The basic principle of the AOD method is the use of gas dilution method, so that the CO partial pressure is reduced. High-pressure argon and oxygen gas mixture blown into the molten steel and bubbles and slag contact opportunities to increase, conducive to carbon, sulfur, non-metallic inclusions, such as the rapid removal. In the smelting process, AOD furnace slag composition and properties change greatly, alkalinity from the initial 0.6 or so changes to the late 4.0 ~ 4.5, refractory materials from the strong corrosive acidic slag to alkaline slag erosion. The main causes of refractory damage are: gas stirring vortex, resulting in intense turbulence and scouring of molten steel and slag; refining temperature is high (1700 ~ 1750 ℃), fluctuations, resulting in thermal spalling and structural spalling; at high temperatures, alkalinity changes in slag leading to penetration of the furnace lining and melting corrosion. Therefore, AOD furnace refractories should have high temperature strength, good thermal shock resistance, slag resistance and resistance to scouring and abrasion.
The lining of AOD furnace is generally constructed by directly bonded MgO-Cr2O3 bricks, re-bonded and semi-re-bonded MgO-Cr2O3 bricks. Directly bonded MgO-Cr2O3 bricks are made of high-quality high-purity magnesium sand and chromite ore calcined at high temperature, and the microstructure is characterized by the formation of direct bonding between the main crystalline phases, while the low melting point of the silicate phase exists in isolation. Re-combined magnesium-chromium bricks are crushed with electrofused magnesium-chromium sand, and then fired at high temperature, characterized by excellent slag resistance, the use of the effect is better than the direct combination of magnesium-chromium bricks. Semi-recombined magnesium-chromium brick is directly combined with magnesium-chromium brick and re-combined magnesium-chromium brick synthesis, performance is better. Table 1 for the physical and chemical properties of magnesium-chromium brick.
AOD furnace with magnesium-chromium brick damage causes, mainly considering the slag infiltration and the brick body deterioration caused by the structure of the spalling. In order to improve its performance, the production of magnesium-chromium bricks should be considered from the following aspects.
(1) Strictly control the chemical composition, Cr2O3 content (by mass fraction, the same below) to 18% to 20% is good, SiO2 content has the greatest impact on the erosion, its content should be as low as possible, to <1% is appropriate, and should be strictly control the content of CaO.
(2) Brick-making process should be reasonable control of particle grading, and the use of high-pressure molding and ultra-high-temperature firing.
Magnesium calcium series refractories
Magnesium calcium series refractories due to abundant raw materials, low price and widely valued, but easy to hydrate and other defects limit the wide application of the material. the main varieties of AOD furnace lining used in sintered magnesium dolomite bricks and electrolytic fusion of non-burning magnesium dolomite bricks. Sintered magnesium dolomite bricks with high-quality sintered magnesium dolomite sand as the main raw material, high pressure molding, calcined at a high temperature of 1600 ℃ and become. Electromelted magnesia dolomite bricks are made of electrofused magnesia dolomite sand as raw material, molded by high pressure and dried at low temperature. Because the fused magnesium dolomite sand is fully melted, the crystal lattice is complete and the activity is low, so the fused magnesium dolomite bricks have high erosion resistance and hydration resistance.
Selection of refractory materials for AOD furnace
Magnesium-chromium series refractories and magnesium-calcium series refractories are the main refractories used in AOD furnaces. From the service life of AOD furnace lined with different refractory materials (Table 3), different refractory materials have their own merits. Comprehensive consideration, magnesium and calcium series refractories have more advantages, magnesium and calcium series refractories in the AOD refining furnace application has become the development trend.
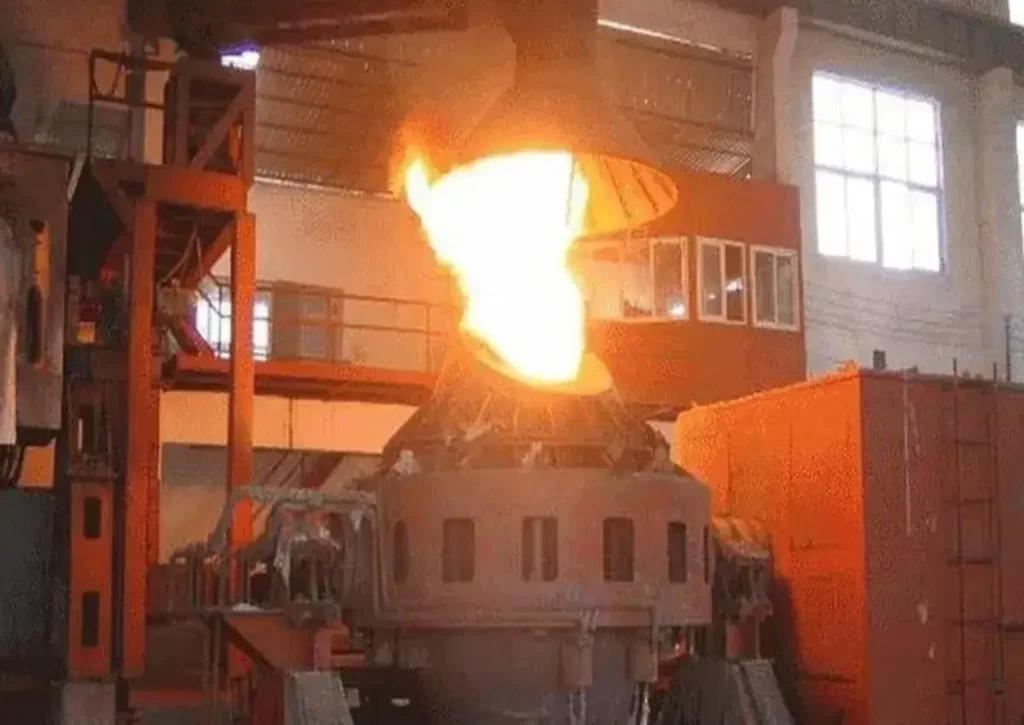
AOD furnaces need to meet the following criteria when selecting refractory materials:
- In terms of thermal stability, it must be able to withstand sudden high-temperature thermal shock, with good heat resistance and heat resistance. Ensure that a wide range of temperature changes in the process, does not occur serious thermal spalling, thermal cracking.
- In terms of corrosion resistance, must withstand a variety of high-temperature chemical erosion in the furnace, while ensuring that a large range of alkalinity changes can still maintain good thermal and chemical stability.
- In terms of mechanical properties, must have excellent mechanical shock resistance, wear resistance. To resist the frequent impact wear and tear of violently turbulent steel, slag mixture eddy current.
Traditionally, magnesium-chromium brick as the main furnace lining materials in the United States, in recent years, also focus on the development of magnesium-calcium series refractories.
Magnesium-calcium series refractories have their unique advantages:
(1) Its main components, MgO and CaO, have high melting points (2800 ℃ and 2570 ℃, respectively), low vapor pressure and stable thermodynamic properties.
(2) MgO-CaO combination than MgO-MgO combination of two-sided angle is large, is conducive to improve the resistance to slag permeability and slag erosion. Magnesium-calcium series materials are better than magnesium-chromium series materials in thermal shock resistance.
(3)The existence of CaO can purify the steel, especially suitable for smelting pure steel.
(4) Raw material resources, low price, and no chromium pollution.