Heating furnace refractory function
Heating furnaces are divided into continuous heating furnaces, pusher heating furnaces, regenerative heating furnaces and roller bottom heating furnaces. According to the different conditions of heating capacity, material grade and material shape, the appropriate heating furnace type is selected. The heating furnace used for metal heat treatment is also called a heat treatment furnace. The heating furnace before the initial rolling of the ingot or the heating furnace that makes the internal temperature of the ingot uniform is called a soaking furnace.
The heating furnace is mainly composed of a regenerative chamber insulated by refractory materials (dense insulating materials), a furnace that supports and transports the heating parts, a furnace body and a heat recovery system. The heating furnace uses oil, natural gas, electricity and coal as the main fuel as the heat source. The furnace temperature and furnace pressure are controlled automatically, and of course they can also be controlled manually.
Refractory materials play an important role in controlling energy consumption and improving the efficiency of heating furnaces. The service life of refractory linings and the production efficiency of heating furnaces depend to a large extent on the correct selection of refractory materials, the design results of refractory materials and the precise masonry method.
The function of the heating furnace refractory lining is to prevent heat loss from the furnace body and ensure that the outer surface temperature of the heating furnace body is low to meet the safe working conditions around the heating furnace body, thereby helping to achieve the unit fuel consumption target. The design structure of the refractory material also fully considers the problem of minimizing heat loss from the side walls, furnace roof and furnace bottom.
1.Advantages of Advanced Refractory Solutions
- Practical and reliable heating technology, such as walking bottom heating furnace, walking beam heating furnace and pusher heating furnace, for various types of heat treatment furnaces, the working temperature can reach 1500℃;
- Significant energy saving effect: With rich professional technology and the best selection of refractory products, the refractory lining can be made to have a longer life and better insulation performance;
- Simple process, short shutdown period, through rapid masonry technology, shorten the relining time, and maximize production efficiency;
- Provide users with high-quality technical services through reheating project experience, including various general contracting projects and maintenance/improvement projects.
- Generally speaking, the refractory solutions for heating furnaces include providing a complete set of solutions for new projects and upgrade and renovation projects. Specifically, there are refractory solutions for heating furnace nose, heating furnace feed and discharge end low wall, refractory brick furnace roof, burner silencer refractory brick, slider support refractory brick, feed and discharge furnace wall special brick, pusher heating furnace, etc. It also includes solutions for shotcrete refractory technology and simple and fast refractory masonry processes, which can greatly shorten the downtime of heating furnace relining and transformation.
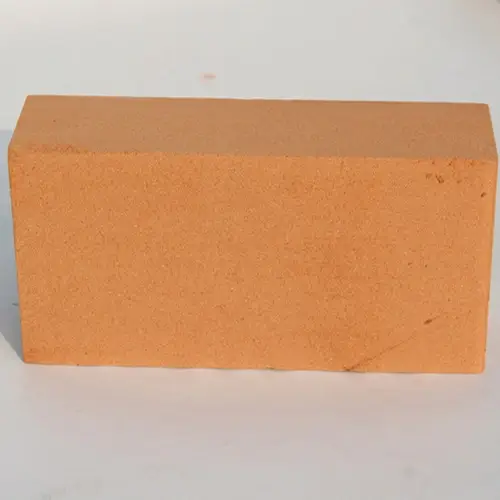
2.Overall refractory solution for heating furnace
In today’s world, the refractory materials for masonry heating furnaces are increasingly using monolithic refractory materials, replacing the old refractory bricks. The main advantage of changing from refractory bricks to monolithic refractory structures is that they reduce the downtime of the heating furnace and improve the production efficiency of the heating furnace. Monolithic linings can also minimize the downtime and maintenance costs of refractory relinings, and can also improve the thermal stress caused by frequent cooling and heating during maintenance. If refractory bricks are used, the number of joints in the refractory brick structure is large, and the hot coal gas can easily transfer heat through the refractory brick lining, resulting in an increase in the furnace shell temperature. The number of joints in the monolithic refractory lining structure is small, and it has little effect on the furnace shell temperature.
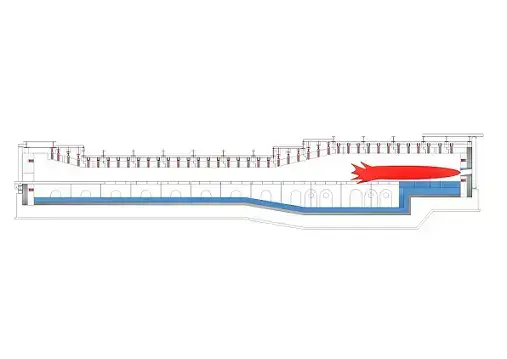
More details about Reheating Furnace:
What is the process of reheating a furnace?
Reheating Furnaces serve the purpose of heating steel blooms, billets or slabs in steel rolling mills. Reheating furnaces takes this steel stock up to approximately 1200 degree Celsius. The steel begins to deform at this temperature, and the steel rolling process can begin.
What is the temperature of a reheating furnace?
An oil-fired reheating furnace has an operating temperature of around 1340°C. Average fuel consumption is 400 litres/hour. The flue gas exit temperature is 750 °C after air preheater. Air is preheated from ambient temperature of 40 °C to 190 °C through an air pre-heater.
What fuel is used in reheating furnace?
Most metal industries use reheating furnaces (RHF) for their finishing operations. This RHF is highly energy-consuming equipment that heats the material inside the chamber for rolling or shaping using the by-product gases, natural gas, or oil as fuel.
What are the zones of reheating furnace?
Reheating Furnaces can be divided into five zones: Non-firing, charging zone, preheating, heating and damping. Energy for heating is supplied by the tangential combustion of roof and bottom gases.