Magnesium carbon brick is a new type of refractory material emerged in the 1970s, it is high temperature sintered magnesium sand or electrofused magnesium sand and carbonaceous materials as raw materials, with a variety of carbonaceous bonding agent made of non-burning refractories, magnesium carbon brick that maintains the advantages of carbonaceous refractory materials, and at the same time completely changed the previous alkaline refractory materials with poor resistance to flaking performance, easy to absorb slag of the inherent shortcomings.
In the iron and steel metallurgy industry is still a large number of use of magnesium carbon bricks, magnesium carbon bricks application has improved the converter of the various technical wood economic indicators, reducing the consumption of refractory materials. In addition, as a kind of non-burning products, compared with the traditional fired magnesium dolomite bricks, magnesium carbon brick production fuel consumption savings of at least 80%.
Properties of magnesium carbon bricks
Magnesium carbon brick because of its constituent materials are magnesium oxide and carbon, both have a high melting point, and the two components are not solid fusion, so magnesium carbon brick has a high resistance to melting performance. Magnesia-carbon brick is a composite structure, the main part of which adopts the magnesia clinker which has strong slag resistance to alkaline slag and carbon which has poor wettability with slag, so it has excellent slag resistance. Especially its resistance to slag penetration ability is strong, compared with the old type of fired alkaline brick, magnesium carbon brick penetration layer is much shallower.
By dry graphite has excellent thermal shock resistance, so inherited the excellent characteristics of graphite magnesium-carbon bricks, has a high thermal conductivity, the coefficient of linear expansion and modulus of elasticity is relatively small, and high-temperature strength of the characteristics of the larger, basically avoiding the use of the process of organisational damage due to the chipping and spalling phenomenon. In addition to the above excellent characteristics of magnesium carbon brick, but also has a better thermal creep resistance, magnesium carbon bricks and other ceramic bonded bricks, compared with the display of particularly good resistance to change.
Application of magnesium carbon bricks on converter steelmaking
Since the introduction of oxygen converter, furnace lining materials have gone through three stages of evolution: tar dolomite bricks – fired alkaline oil-impregnated bricks – magnesium-carbon bricks.Since the 1980s, the steelmaking converter and its lining refractory materials have had a great deal of development in terms of the steelmaking converter, has been completed to the large-scale, automated development of the process. At present, it is developing to double blowing and high temperature.
In the smelting process, the use of each part of the converter conditions, damage is different, for different conditions of use of each part of the converter, the masonry refractories are not the same.
At present, integrated masonry is commonly used to improve the technical and economic indicators of the converter.
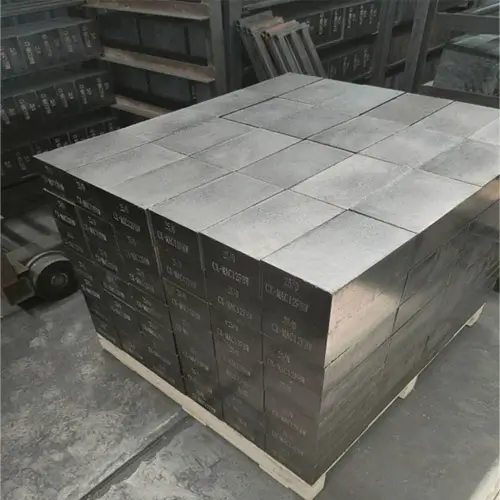
Magnesium-carbon bricks in electric furnaces
At present, almost all of the furnace walls are built with magnesium carbon bricks, so the life of magnesium carbon bricks determines the service life of the furnace, the main factors that determine the quality of magnesium carbon bricks for the furnace include the purity of magnesium sand as the source of MgO, the type of impurities, the bonding state of the magnesite grains and the size of the grains; as a source of carbon introduction of the scalar graphite purity, the degree of crystallinity and the size of the scales; usually use thermosetting phenolic resins as a bonding agent, the main Influencing factors are the amount of addition and the amount of residual carbon. Now it has been proved that the magnesium carbon bricks add antioxidant can change and improve its matrix structure, but in the normal operating conditions of the electric furnace, antioxidant is not a necessary raw material for magnesium carbon bricks, and only used in high FeOn slag arc furnace, such as the use of direct reduction of iron or irregular oxidation of the parts as well as hot spots of the electric furnace, add a variety of metal antioxidants to become an important part of magnesium carbon bricks. Component.
