial stage of power restoration cannot be too fast, and the load cannot exceed 90% of the normal load within a week.
Generally, the knotted bulk density of cold stamping is not less than 1.9g / cm3. At the same time, when the electric furnace is sent to the electric oven, the time at the low temperature of 150-250 ℃ should be controlled within 1-2 days. When the temperature rise is increased to 700- After 800 ℃, the load should be controlled no longer and maintained for 24 hours. When the load is continued to rise, the load should not exceed 90% of the normal load within a week. The furnace is baked at the above speed. Usually, the furnace lining can be obtained. Effectively prolong, in addition to laying a layer of 400-600mm thick carbon blocks under the cold mash, can significantly extend the life of the electric furnace lining.
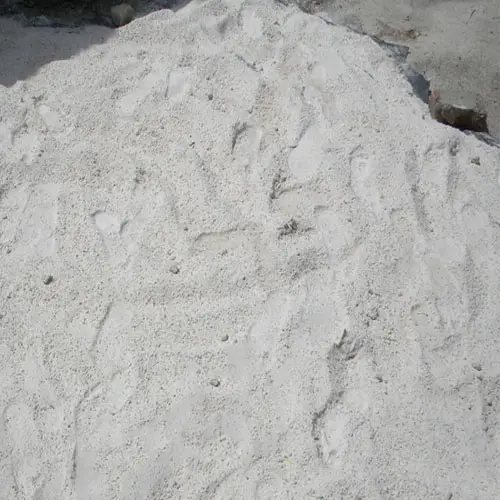