Magnesium carbon brick in use in addition to withstand high temperature, oxidation and slag erosion, but also need to withstand the impact of steel and scouring effect, which requires magnesium carbon brick has a high high temperature strength. High-temperature flexural strength that has become a measure of high-temperature strength of magnesium-carbon bricks indicators, but also magnesium-carbon bricks in one of the important research direction.
There are many factors affecting its high temperature flexural strength, the most important of which are raw material purity, carbon content, binding agent, matrix composition and organisational structure of magnesium carbon bricks. Raw material purity is relatively simple, high purity of magnesium sand, crystalline scale is large, then distributed in the low melting point of the magnesite grain boundaries of the low content of material phases, the degree of direct bonding is high, high-temperature flexural strength to be better; graphite purity and content of the impact is the same. The research on matrix composition, organisational structure and other aspects of the relatively complex, but also to enhance the magnesium carbon brick high temperature flexural strength of the most concentrated research areas, which is broadly divided into the following three directions.
1.Add metal powder
In the enhancement of high-temperature flexural strength, the added metal powder mainly includes metal Al, Si and so on. Its role mechanism mainly includes: ① metal Al, Si, etc. and magnesium carbon brick graphite, resin carbon, etc. to generate Al4C3, SiC, etc., to strengthen the bond between carbon and carbon to enhance the strength; ② metal Al, Si, etc. in magnesium carbon brick whiskers, fibres, etc., to strengthen the material matrix; ③ generation of magnesium-aluminium spinel and other material phases, to improve ceramic bonding and so on. With the increase of metal Al, the high temperature flexural strength of low carbon magnesium carbon bricks increased and more MgAIO and whiskers were found in the structure of magnesium carbon bricks with the addition of metal Al with a mass fraction of 6%.
By introducing metal Zn powder and Al powder with different properties, it was found that the high temperature flexural strength of the specimens treated at 1400°C was the greatest when the metal addition mass ratio Al/Zn was 1 and the addition mass fraction was 1% in both cases. At this time, the expansion accompanied by the metal carbonation reaction was moderate, and the matrix aggregate was tightly bonded and less stressed. In magnesium-carbon bricks, columnar or plate-like Al4C3 interspersed with each other existed between the aggregates or blocked the pores inside the specimen, which increased the resistance of the particles to ask slip. Therefore, the addition of metal Al generated Al4C3, which enhanced the high-temperature flexural strength of magnesium-carbon bricks. The addition of metal Si can also increase the high temperature strength of magnesium carbon bricks, but the effect is not as significant as that of metal Al.
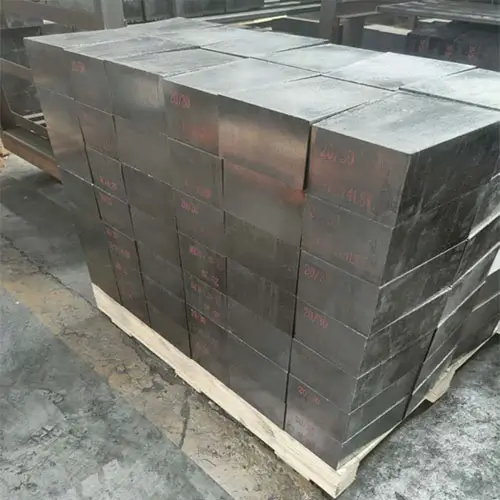
2.In-situ generation of whiskers such as carbides and nitrides
The increase in high-temperature flexural strength of magnesium-carbon bricks is often achieved through the in-situ generation of carbide and nitride whiskers. Whiskers are generally one-dimensional crystalline materials of nano or submicron level, with few internal defects and strength and modulus close to the theoretical values of crystalline materials. At the same time, the whiskers also confer a better strength to the material by their reticular distribution in the bricks or by their pinning and locking effects in the organisational structure of magnesium-carbon bricks. The high temperature flexural strength and residual flexural strength after thermal shock of the specimens of the magnesium carbon bricks with the addition of metallic Si and Al powders increased with the increase in heat treatment temperature, while the flexural strength of the specimens after heat treatment at 1400°C was greater. Through the analysis of the microstructure, it was found that at 1400℃, not only was there needle-like AlN generated in the brick and embedded in the surface of magnesium sand particles, but also accompanied by a large number of SiC whiskers and needle-like β-Si3N4 whiskers generated at the same time. Such a microstructure, when the material is subjected to external force, the stress can be transferred to the whiskers through the interface layer from the matrix, the whiskers make the matrix stress dispersed, reducing the destructive effect. When the specimen is subjected to thermal stress and the crack size is relatively small, the whiskers play a bridging role to inhibit the continued expansion of the crack; when with the crack increase, the whiskers at the tip of the crack is further destroyed, whiskers from the matrix is pulled out and consume energy, this time the pull-out effect will give the magnesium-carbon bricks with high-temperature mechanical properties.