The erosion behaviour of magnesium-carbon bricks used in the slag line area is characterised by the formation of a pronounced reactive dense layer and a decarburised loose layer. The reaction dense zone, also known as the slag erosion zone, is the erosion area where the high temperature liquid-phase slag penetrates into the brick body after the decarburisation of magnesium-carbon bricks and the formation of a large number of pores. In this region, FeOn in the slag is reduced to metallic iron, and even the dissolved phase and intergranular Fe2O3 solidly dissolved in MgO are also reduced to metallic iron. The depth of slag penetration into the brick is mainly determined by the thickness of the decarburised loose layer, which usually terminates at the residual graphite. Under normal conditions, the decarburisation layer in magnesium-carbon bricks is relatively thin due to the presence of graphite.
There are two ways of steel outlet of electric furnace: steel outlet trough tilting outlet and steel outlet at the bottom of furnace. When the steel outlet trough is used for tilting steel outlet, magnesium-carbon bricks are basically not used, but Al2O3 or ZrO2, and non-oxygen substances such as C, SiC and Si3N4 are added. When the bottom of the furnace steel outlet, the outlet consists of external casing bricks and internal pipe bricks. Furnace bottom outlet with magnesium carbon brick tube brick, tube brick aperture size according to the furnace capacity, steel time and other factors to determine the general internal diameter of 140 ~ 260mm.
A steel plant electric furnace in the block and low block magnesium carbon bricks used in the steel outlet, out of the copper outlet on both sides of the part instead of the original use of sintered magnesium bricks initially achieved better results, the age of the furnace by 60 furnaces increased to more than 1 times. After the use of slag line parts of the magnesium carbon brick to maintain a more complete, non-stick slag. Slag line parts do not need to replenish the furnace, that is, to reduce labour intensity and improve the purity of liquid steel and productivity.
The use of Aluminium magnesium carbon bricks in ladles
When MgO-C bricks are used in refining ladle furnaces and ladles, they are mainly used in parts such as clearances and slag lines. According to the operating conditions, these parts require the refractory material used must have high temperature resistance, thermal shock resistance, resistance to slag erosion and other mechanical erosion. So in the past, these parts used to choose magnesium-chromium refractory materials, but considering the chromium pollution of the environment, the amount of its reduction, and now the choice of magnesium-carbon bricks.
Due to the preheating process of the new ladle in the magnesium-carbon bricks will be seriously damaged, loose decarburisation layer can reach 30 ~ 60mm thick. This layer of band in the process of injecting steel that is washed out and will be magnesium sand particles into the slag. Obviously, to prevent the magnesium carbon bricks in the carbon in the preheating is burned off will become the ladle headroom and slag line parts of the magnesium carbon brick service life of one of the important steps. Its technical measures, in addition to the magnesium carbon bricks into the composite anti-oxidant, the key is in the lining after the surface of magnesium carbon bricks with alkaline low-melting glass phase liquid cover to protect the magnesium carbon bricks in the carbon in the ladle in the preheating process is not burned off.
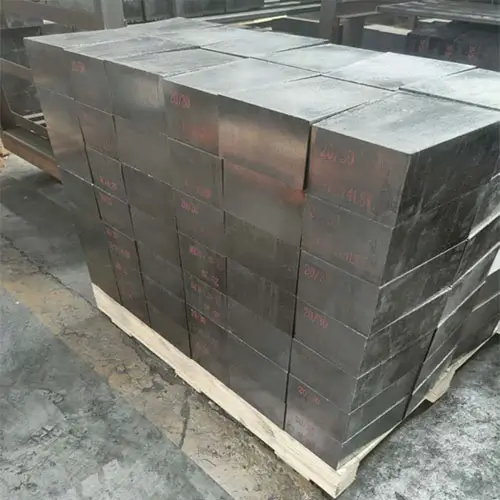