The refractories of ferroalloy electric furnace include three parts: furnace roof refractories, furnace wall refractories and melt pool refractories (furnace slope and bottom). In the process of ferroalloy smelting, different parts of the refractories are in different working conditions.
Furnace top refractories are mainly subject to the erosion and impact of high temperature furnace gas and sprayed slag, the temperature change between charging and the radiant heat of high temperature arc light, and the impact of airflow and pressure change when collapsing materials. Furnace wall refractories are mainly subjected to high-temperature radiation of the arc and the temperature change during the charging interval; high-temperature furnace gas and spray attached slag erosion impact; solid material and semi-molten material impact abrasion; slag near the slag line serious slag corrosion and slag impact. In addition, in the furnace body tilting, the additional pressure.
Furnace slope and bottom refractory materials are mainly subject to the pressure of the upper layer of charge or molten iron; charging intermittent temperature changes, charge impact and arc melting loss; high temperature molten iron and slag erosion impact. In order to ensure that the electric furnace can work properly, must choose refractoriness and load softening temperature is high, hot and cold resistance and slag resistance is good, there is a large heat capacity and a certain degree of thermal conductivity of refractory materials to masonry electric furnace lining.
The performance and use characteristics of the furnace lining refractories often used in ferroalloy production are as follows:
1.Clay brick
The main raw material for manufacturing clay bricks is refractory clay with good plasticity and binding force.
The main performance characteristics of clay bricks are: strong resistance to acidic slag, good resistance to rapid cooling and heating, good thermal insulation capacity and a certain degree of insulation properties; refractoriness and load softening temperature is low. Clay bricks should not be used directly under high temperature conditions and special requirements. In the production of ferroalloys, clay bricks are mainly used for masonry exposed parts of the furnace wall lining of the mineral heat furnace, the role of thermal insulation and insulation of the furnace wall and the bottom of the outer layer of the furnace lining or used for masonry iron package lining.
2.High aluminum brick
The main raw material for manufacturing high alumina bricks is high alumina bauxite, and the binder is refractory clay. Compared with the clay brick, high alumina brick is the biggest advantage of refractoriness, high load softening, good slag resistance, mechanical strength. The disadvantage is that the high alumina brick is not good at resisting rapid cooling and heating.
In the production of ferroalloys, high alumina bricks can be used for masonry iron outlet lining bricks of mineral heat furnace, refining electric furnace roof, can also be used for artillery construction of iron ladle lining.
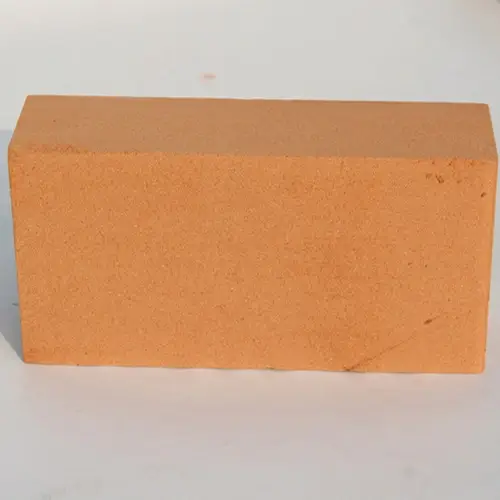
3.Magnesium bricks and Magnesium sand
The main raw material for the manufacture of magnesium bricks is magnesite, and the binder is water and brine or sulfite pulp waste liquid.
The main performance characteristics of magnesium bricks are: high refractoriness, excellent resistance to alkaline slag; but the thermal conductivity and electrical conductivity at high temperatures are large, and the load softening temperature is low, and the resistance to rapid cooling and heating is poor. Pulverization occurs when subjected to water or steam at high temperature.
In the production of ferroalloys, magnesium bricks are used for masonry high-carbon ferrochrome reduction furnace, low and medium-carbon ferrochrome converter, shaking furnace and refining electric furnace furnace wall, furnace bottom and put ferrochrome and low and medium-carbon ferromanganese iron ladle lining and so on. Use magnesium aluminum brick instead of magnesium brick masonry furnace roof. Magnesia has high refractoriness, in the production of ferroalloys, magnesia is commonly used in knotted furnace bottom, making and repairing furnace wall, furnace bottom, and can be used as plugging or making knotted ingot mold with materials.
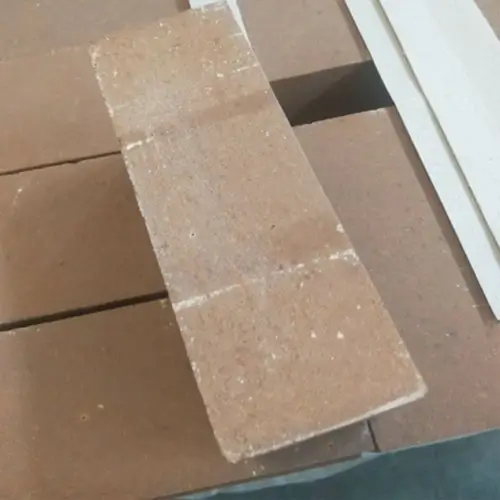
4.Carbon brick
The main raw materials for manufacturing charcoal briquettes are crushed coke and anthracite, and the binder is coal tar or bitumen.
Compared with other common refractories, carbon bricks not only have high compressive strength, small coefficient of thermal expansion, good abrasion resistance, high refractoriness and load softening temperature, good resistance to rapid cooling and heating, but also particularly good slag resistance. Therefore, all smelting is not afraid of carburization of ferroalloy varieties, can be used as a mineral heat furnace lining materials carbon brick.
However, charcoal briquettes are very easy to oxidize under high temperature conditions, and its thermal conductivity and electrical conductivity are larger, in the production of ferroalloys, charcoal briquettes are mainly used for masonry of mineral heat furnace is not exposed to the air part of the furnace wall, furnace bottom.
More details about Ferroalloy electric furnace
What is the downside of an electric furnace?
Millions of Americans use electric resistance heating — most commonly baseboard heating and electric furnaces — to heat their homes. These systems may be cheap and easy to install, but they’re incredibly expensive to operate and fail to provide the year-round efficiency and comfort of heat pumps.
What is the difference between EAF and saf?
In contrast to an electric arc furnace, the main focus of SAF is on reduction and slower metallurgical processes. Therefore, a SAF works much quieter and more stable than an EAF (Electric Arc Furnace) and is usually operated continuously.
What are ferroalloys used for?
The main share of ferroalloys is used in steelmaking for deoxidation and alloying of steels, as well as to modify cast iron, manufacture welding electrodes, and produce compounds as a starting material for the protective coatings for mineral processing.
What are the applications of ferroalloys?
This ferroalloy is obtained by reducing the silica through coking coal in the presence of iron ore in blast furnaces. Its application includes its use as a deoxidizer in the production of stainless steels and for the production of magnesium through a special process known as Pidgeon.