The quality of high alumina bricks to improve , no more than high-pressure molding, high-temperature sintering. However, in the production process, it is necessary to start from the source, in order to better ensure the stability of the quality of the product.
High-alumina bricks are divided into one, two or three levels
High-aluminum bricks are classified into first, second and third level, which is to determine the quality grading of bricks by chemical and physical indexes. High-aluminum bricks used in the current market, except for the first grade, are basically made with a small amount of waste bricks and raw materials. Regardless of the ratios, it is necessary to start with the raw material matrix.
In the production process, the selection of materials and ingredients is also very important, the picking of raw materials is the first link, be sure to pick out the impurities, so as to avoid the refractory bricks melt holes and black spots. Next is the high alumina brick molding, generally 90% of the high alumina brick is machine pressure molding, only a small number of special use parts of the brick is hand or hydraulic molding.
High Alumina Brick Forming Process
Machine pressure molding of high alumina bricks in the mixing to add the amount of water than the amount of water added by hand to less, in general, in the first proportion of good raw materials first dry mixing, and then add water, machine pressure molding of raw materials with water in 6-8%, hand-formed water added in 9-10%, whether it is handmade or machine pressure molding of high alumina bricks of raw materials must be stirred can not be less than 8 minutes, in principle, is dry mixing for 2 minutes, add water and then stir for 10 minutes! About.
High-alumina brick molding process, must first light and then heavy, discharge products of gas, so that high-alumina bricks can not appear layer cracks, densification is stronger. If it is a handmade brick, it must be hit with more standing hammers and pressurized on both sides. So that the air inside the raw material is fully discharged. If the gas is not fully discharged, there will be layer cracks, affecting the quality of high alumina bricks.
Fired products
Next is sintered products, in the sintering process, first from the beginning of the kiln should be fine operation, kiln loaded semi-finished billet must be loaded kiln reasonable, leaving a reasonable fire road, so that the high alumina bricks can be fully sintered, sintered, to ensure that the strength of the products. After the dryer products in the sintering process, according to the raw material matrix of high and low, to determine the sintering temperature, and to be sintered in the oxidizing atmosphere, can not make the reducing atmosphere sintering, reducing atmosphere sintering of high alumina bricks dark, red and white inconsistency.
Adjustment of the distribution of the kiln’s good fire holes during the sintering process
If the sintering of high-temperature bricks, because the particle distribution and matrix is good, high-temperature sintering, kiln speed will be longer than the second or third level of high alumina brick time. Out of the kiln time is also a sintering process must master a technology, not the same sintering time to burn out all the products, is based on the level of raw materials, set out the sintering and kiln time.
Sintering process, to adjust the distribution of the kiln good fire hole, adjust the temperature difference between the lower and upper parts of the kiln car, of course, can also be on the dense under the thinning of the installation of the kiln, but also to adjust the method of sintering.
In short, to improve the quality of high alumina bricks, it must be raw materials to start, after mixing, molding, firing a series of fine operations to ensure that the indicators of high alumina bricks.
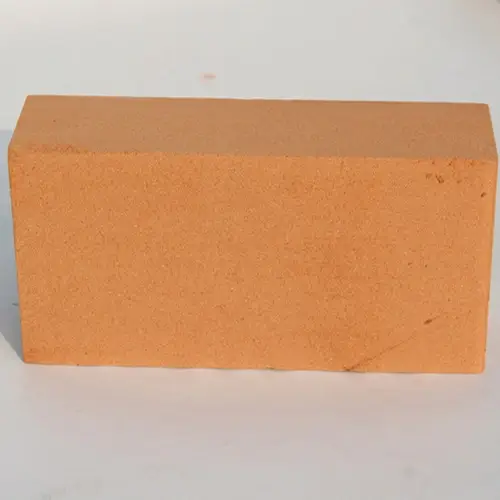