We have shared the construction methods of refractory castables in many articles in the past, including blast furnaces, circulating fluidized bed boilers, etc. Today, taking the second-stage converter in the petrochemical industry as an example, we will briefly share the construction of refractory castables for converters.
The construction of refractory castables for the second-stage converter must be carried out after a series of construction preparations such as equipment preparation, material and tool preparation, and steel formwork installation have been completed. The focus of its construction is on the mixing, pouring and maintenance of refractory castables. The details are as follows:
1.Refractory casting mixing
(1) The mixer uses a large forced mixer for mixing. The mixing procedure and water addition amount are strictly carried out in accordance with the construction instructions provided by the material manufacturer;
(2) The mixing water should be clean and potable water. The water temperature and the discharge temperature should be controlled within 10~25℃. The mixing time after adding water should not exceed 2min;
(3) In order to prevent the castable from condensing in the mixer and the string barrel, the mixer and the string barrel should be cleaned frequently.
2.Refractory castable casting
(1) Before pouring the cylinder, the spherical arch support ring can be filled with water to clean the pouring material when pouring the cylinder;
(2) When pouring, the string barrel should be moved symmetrically at 180° and the material should be cut evenly along the circumference. The string barrel should not be fixed in one place for cutting;
(3) The pouring speed should be equal, with a height of 350mm per hour being appropriate;
(4) When using a plug-in vibrator to vibrate castables, the vibration time should be strictly controlled. Stop vibrating immediately when no bubbles escape around the vibrator to avoid stratification. While vibrating, tap the template lightly with a mallet;
(5) Vibration of castables should be carried out in layers, and the thickness of each layer should be 150mm. When vibrating, the vibrator rod should cover 50mm of the lower castables to ensure a tight combination of new and old castables. Pure calcium aluminate cement Refractory castables should be poured continuously, with intervals of no more than 30 minutes;
(6) The free falling height of the castable material during pouring should be within 1.3m. If it is too high, it will cause the particles of the castable material to separate. When using a skewer, 800mm is the best;
(7) Stop pouring when the castable is 100mm away from the top of the formwork, and pour after the lower formwork is installed;
(8) The ambient temperature for castable construction should be between 5-35°C;
(9) The thickness of the lining should be controlled by the thickness control top block. The thickness deviation of castable lining is ±5mm.
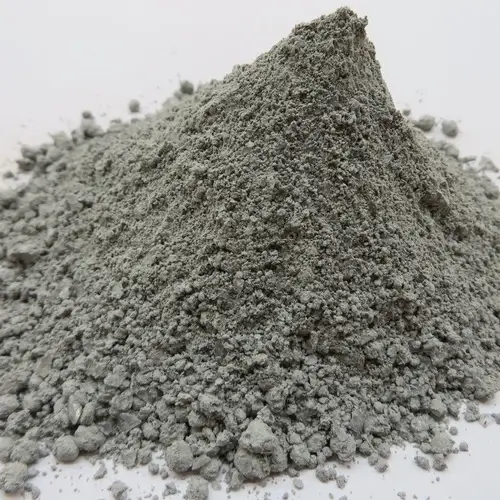
3.Maintenance
(1) After the castable is poured, it is cured according to the design requirements. Since the second-stage reforming furnace lining is continuously cast as a supporting form, the start time of curing can only be judged based on the initial setting time of the castable. Generally, it is 3 to 5 hours after construction to start pouring on the formwork. The method of water cooling and curing is to wait for no less than 24 hours until the end of heat release of the castable. During curing, seal all pipe openings to reduce air convection and avoid water evaporation.
(2) After curing for 24 hours, the mold can be removed. After natural curing, hammer inspection is carried out. A crisp sound indicates that the structure is dense and there are no cracks on the lining surface. After the oven is finished, the overall furnace lining is inspected for quality. Small network cracks are allowed, but no through cracks are allowed.
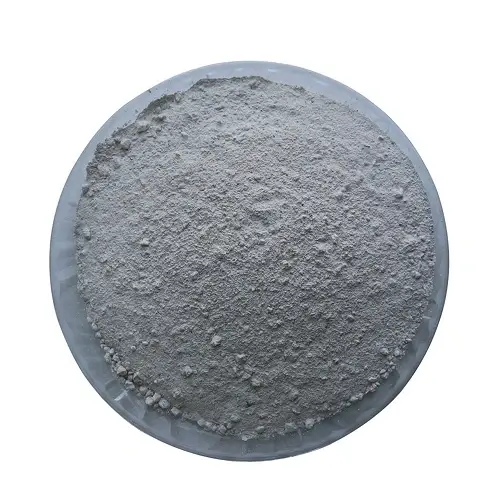