The tundish monoblock stopper is one of the most important control elements in the continuous casting production process, installed in the intermediate package, with the submerged entry nozzle or tundish upper nozzle, in the continuous casting process to control the flow of steel from the tundish to the crystallizer, in order to ensure the stability of the flow of steel in the crystallizer and the stability of the continuous casting process. Due to the non-replaceability of the monoblock stopper in the process of use, once the monoblock stopper problem occurs, it will lead to the steel flow out of control or even stop pouring, so that the continuous casting is interrupted, thus resulting in serious cases of accidents or huge economic losses. Steel enterprises in the tundish monoblock stopper application process problems to analyze and put forward effective countermeasures for various types of problems.
The main problems arising from the use of tundish monoblock stopper
1.Problems in the use of monoblock stopper heads
Monoblock stopper heads is the key part of the monoblock stopper, the rod head and the upper nozzle with play a role in controlling the flow, so the rod head needs to be excellent resistance to scouring. Monoblock stopper heads material is generally aluminum carbon, magnesium carbon, spinel carbon, zirconium carbon, etc., carbon content design is generally relative to the body of monoblock stopper heads carbon content is much lower. tundish monoblock stopper head in the use of the process of the main problems occurring in the head of the serious scouring, plug the head of the two aspects of the rod off.
A. Heavy scouring of monoblock stopper head
Monoblock stopper head scouring serious, you can see that the head arc has been scoured into the shape of the depression, monoblock stopper head shape change with the bowl of the mouth of the bowl of the tundish upper nozzler deterioration, resulting in the monoblock stopper flow control instability or even lose the role of flow control. The height of monoblock stopper is reduced from 1250mm to 1225mm, and the head of monoblock stopper is washed away by 25mm. The reduction of the height of stopper will lead to the stopper not being able to control the flow effectively and not being able to be closed properly when the pouring is stopped.
B. Tundish monoblock stopper stick turnaround
The head of monoblock stopper was separated from the body of monoblock stopper, the height of monoblock stopper was reduced from 1725mm to 1600mm, and the head of monoblock stopper was dropped by 125mm. The monoblock stopper could not control the flow properly, which led to the stoppage of continuous casting.
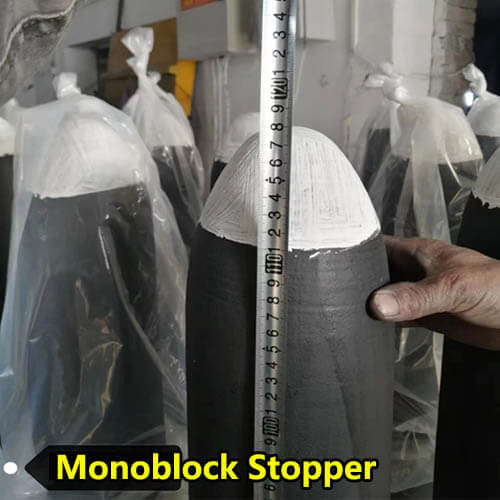
2.Problems in the use of tundish monoblock stopper body
Monoblock stopper body consists of rod body material and slag line material. Monoblock stopper body needs appropriate strength to keep monoblock stopper in the use of the process does not break, generally aluminum carbon; Monoblock stopper body slag line needs good resistance to slag erosion, generally spinel carbon, zirconium carbon and so on. Monoblock stopper body in the use of the main problem of transverse fracture, transverse fracture is divided into the body part of the transverse fracture and slag line part of the transverse fracture.
Monoblock stopper body parts in the pouring process of steel monoblock stopper wall thickness is sufficient in the case of transverse fracture, usually occurs in the middle of the monoblock stopper, the fracture is flush, knife-like.
3.Problems in the use of monoblock stopper connectors
Monoblock stopper connection generally has a metal wire plug, carbon or ceramic wire plug and pin hole and other methods, of which the metal wire plug is most widely used, the current common for the M39 metal wire plug. Monoblock stopper connectors play an important role in the continuous casting process, if the connection is not tight or fall off will lead to continuous casting stop pouring. The common problems in the use of monoblock stopper connectors include melting of the connectors and cracking of the end of monoblock stopper.
