Production of refractories for alumina
(1) Refractories for rotary kiln. Rotary kiln is divided into pre-tropical, firing belt and cooling belt. Firing belt working temperature is not higher than 1200 ℃, kiln insulation layer structure for the first by the furnace shell laying a layer of refractory fiber felt, and then with diatomaceous earth bricks, clay heat-insulating bricks or bleached bead bricks and other heat-insulating bricks masonry, can also be used as a bulk density of 0.8g/cm³ lightweight refractory castable overall pouring.
(2) flash roaster with refractory materials. The furnace group consists of flash furnace, preheating furnace, residence tank, fluidized dryer and cooler and other parts. The maximum working temperature is about 1100 ℃, the maximum flow rate of the material in the section of the furnace body is about 30m/s. The whole roasting process of the material in the furnace is carried out under the conditions of high temperature, high speed and constant change of the flow direction, so it produces wear and tear on the furnace lining. The furnace lining body is generally poured with high-strength aluminum silicate refractory castables.
(3) Refractory materials for alumina electrolyzer.
The sectional structure of the aluminum electrolyzer is shown in Figure 1. 1-Steel base plate; 2-Cathode steel rod conductor; 3-Tank bottom charcoal block; 4-Sidewall charcoal block;
5-Electrolyte; 6-Pre-roasted carbon anode; 7-Alumina; 8-Electrolytic Aluminum; 9-Clay bricks non-working layer with alumina and cryolite (Na₃A1F₆) melt composition of the electrolyte, the electrolyte solution into the electrolytic tank energized at a temperature of 950 ~ 970 ° C to make the alumina decomposition of the metal into aluminum and oxygen.
Aluminum electrolyzer non-working layer thickness is generally 240 ~ 400mm, the first by the trough shell laying a layer of insulation board or refractory fiber felt, followed by masonry clay heat-insulating bricks or drifting bead brick, can also be poured bulk density of 1.0g/cm³ lightweight refractory castables, and finally masonry ordinary clay bricks; working layer of carbonaceous or silicon nitride combined with silicon carbide refractory materials masonry, able to resist the infiltration of aluminum liquid, fluoride and The working layer is made of carbon or silicon nitride combined with silicon carbide refractory material, which can resist the penetration of aluminum liquid, the erosion of fluoride and electrolyte as well as molten sodium salt and prolong the service life.
Refractories for Aluminum Smelting
(1) Refractories for reflex furnaces. The furnace is divided into two types: fixed and tilting type, generally using gas or heavy oil as fuel.
Aluminum melting is usually fixed reflector furnace. Reflector furnace non-working layer with refractory fiber felt and clay heat-insulating brick masonry, melting pool above the part of the working layer of clay brick masonry in general, can also be used in high alumina refractory castable prefabricated blocks suspended or poured at the scene or with high alumina refractory plastic pounded into.
(2) Refractory materials for rotary furnace. The non-working layer of the furnace with clay heat-insulating bricks or drifting bead brick masonry, can also be used for bulk density of 1.0g/cm³ lightweight refractory castable material pouring or made into prefabricated blocks masonry; working layer with dense clay bricks or Al₂O₃ content of more than 55% of the high alumina brick masonry.
(3) refractory materials for induction furnace. The furnace is generally lined with clay bricks or third-class high alumina brick masonry. The bottom of the furnace is sometimes first poured with high-alumina refractory castables at the grass-roots level, and then masonry high-alumina bricks. Induction furnace capacity is less than 10t, the lining can be used Al₂O₃ content of about 75% of the high-alumina refractory castables or refractory pounding material production, but also can be used corundum refractory castables or dry vibration material.
(4)Refractories for holding furnace and aluminum water tank. Aluminum holding furnace is divided into slot induction furnace, resistance heating pool furnace and gas chamber furnace. This type of equipment due to the low operating temperature, generally use clay bricks and other materials for lining, but also obtained a high service life.
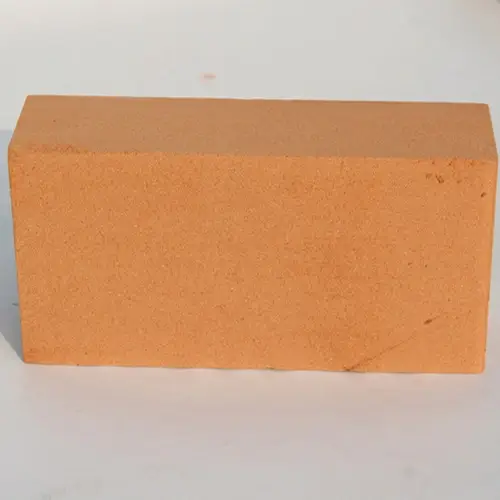
Flash Melting Furnace
The main process of copper pyrometallurgical smelting is very similar to nickel smelting, with differences only in the following aspects: the product of the copper smelting converter is crude copper, while the product of the nickel smelting converter is high icy nickel (nickel matte with a high nickel content); copper electrolytic refining uses copper anode plates, while nickel electrolytic refining uses Ni₃S₂ anode plates.
