The key technology of smelting clean steel is slag-free steel, i.e. the sliding water outlet slag blocking technology is adopted in the steel outlet of converter. Due to the very rapid opening and closing of the sliding plate, it can effectively block the pre-slag and post-slag in the process of steel discharge, and it can realize automatic slag judging and slag blocking through the combination of infrared slag detecting technology and PLC control technology, which is one of the best production technology for slag blocking in converter steel discharge at present. The sliding plate slag blocking technology, realize the fast slag blocking, slag blocking success rate increased, the average slag thickness is reduced, improve the alloy and deoxidizer yield, reduce the amount of phosphorus back to the molten steel, reduce the refining slagging agent and all kinds of deoxidizer consumption.
A steel plant in Hebei has a 120t converter, since its commissioning, it has adopted the slide plate to block the slag out of the steel, and achieved very good smelting results. The smelting steel grades are 60Si2Mn, Q335B, 9SiCr, 33MnCrTiB, 50CrV, 55CrMn, U71Mn, etc. The main products are light rail, heavy rail, crane rail, miner’s steel, elevator steel, spring flat steel and so on.
Damage to the resistant material of the slag blocking system
Converter slag blocking system refractory material includes slag blocking slide plate and steel outlet, the slide plate system is installed at the end of the steel outlet of the converter. The slide plate system consists of inner spout, outer spout, inner slide plate and outer slide plate. The improvement of the service life of slag blocking system refractory material for converter can save labor intensity, reduce production cost, improve production efficiency and safety.
1.Damage to steel outlet
Steel in the high-speed flow through the outlet hole, high-temperature steel flow and the outlet hole to produce a strong scouring of the outlet caused by mechanical damage to the outlet. Oxygen in steel or slag oxidizes the magnesium-carbon steel outlet, making the refractory material structure become loose, thus causing a decline in life.
2.Damage to converter skids
Converter slide plate in the steel process, to withstand high temperature steel, steel slag scouring; multiple slag blocking operations in the process of slide plate and slideway to withstand high temperature steel, steel slag scouring, wear and tear, oxidation and erosion. Therefore, the converter slide plate is mostly made of aluminum and carbon with excellent erosion resistance and thermal shock resistance.
Improvement measures
The original life of the steel outlet was about 200 furnaces, and the life of the slide plate was about 14 furnaces, which resulted in a large consumption of refractory material, high cost and low production efficiency. After several technical improvements, the refractory material for slag blocking in converter has achieved very good utilization effect.
1. Optimization of outlet bore design
The steel outlet adopts the split type, compared with the whole type steel outlet, its density, high temperature strength, erosion resistance have been improved, and the service life is longer.
The original use of the inner hole diameter of 160mm, the steel out of the time 6~8min, too long out of the steel time caused the following negative impact:
(1)Erosion of the furnace lining on the discharge side of the converter is aggravated by the long discharge time.
Longer discharge time leads to greater loss of steel temperature, and thus higher requirements for the temperature of the steel, which also leads to a longer cycle of the converter, lower productivity; flow through the outlet of the molten steel flow and air contact time becomes longer, the molten steel and the nitrogen and oxygen in the air of the contact between the molten steel and the nitrogen and oxidation of the molten steel.
After demonstration, the inner hole diameter of the steel outlet was changed to 180mm, and the taper of the inner hole was increased. It has been proved that the change of hole diameter and taper of the outlet brick can shorten the time of steel outlet’A], from 6~8min to 3.5~5min. The shortening of the time of steel outlet improves the productivity of the converter and reduces the temperature loss of the steel outlet process.
The test results meet the production requirements, so the final decision to use the inner diameter of 150/180mm outlet. The wall thickness at the front end of the spout remains unchanged, but the shortening of the discharge time reduces the erosion of the spout bore, and the average service life of the spout can be increased from 200 to more than 300 furnaces. The average service life of the spout can be increased from 200 to more than 300 furnaces. This reduces the time of replacing the spout and the consumption of spout spraying material.
(2)Use of outlet bowl bricks
Currently used steel spout and inner water spout combination is easy to be eroded by the steel scouring, limiting the life of the spout, so a replaceable bowl brick is installed at this location. When serious erosion and melting of the bowl brick, you can replace the bowl brick at the same time as the replacement of the inner spout, using this method is expected to increase the overall life of the spout of more than 400 furnaces.
(3)Improvement of slag blocking slide plate
The traditional aluminum wrong carbon skateboard used raw material wrong mullite in the use of easy decomposition, resulting in loose structure and skateboard corrosion resistance decline, affecting the skateboard service life to further improve. Replace the wrong mullite with wrong corundum and wrong oxide, and also increase the content of oxide times, which can improve the erosion resistance of the material. Optimize the firing system and firing atmosphere to promote the growth of SiC whiskers within the slide plate. The generation of a large number of SiC whiskers in the matrix is conducive to improving the strength of the material, and at the same time helps to improve the thermal shock resistance of the material.
After changing the shape of the inner hole of the steel outlet, the steel outlet speed increases, the interference between the steel and the steel outlet is weakened, the steel flow is smoother, and the turbulence at the end of the steel outlet is reduced, which avoids the slag rolled in the later stage and reduces the erosion on the surface of the slide plate. The shortening of the steel discharge time reduces the scouring time on the slag blocking slide plate and the inner and outer water ports, which reduces the flaring rate of the slide plate and the inner and outer water ports. After using the new steel outlet, the service life of the slide plate can be increased from about 14 furnaces to about 18 furnaces. Later the test will be changed from the original 150mm hole diameter to 140mm, the steel time did not increase significantly, while the service life of the slide plate can be increased to more than 20 furnaces, up to 23 furnaces.
(4)Dual front and rear slag technology
The use of slag plugs to block the steel before the first slag, and then use the slide plate to block the end of the steel out of the late slag. These two slag blocking methods are used in combination, the slag blocking effect is significantly improved. After the end of the steel with the device will block the slag plug inserted into the slag slide out of the steel hole, relying on greater friction to prevent the impact of the slag in the early stage, so as to achieve the purpose of blocking the slag in the early stage. The front block does not use the slide to block slag, because the slag blocking plug cost is lower, and the use of better results.
In 120t converter, by optimizing the size and taper of the inner hole of the steel outlet, and increasing the replaceable bowl bricks, the time of steel outlet is shortened, and the service life of the steel outlet is improved. In addition, reducing the aperture of slide plate, using slag blocking plugs in the front block and optimizing the material of slide plate can also improve the service life of slag blocking slide plate. By taking the above measures, the average service life of 120t converter sliding plate is increased from 14 furnaces to more than 20 furnaces, and the service life of steel outlet is increased to more than 300 furnaces, and it is expected to increase the service life to 400 furnaces by using the steel outlet with bowl brick.
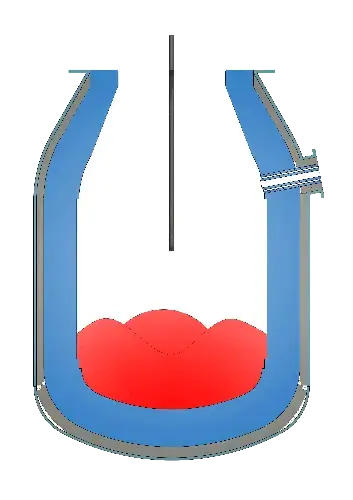