Analysis of major problems in use and improvement measures
1.Analysis of problems in the use of monoblock stopper head and improvement measures
A.Analysis of serious causes of monoblock stopper head scouring and improvement measures
Monoblock stopper heads material and continuous casting process is compatible with the important aspects of the impact of monoblock stopper heads scour, generally speaking, depending on the casting steel and refractory reaction to select head material. The erosion of monoblock stopper heads mainly consists of three aspects: physical scouring, carbon oxidation and oxide reaction. When the vacuum is high, MgO will react with C, resulting in accelerated erosion of the bar head; when the Ca content in the liquid steel is high, it will react with Al2O3, accelerating the erosion of the bar head; when the oxygen content in the liquid steel is high, it will accelerate the gasification of C, resulting in accelerated erosion of the bar head. For different kinds of steel, different operating conditions should choose the right material for monoblock stopper heads, Al2O3-C monoblock stopper heads than MgO-C monoblock stopper heads is more suitable for Al sedentary steel, while the latter is very suitable for calcium treatment of steel, when pouring steel, the monoblock stopper heads surface formed by the CaO-Al2O3 compounds and MA, M2S thin slag film can effectively protect the head of monoblock stopper heads is not eroded by the molten steel, ZrO2-C rod can be better adapted to the complex environment of continuous casting of steel composition. ZrO2-C monoblock stopper heads can be better adapted to the complex steel composition of the continuous casting environment, which is mainly due to the erosion resistance of ZrO2.
Baking time is too long monoblock stopper head abnormal scouring of an aspect. Generally, the baking time of monoblock stopper is generally 2h, more than 4h baking will lead to the destruction of the anti-oxidation glaze layer of monoblock stopper stick, resulting in the oxidation of the head of the plug stick from the surface layer to the inner layer. And with the extension of baking time, the oxidation depth of the monoblock stopper head increases. After oxidization, the carbon bond is destroyed, and it is rapidly destroyed under the high-speed steel washout.
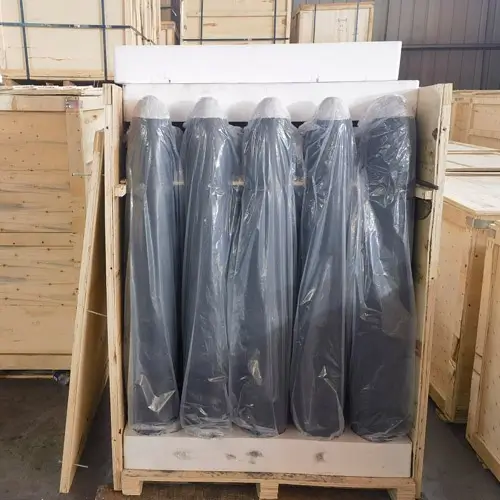
B.Analysis of the causes of monoblock stopper head drop and improvement measures
There are many reasons why the head of monoblock stopper can fall off, generally thermal as well as mechanical stresses. The phenomenon of monoblock stopper plugs falling off due to thermal stress is more common. Monoblock stopper before use generally after about 2h baking, baking the final temperature is very important, generally to reach 1100 ℃. Baking temperature can not be reached, monoblock stopper in the open casting contact with high-temperature molten steel suddenly heated, due to the head and body of monoblock stopper with different coefficients of thermal expansion, in the monoblock stopper internal heat into the force, resulting in the plug due to the concentration of thermal stresses when the head off. The key to solving this kind of problem is to strictly implement the baking system of plug stick.
In addition, some steel mills require the whole monoblock stopper to close the baking, resulting in the tip of monoblock stopper can not be effectively baked, which will also cause monoblock stopper in the opening of the casting of the internal thermal stress concentration and the phenomenon of falling head. Following Figure is the number of mold state diagram when tmonoblock stopper off the baking, can be seen that the baking temperature of the tip part of monoblock stopper bar is low.
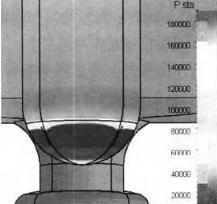
There are many cases where monoblock stopper breaks due to mechanical stress. The head of monoblock stopper is installed off-center with upper nozzle, monoblock stopper rod is used to hit the upper nozzle operation when the upper nozzle is clogged, and too much force is applied when the immersed nozzle is changed quickly, all of which can cause the head of monoblock stopper head to fall off.
