Steel bag weekly transfer process: Turn on the furnace/electric furnace out of steel for one or two refined treatment, one consecutive casting steel, one steel bag is prepared to wait for the steel. The normal turnover time is 100 ~ 140min depending on the difference between steel and connecting machines. The temperature of the steel bag is 1680-1700 ° C, and the steel time is 100 ~ 120 minutes. ~ 11%, FeO 18%~ 22%. If ultra -low -carbon steel technology such as silicon steel, bridge steel, car plate steel, etc. must be treated with vacuum treatment, it must be stirred at the bottom of the steel and the LF furnace is heated through the arc, the atmosphere of the furnace is restored, the refining of the slag, and the gas stirring of the gas, etc. Tower, strengthen the comprehensive refining effects such as thermodynamics and dynamic conditions, desulfurization, alloy, and heating up. Therefore, the range of slag base is large, and the temperature of steel and scum is higher. The mixing power is large, and the lining of the steel bag is damaged.
Causes of damage to the refractory material of steel bag
- 1.Steel bags are used to transport high -temperature steel water. During the transportation, high -temperature steel water and slag at about 1680 ° C were emitted to erosion, especially the slag line, which was seriously erosion and was an important factor in determining the life of a can.
- 2.Refining treatment outside the furnace is seriously damaged by non -burning bricks.
- 3.When the steel is out of the furnace, the inner lining is affected by a severe temperature change, which causes the cracks and peeling of the inner lining material.
- 4.When the steel bag is loaded into the steel water, the high -temperature steel water has a strong mechanical scour on its bottom, resulting in damage caused by the inner lining material of this part.
Damage mechanism of ladle refractory
The damage mechanism of ladle refractory materials is mainly caused by high-temperature slag erosion and penetration. The slag line of the ladle is mainly melted, and the side wall is cracked and thermally peeled due to the penetration of slag. The melting rate is related to the slag temperature, viscosity and reaction rate of the material. The high temperature of molten steel, the long retention time in the ladle, the low viscosity of slag, and the pore penetration, liquid phase penetration and diffusion in the solid phase of the matrix material cause qualitative changes in the composition and structure of the material surface, forming a metamorphic layer with a high degree of solubility, which is prone to peeling and accelerates the damage of the lining bricks. Ladle linings with the same or different chemical compositions of refractory materials have different organizational structures and properties, and the damage rate is also different. The ladle cannot operate continuously, resulting in a decrease in the lining temperature or even a cold ladle, which is also prone to lining structure peeling, reducing the service life of the ladle.
The erosion of slag on refractory materials is not limited to the dissolution of the surface, but the slag can also invade (penetrate) the interior of the refractory materials, expand its reaction area and depth, and undergo qualitative changes in its composition and structure near the surface of the material, forming a highly soluble metamorphic layer, which accelerates damage. The proportion of this invasion is roughly proportional to the porosity. Therefore, even if the chemical composition of the refractory materials is the same, their melting loss rates are significantly different due to their different organizational structures.
The higher the open porosity of the refractory material, the faster the slag invasion rate is, and the invasion ratio is approximately proportional to the porosity. Even if the apparent porosity of the refractory materials is the same, the erosion rate will change if the shape, size and distribution of the pores are different.
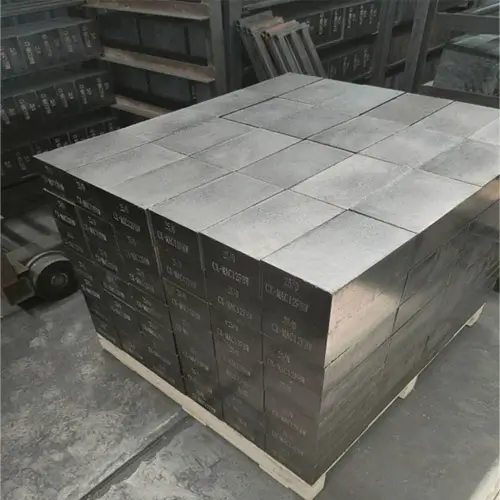
Characteristics of refractories for ladle linings
Based on the above analysis, the ladle lining refractory material should have the following characteristics: dense and uniform organizational structure; micro-expansion at high temperatures, good volume stability; high strength, and a small ratio of medium-temperature strength to high-temperature strength.
During the use of refractory materials, molten slag easily penetrates from the heating surface into the depths of the refractory material, causing the porosity near the working surface to significantly decrease and become densified, forming a very thick metamorphic layer. When the temperature changes drastically, cracks parallel to the working surface will occur at the interface between the metamorphic layer and the original brick layer, causing the bricks to peel off and be damaged. The way to reduce the structural spalling of refractory materials is to reduce the depth of slag penetration. This can be done from the following aspects:
(1) Improve the slag permeability resistance of refractory materials;
(2) Reduce the porosity of refractory materials and reduce the erosion channels of slag;
(3) Slag reacts with refractory materials to form a high melting point compound retaining wall to prevent the penetration of slag;
(4) Increase the viscosity of slag. The greater the viscosity of slag, the less corrosive it is to refractory materials.
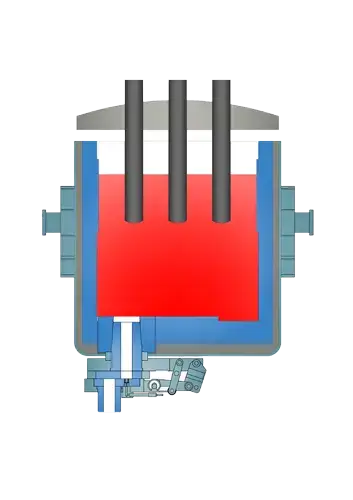