With the development of new dry cement production technology, the corresponding refractory materials have also developed greatly. In addition to the breakthrough of conventional refractory bricks, the performance of fire -resistant pouring materials is also more and more complete, and it is widely used in the irregular parts in the kiln. As we all know, refractory watering is a non -fired -type refractory material that is not burned without burning. It is prepared by refractory aggregate, refractory powder and glue agent in a certain proportion; It can be condensed and hardened by forming and maintenance (baked according to a certain temperature system). The use of refractory watering materials is as follows: First, the masonry structure has few seams, strong overallness, good sealing, and can avoid the penetration of clinker powder during application operation; second, it is easy to anchor and convenient construction, which is conducive to improving masonry masonry Efficiency and masonry quality; Third, the raw materials are widely available, which is convenient for comprehensive utilization resources, and the delivery time is short, which can reduce the amount of inventory and its related costs accordingly. Based on these advantages, the application ratio of fire -resistant pouring in the cement firing system has increased year by year. Taking a new type of dry kiln of 5000T/D as an example, the use of refractory pouring and refractory bricks has reached 1: 1.
1.Measures to speed up the use cycle
The refractory watering is popular in a kind of high -temperature concrete, so it is also in line with the theory of concrete. If the amount of water adding water is the fundamental reason for controlling the refractory pouring materials to achieve the design strength. However, due to the driver of interest, some construction parties will add water in the pouring materials to accelerate the construction progress when the construction progress is performed, which will lead to the fire -resistant lining after the construction of the kiln after construction. Even if you have used serious problems in half a year, you must repair it (and the good fire -resistant pouring materials are well used. You do n’t need to repair it for 3 to 5 years). We know that the investment in refractory materials accounted for a small proportion of the entire construction factory investment (about 2%one 4%), but it had a great impact on the future operation of the entire system. Due to the loss of a day of parking on fire -resistant lining accidents, less than hundreds of thousands of yuan or even millions of millions, to ensure the high operation rate of the firing system to achieve the high -quality, high yield and low consumption operation of the system.
2.Strict implementation of regulations
(1) The amount of water added to the watering should be controlled strictly in accordance with the instruction manual, and it must not exceed the limit, and under the premise of ensuring construction performance, add water should not be less.
(2) The mixing time of the pouring is not less than 5min. Use a mandatory mixer during operation. When stirring, you should dry up and mix it first. Then add 80%of the amount of water and stir. Get the appropriate work consistency.
(3) Pour the pouring materials in the mold frame immediately. The vibration rod should be made in layered. The height of each layer should not be greater than 300mm. The vibration spacing should be 250mm. Try to avoid touching the anchor during vibration. The layer shall not be vibrated and revived on the same part. After seeing the surface of the pouring material, the vibration rod should be pulled out slowly to avoid the phenomenon of the pouring layer and the empty hole.
(4) When pouring in a large area, it is necessary to build it in block. The area of each pouring area is about 1.5m². The expansion seam should be left according to the design. The expansion seam should be located in the middle of the interval between anchor parts.
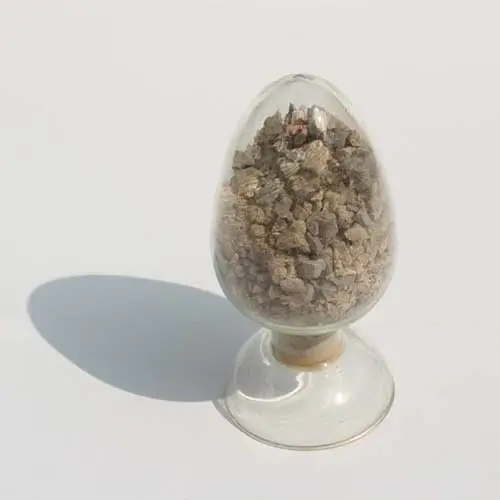
More details about refractory castable
How many types of castable are there?
Conventional castables, low cement castables, ultra-low cement castables, no-cement castables, refractory plastics, mortars, and so on. Castables can be applied by pouring, pumping, casting, gunning, shot-creeting and ramming. Self-leveling refractory castables are also available.
What is a refractory castable?
Castable Refractory—A refractory mixture with heat resistant hydraulic cement and binders that can be cast in place. Castable refractory has many applications in industry as well as studio ceramics. It is often used in kiln construction because it is easy to use and mix, and reasonably priced.
What are the raw materials for refractory castable?
There is a wide variety of raw materials that refractory castables are derived from, including chamotte, andalusite, bauxite, mullite, corundum, tabular alumina, silicon carbide, and both perlite and vermiculite can be used for insulation purposes.
What is dense castable refractory?
Dense castables are special types of cements that are suited for use in high temperature settings. The reason why these are required is because traditional cements do not work in industries where high temperature processes are involved. Alumina based refractory castables have evolved over the last few decades.