With the reform and improvement of continuous casting technology and functional refractories, the most commonly used in our country is the zirconium sizing nozzle. According to the content of zirconia in the sizing nozzle, the zirconium sizing nozzle can be divided into ordinary type sizing water and zirconia type sizing water are two categories, ordinary sizing water The content of Zr02 in zirconium inlay is less than 85%; the content of Zr02 in zirconia type sizing nozzle is more than 85 %.
Due to the different production processes, the sound-through type sizing nozzle can be divided into four types: homogeneous sizing nozzle, direct compound sizing nozzle, vibration forming sizing refractory nozzle and inlaid sizing nozzle.
⑴Fully homogeneous sizing nozzle
The fully homogeneous sizing nozzle is mainly made of zirconia and a small amount of zircon in a certain proportion, mixed, molded, dried, and sintered at 1620-1650°C. Since the content of zirconia is 60-90%, its advantages are good uniformity of composition and structure, high strength, high corrosion resistance, safe and reliable use, but the disadvantage is that the production cost is high and the life is short.
(2) Direct compound sizing nozzle
The body of the direct composite sizing nozzle is made of zircon, and the working surface of the nozzle sizing end is made of zircon and 72%-78% zirconia. The composite part of the body and the working surface is formed at the same time, in 1620-1650 ℃-time firing, the advantage of this nozzle is that it has good integrity, is not easy to fall off during use, and the production cost is much lower than that of a fully homogeneous sizing nozzle, but due to the martensitic transformation of zirconia and its accompanying volume Changes, it is easy to cause the nozzle to burst during use. Therefore, this kind of water must use stable zirconia as a raw material, but its content should not be too high. The expansion coefficients of zircon and zirconia are different, and it is easy to cause nozzle cracking when making the nozzle. In order to avoid this problem, it is necessary to minimize the difference between the expansion coefficients of the two. Therefore, the water sizing end working surface The content of zirconium oxide in the slab must be controlled at 70-80%, but this is not conducive to the improvement of the sizing water life.
⑶ Vibration forming sizing nozzle
The vibration forming sizing refractory nozzle is composed of the nozzle body, the nozzle core and the iron shell. The nozzle body is made of high alumina material, and the nozzle core is made of zircon and zirconium oxide. The firing temperature is 1620-1650°C. The nozzle adopts vibration and pressure to form the nozzle core, the high aluminum material and the iron sheet outer wall prepared in advance, and it can be dried after the molding without firing. The advantage of this kind of water is simple production and preparation process, lower production cost, but the disadvantage is that it is easy to cause leakage accidents after long-term use.
⑷Inlaid sizing nozzle
The body of the inlaid sizing nozzle is made of high-aluminum material, and the nozzle core is made of zircon and oxide compound. The two are made separately, and then the two are bonded together with fire clay. Therefore, if the water body and the water core are not well bonded, the water core will fall off after long-term use, which will cause the continuous casting production to not proceed normally, but the advantage of this nozzle is that the production cost is lower and the thermal shock is stable. The sex is better.
Common sizing nozzles are prone to problems such as diameter expansion and cracking during use, while zirconia sizing nozzles are widely used due to their good thermal shock resistance and corrosion resistance.
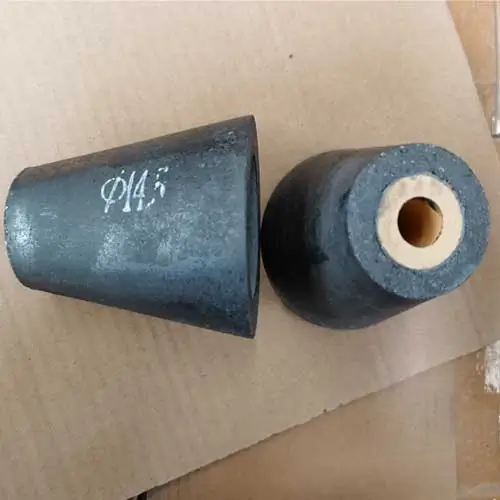
According to the gradual reduction of the particle size of the raw materials used, the zirconia type sizing nozzle can be divided into: coarse particle type sizing nozzle, fine particle type sizing refractory nozzle and ceramic type sizing nozzle.
(1) Coarse particle type sizing nozzle
The zirconia particles selected for the coarse-grained sizing nozzle are larger (up to 2mm), so the advantage of this nozzle is that it has good thermal shock resistance and is not easy to burst during use, but the disadvantage is that it has low compressive strength. The porosity is higher.
(2) Fine particle type sizing nozzle
The raw material particles of the fine-particle type sizing nozzle are relatively fine (particle size <50um), so the microstructure of the nozzle is relatively uniform. The advantage is lower apparent porosity, higher strength, and good corrosion resistance, but the disadvantage is heat resistance The seismic stability is poor, and the phenomenon of bursting occurs at the moment of pouring.
(3) Ceramic type sizing nozzle
The raw material particles used in the ceramic sizing nozzle are very fine (particle size <5um), so the strength of the nozzle is very high, the apparent porosity is very low (<5%), but its thermal shock resistance is poor, and the molding and firing The manufacturing process is more complicated, and it is prone to bursting during use.
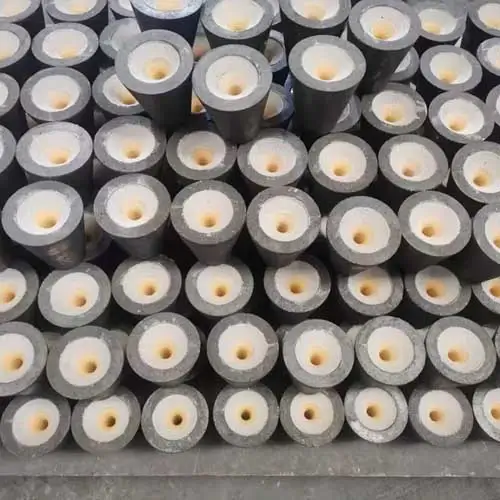