Medium frequency furnace furnace use process of various processes on the service life of the furnace is also quite important, a variety of improper operation may reduce the service life of the furnace. Therefore, in the use of the process should pay attention to the following points:
1. in the use of medium frequency furnace, if due to failure or other reasons need to stop for a long time, an important operation step is to completely empty the furnace liquid iron. This measure is critical, because it can effectively prevent the iron in the cooling and solidification process on the furnace lining to produce cracking, so as to avoid unnecessary damage to the furnace lining. In some cases, however, it is difficult to determine whether the furnace lining is still intact if it cannot be emptied completely and the molten iron has condensed. In the face of such uncertainty, the safest course of action is to dismantle the furnace for inspection. This ensures the safety of the operators and allows any potential lining damage to be detected and dealt with in a timely manner.
2. In the medium frequency furnace stop and enter the cooling phase, in order to ensure that the furnace lining will not be damaged by the sudden cold, we recommend the use of empty furnace cooling. This practice helps the furnace lining to gradually release heat, to avoid rapid temperature changes on its adverse effects. At the same time, in order to further protect the furnace lining, special attention should be paid to the temperature difference between the upper and lower parts of the furnace during the cooling process. For this purpose, it is recommended to cover the furnace with a lid, so that the temperature of the furnace lining can be kept uniform during cooling, effectively preventing cracks caused by excessive temperature differences. Through these careful operation and maintenance measures, we can better guarantee the service life of the furnace and ensure its long-term stable operation.
3.The appearance of vertical cracks during the cooling process of an IF furnace is a phenomenon that is difficult to avoid completely. In view of this, when restarting a cold furnace, we particularly recommend the step of low-temperature baking as a preliminary preheating measure. The purpose of this step is to create a more stable environment for the melting process by gently closing the cracks in the furnace lining. This is followed by the normal melting operation. This sequence of operations prevents the molten iron from penetrating into the cracks that have not yet been fully closed, and thus prevents the cracks from expanding further under high temperature and pressure. Such a start-up procedure not only reflects a professional understanding of the maintenance of the IF furnace, but also ensures the safety of the operation process and maximizes the service life of the furnace.
4.In the process of using the medium frequency furnace, the careful observation of the furnace condition is particularly important, which is actually an effective protection measure for the furnace. In order to ensure the stable operation of the furnace, we recommend that the bottom of the furnace be measured accurately every three days. Such regular inspection helps to find and deal with any potential abnormality or wear and tear situation in time. At the same time, the condition of the furnace walls should be carefully observed during the daily use of each furnace, without missing any minor changes. Through this combination of daily observation and regular inspections, we can provide a strong guarantee for the safety of the furnace lining and ensure that the furnace can continue to operate in optimal condition, thus extending its service life and improving overall productivity.
5.We always pay great attention to the maintenance and repair of the medium frequency furnace equipment. In daily operation, an important maintenance measure is to frequently carry out coil blowing, this step is designed to effectively remove the accumulated debris on the coil, thus preventing the debris caused by the coil breakdown problem. This careful maintenance significantly reduces the risk of having to dismantle the furnace due to equipment failure, which not only reduces unnecessary maintenance costs and time, but also greatly extends the service life of the crucible. Therefore, regular and professional maintenance of IF furnace equipment is undoubtedly an economical and efficient long-term investment strategy, which provides a solid guarantee for the stable operation of the equipment and the smooth progress of production.
6.For the new put into use in the frequency furnace, because of its sintering layer is relatively thin, therefore, the initial use of the process is particularly important. In the new furnace for the first time out of the water, it is recommended that only 50% of the water discharge to start charging melting. This measure is intended to avoid charging immediately after the furnace water has been completely discharged, which can lead to potential defects such as cracks in the furnace lining due to sudden cooling. To further strengthen the stability of the furnace lining, new furnaces should be operated as continuously as possible to avoid temperature fluctuations caused by intermittent melting, which can lead to cracks. Generally speaking, one week of continuous melting operation is an ideal initial use cycle. In the process of using a new furnace, special attention also needs to be paid to the way and method of discharging the material. Strong impacts of the material on the furnace bottom and walls should be avoided as much as possible, because under such impacts there is a risk of spalling or cracking of the furnace lining, which can adversely affect the overall structure and service life of the furnace. In summary, in order to get a longer service life of the furnace, i.e. high furnace age, then in the early stage of the use of the new furnace, it is necessary to strictly follow the scientific process of using the furnace to ensure that every step of the operation is meticulous, so as to lay a solid foundation for the long-term stable operation of the furnace.
