Cause analysis
1. The red fire at the roof expansion joints
Furnace top expansion joints in the red fire in the transverse and longitudinal expansion joints, basically along the direction of the expansion joints in a line. Furnace top pouring construction, expansion joint plate is generally blocked with wooden square, wooden square end size 100mm × 100mm better, but most of the construction site using 100mm × 50mm or 100mm × 30mm, 80mm × 50mm or 80mm × 30mm wooden square, basically removed from the old wood to be utilized. And the top of the furnace anchored brick spacing is generally designed for 300mm × 300mm, pouring will be too small due to the end size of the wooden square can not block the expansion plate, resulting in the vibration process of the anchored brick wedge loosening, resulting in the anchored brick deflection, resulting in the expansion of the plate deflection, and sometimes deflected to the anchored brick. When using clay bricks to press the seam, the skewed expansion joints can not be pressed, high furnace temperature and furnace pressure, the lightweight material is blown up, the expansion joints will be red and fire.
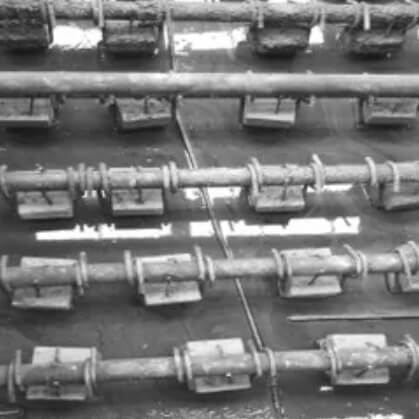
Expansion joint plate deflected to anchor brick
2.Anchor brick around the red fire
Furnace roof casting construction, vibration is not uniform, anchored brick around the casting material vibration is not dense, high temperature state of the anchored brick around the emergence of small gaps, will lead to the anchored brick around the red fire. In addition, the expansion joint plate is placed skewed to the anchoring brick, the expansion joint is not pressed, will also appear around the anchoring brick red fire. After cleaning up the expansion joints at the lightweight materials, pressure seam bricks and fiber blankets, it was found that the expansion joints were skewed in many cases, and some expansion joints were skewed to the edge of the anchoring bricks.
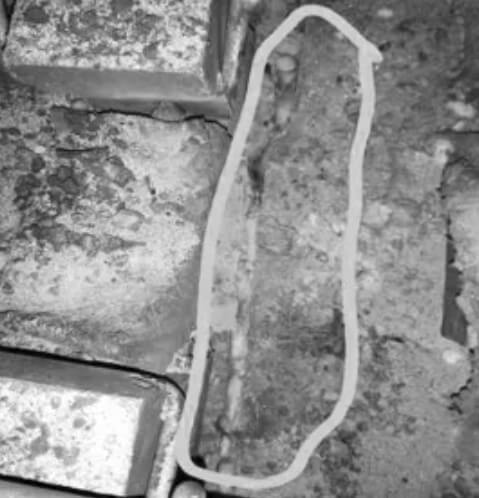
3.The influence of high furnace temperature and high furnace pressure
Heating furnace steel temperature design up to 1280 ℃, due to unskilled workers, often more than 1300 ℃. Furnace pressure to not more than 30Pa is appropriate, but the actual operation of the workers furnace pressure basically fluctuations between 30 ~ 80Pa. Therefore, under the influence of high furnace temperature and high furnace pressure, the lightweight castables at the roof expansion joints were blown up, which also promoted the redness and fire at the roof expansion joints.
In summary, the main reason for the red fire at the roof expansion joints and around the anchoring bricks is that the expansion plate was placed in a skewed position and the expansion joints were not pressed during the roof casting construction. In addition, in the pouring process, the unevenness of vibration on the material construction of the compactness has an impact; high furnace temperature, furnace pressure on the expansion joints at the red fire also played a role in promoting, aggravating.
Rectification measures
(1) Clean out all the horizontal and longitudinal expansion joints on the roof of the heating furnace, and fill the expansion joints with 10mm thick zirconium-containing fiber blankets.
Use high-temperature cement to paste 20mm thick zirconium-containing fiber blanket to the surface of the heavy material on the roof to cover the expansion joints, and press the clay bricks along the expansion joints. Finally, use PN-LW0.6 lightweight castables for heat preservation.
(2) Strengthen the workers’ operation training, formulate assessment measures to ensure that the furnace temperature, furnace pressure control in the normal range. Furnace temperature is required to control the maximum temperature of the steel out of the furnace below 1300℃, and the furnace pressure is not more than 30Pa.
Protective measure
During the pouring construction of the heating furnace roof, in order to avoid redness and fire around the expansion joints of the furnace roof and the anchor bricks caused by the skewed placement of the expansion joint plates on the furnace roof and uneven pouring vibration, the following preventive measures can be taken.
(1) The furnace roof is cast using steel formwork
When steel formwork is used to support the furnace roof pouring construction, Φ10mm steel bars can be spot welded on the steel formwork. The length of the steel bars should be greater than the width of the expansion joint plate to ensure that the expansion joint plate is located at the center line of the two rows of anchor bricks. The expansion joint plate is fixed with wire and wood. After pouring is completed on both sides of the expansion joint plate, the steel bars can be taken out.
(2) The furnace roof is cast using wooden formwork
When the furnace roof is cast using wooden formwork, the expansion plate is placed behind the center line of two rows of anchor bricks, and holes are drilled on the wooden formwork and expansion plate with a hand drill, and then the expansion plate and wooden formwork are tied together with wire, and wooden blocks are placed on both sides of the expansion plate. After the furnace roof is cast, the wire is cut with pliers before removing the formwork, and then the wooden formwork is removed.
(3) Ensure the uniformity of vibration
During the pouring of the furnace roof, the vibrating rod is required to be inserted quickly and pulled out slowly, with a moving speed not exceeding 2m/min. According to the radius of action of the vibrating rod, each part must be vibrated in place, especially around the anchor bricks, to ensure uniform vibration and avoid the formation of gaps. It is best to vibrate the castable material without large bubbles.
Correction effect
After rectification according to the situation of red and flaming top of heating furnace, the results are as follows:
(1)The phenomenon of the heating furnace roof turning red and emitting fire has been completely solved, and no abnormal situation has occurred on the furnace roof;
(2) Heating capacity is significantly enhanced, production tends to be normalized and continuous, and production efficiency is greatly improved;
(3) Energy consumption has dropped significantly, with gas consumption falling below 30,000 m³/h;
(4) No CO can be detected on the top of the heating furnace, and the use environment is greatly improved;
(5) It has accumulated experience in dealing with the phenomenon of redness and fire on the roof of the heating furnace, which has a certain reference significance.