Ausmalt Furnace vs Edsa Furnace
China’s Jiangxi Guixi smelter built copper melting flash furnace, Gansu Jinchuan Metals Company built nickel melting flash furnace. Flash furnace is mainly composed of reaction tower, sedimentation tank and rising flue. Its advantage is that the ore roasting and smelting combined together, rapid reaction, low energy consumption, greatly reducing the non-ferrous metal smelting process of environmental pollution.
The upper part of the reaction tower has higher oxygen pressure and lower temperature, and the tower wall forms a Fe₃O₄ protective layer, which is constructed by directly bonded magnesium-chromium bricks. Fused magnesium-chromium bricks are difficult to generate, with very low productivity and high cost, and have been replaced by molten granular re-bonded magnesium-chromium bricks in recent years. The top of the tower is spherical vault or hanging flat roof, using direct bonded magnesium-chromium bricks.
Noranda Furnace and Silver Furnace
Noranda smelting furnace was developed by Canada, for a horizontal long cylindrical melting pool melting furnace. China’s Daye Smelter and other such furnaces. Noranda furnace production capacity, low energy consumption, mainly by self-heating melting. Noranda furnace vulnerable parts is the wind mouth, wind mouth area, precipitation area slag line and out of the ice copper mouth. Originally, these parts are masonry cast magnesium-chromium bricks, now in addition to the ice out of the copper mouth, have been changed to use the melt and then combined with magnesium-chromium bricks. The remaining parts of the main use of direct bonded magnesium-chromium brick.
Silver furnace developed for our country. Its principle and Noranda furnace is similar. Silver furnace vulnerable parts of the melting area of the wind and the vault and the partition wall and precipitation area slag line parts. Wind mouth area with cast magnesium-chromium bricks or molten particles and then combined with magnesium-chromium bricks, slag line area with half and then combined with magnesium-chromium bricks.
Converter
Copper refining and nickel refining blowing mostly adopt P-S converter, which is a cylindrical horizontal converter. In order to improve the resistance to thermal and structural spalling of magnesium-chromium bricks in the air vent area of nickel converter, and to reduce the infiltration and erosion of iron-silicon slag and nickel matte on them, we can appropriately increase the content of Cr₂O₃ and Al₂O₃ in the magnesium-chromium bricks, and decrease the content of Fe₂O₃ and the impurities of CaO and SiO₂. The increase of Cr₂O₃ and Al₂O₃ content in the brick can improve the content of intergranular spinel in the brick, improve the degree of direct bonding and the strength of the brick, so as to improve the brick’s resistance to the infiltration of iron and silica slag and matte and the ability to resist erosion.
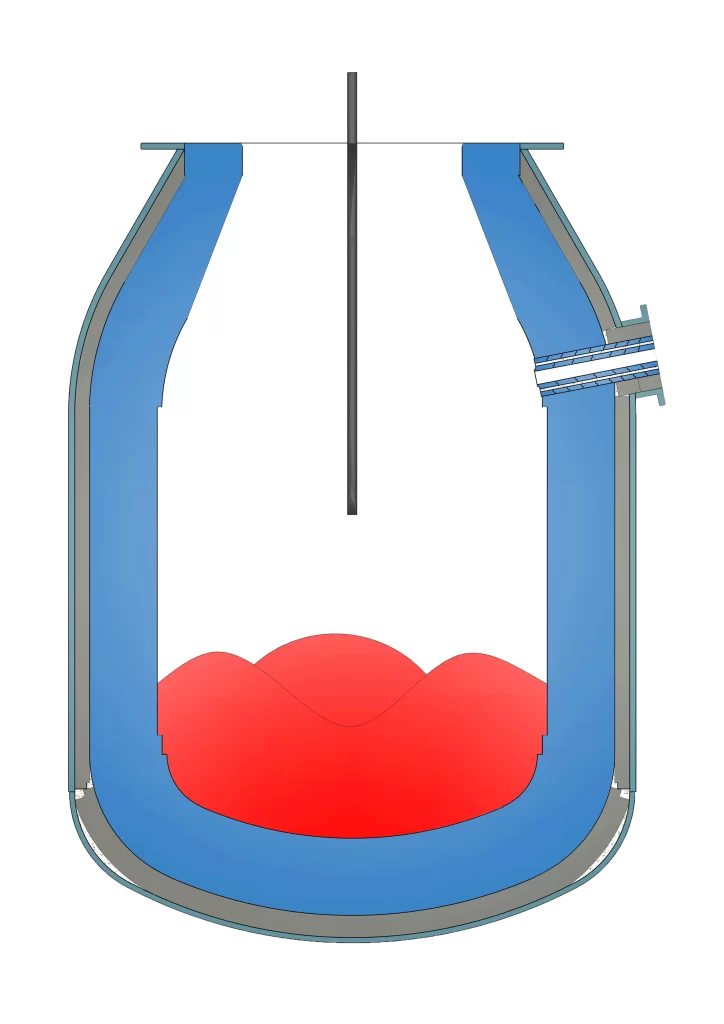