7. In the melting process of medium frequency furnace, we strongly recommend to avoid high temperature melting operation. The reason is that, when the furnace temperature reaches high temperature, the furnace lining and the liquid iron crucible reaction, the chemical reaction formula can be expressed as: SiO2 + 2C → Si + 2CO. this reaction reveals an important law: the higher the temperature, the higher the content of carbon (C), and the lower the content of silicon (Si), the lining of the furnace will be significantly aggravated by the situation of erosion. This phenomenon is particularly noticeable in the early stages of a new furnace. Therefore, in the melting process, we should try to avoid too high melting temperature under the premise of ensuring that the outlet temperature is up to standard. Generally speaking, the water discharge temperature should be controlled between 1490℃ and 1540℃, but in the actual melting operation, we prefer to recommend maintaining the temperature in the range of 1490℃ to 1520℃. It is worth mentioning that after the water has been discharged, it is quite a practical strategy to take power-off measures to keep the furnace at a lower temperature for holding. When preparing to produce water again, we can reasonably adjust the temperature rise according to the temperature of the previous packet of water. This practice not only can effectively reduce the erosion effect of high temperature ferrofluid on the furnace lining, thus prolonging the service life of the furnace lining, but also can significantly reduce the power consumption. Therefore, this method is undoubtedly a good way to recommend for improving furnace age and reducing power consumption.
8.In the use of intermediate frequency furnace process, to prevent overheating of the furnace lining is a critical link. In view of the medium frequency furnace has the characteristics of rapid heating, if the melting worker in the operation is not focused enough, it is easy to appear the furnace material “bridge” phenomenon. This situation will lead to high localized temperature of the furnace lining, which may even exceed the refractory limit of the lining material, thus triggering the risk of melting and erosion of the furnace lining. Similarly, if the furnace foreman fails to keep a close eye on the melting process, there is a risk of melting and erosion of the furnace lining when the temperature climbs to too high a level. These conditions can drastically reduce the service life of the furnace lining, so a high degree of vigilance must be maintained at all times during the melting operation. For example, melting workers should be diligent in poking the material to ensure even distribution of the material and avoid local overheating; while pre-furnace workers need to judge and control the temperature of the molten iron in real time according to the color change of the molten iron to ensure the safety of the furnace lining. Through these meticulous operations and monitoring, we can effectively protect the integrity of the furnace lining and extend its service life.
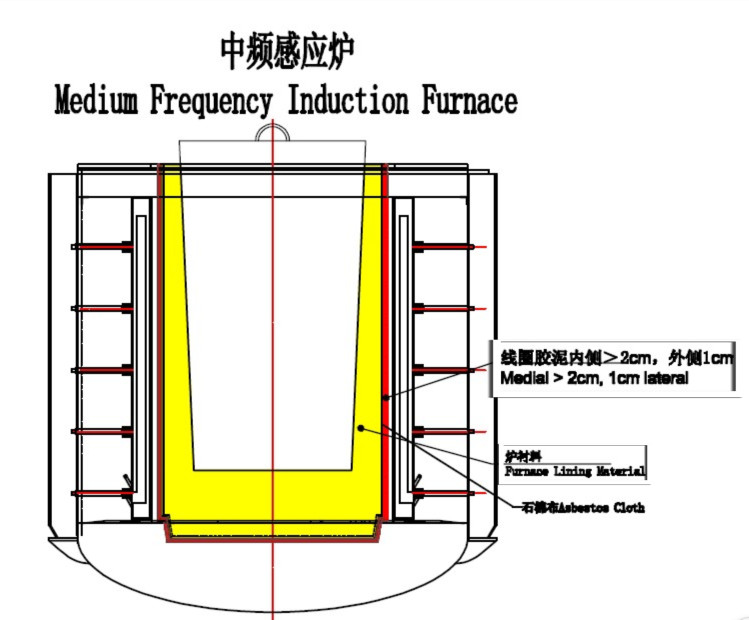