2.Analysis of monoblock stopper body use problems and improvement measures
Continuous casting process monoblock stopper body transverse breakage occurs more common, which is caused by thermal stress, mechanical stress, chemical erosion and other reasons for the high proportion of fracture.
The main reasons for the fracture of the body of monoblock stopper are thermal stress and mechanical stress fracture. One of the main factors affecting thermal stress is the baking time and baking temperature of monoblock stopper. Mechanical stress fracture is caused by a variety of reasons, such as the installation of monoblock stopper is not centered on the nozzle outlet, the operation of too much force, the tundish encrustation caused by monoblock stopper can not be lifted and lowered, and so on. This kind of problem can be solved through the strict implementation of the baking system, the training of the main operator of monoblock stopper, improve the continuous casting process and so on.
The monoblock stopper slag line part of the abnormal erosion causes mainly have material selection is not adaptable, wrong operation and other reasons. First monoblock stopper slag line material selection should be suitable for continuous casting process requirements. According to continuous casting slag and tundish covering agent composition selection of suitable slag line material is necessary. For example, MnO high steel avoid choosing material containing SiO2, SiC and single Si powder, in order to avoid the formation of silicon manganese oxygen low co-melting point phase, resulting in increased erosion.
The ladle slag is also one of the common causes of abnormal erosion of monoblock stopper. Due to the continuous casting process ladle automatic slag detection system failure or improper control of the ladle slag, resulting in a larger amount of ladle slag into the middle ladle, and at the same time due to the slag plate slag blocking effect is poor or no timely slag discharge, ladle slag accumulates around monoblock stopper, resulting in abnormal erosion of monoblock stopper slag line.
Throwing crystallizer protective slag to the tundish pack is also one of the reasons for the abnormal erosion of monoblock stopper bar slag line. Continuous casting process due to the low temperature of tundish and other reasons, resulting in the tundish pack liquid surface crust. Encountering such a situation, the operator sometimes chooses to put in the melting temperature lower crystallizer protective slag to avoid crusting. Due to the strong erosive nature of the crystallizer protective slag, it leads to abnormal erosion of monoblock stopper slag line.
3.Connector use problem analysis and improvement measures
Problems at the monoblock stopper connectors include monoblock stopper bar tail crossing over as well as the filament rod melting, both of which happen a lot. The main reason for the transverse breakage at monoblock stopper silk plug is the installation of monoblock stopper. Installation process of the rod of the tightening force is too large, debugging process of bumping and so on will cause the end of monoblock stopper transverse breakage. monoblock stopper tail internal metal wire plug, in the monoblock stopper molding process buried in, resulting in the plug for monoblock stopper body is relatively weak area. Installation process to grasp the strength of moderate, strengthen the installation of the end of monoblock stopper after the inspection, found cracks in a timely manner off the line.
The root cause of the melting of monoblock stopper connector is a problem with the design of monoblock stopper. Monoblock stopper design is shorter, the tail can not be exposed in the package cover, in the high temperature baking or use, the temperature at the connector is too high, it will cause the rod melting. The fundamental measure to solve this problem is to lengthen monoblock stopper so that the connecting parts are exposed in the package cover. Lengthen the monoblock stopper must change the monoblock stopper mechanism, some steel mills are limited to the tundish plug rod mechanism height has been fixed, you can take monoblock stopper cross arm can be made into a step-like high plug rod, as shown in following Figure.
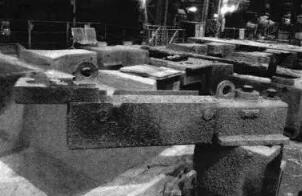
In addition, applying fire clay between monoblock stopper and the connecting parts and using asbestos gasket instead of graphite gasket between the rod and the connecting parts are convenient temporary measures. The application of fire clay between the screw and the connectors can to some extent prevent heat transfer and reduce the risk of melting of the connectors; the use of asbestos gaskets instead of graphite gaskets, which are easy to burn and exothermic, can also reduce the risk of melting of the connectors; however, these two measures can not solve the problem fundamentally.