3.Generation or incorporation of carbon nanoparticles within magnesium carbon bricks
Carbon nanotubes are new materials that appeared in recent years with outstanding mechanical properties, so in terms of high-temperature flexural strength enhancement and microstructure improvement of magnesium-carbon bricks, some scholars got better results by introducing catalysts and other ways to form carbon nanotubes in the materials. Phenolic resin was modified and low carbon magnesium-carbon bricks were prepared by introducing Fe nanosheets. It was found that magnesium carbon bricks doped with 0.5% mass fraction produced a large number of carbon nanotubes with diameters of 50-100 ml and lengths of micrometres at 1000°C. Compared to the undoped Fe nanosheets specimen, the high-temperature flexural strength increased from 8.29 MPa to 10.29 MPa, which was about 24%, reaching the highest value.
The presence of a large number of carbon nanotubes firmly interlocked the MgO grains, and when stress was applied on the blank specimen, cracks started to appear on the surface of the specified specimen and subsequently propagated along the MgO grain boundaries in the matrix until the specimen was completely destroyed. For the 0.5% doped specimen, when the crack passes through the MgO grains, the carbon nanotubes, due to their high strength and toughness, can absorb and release the stress at the crack tip through bridging and crack deflection mechanisms.
In addition to the formation of carbon nanotubes in magnesium-carbon bricks, there is the introduction of nanocarbon to improve the microstructure of magnesium-carbon bricks and to enhance the high-temperature flexural strength of the material. On the basis of 3% mass fraction graphite additions, it was found that the high-temperature flexural strength (HMOR) increased with the increase of nanocarbon content, and the value of which was increased from 2.5 MPa to 4.5 MPa ( at 0.9% mass fraction addition) and remained constant at further increase in nanocarbon. Further analyses revealed that the filling and compaction effect was a little better with the increase in the content of nanocarbon. At the same time, the nanocarbon is very reactive and can form carbides at a higher rate when in contact with the metal additives, resulting in a stronger bond and higher strength.
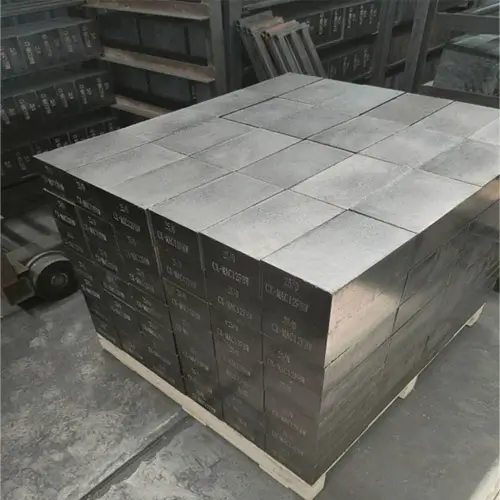
More Products about Magnesia Carbon Brick
What is magnesia carbon brick?
Magnesia-Carbon brick is resin-bonded brick made from dead-burned or fused magnesia and graphite. Anti-oxidant is added if required. Our control over bonding agents mean that these products are classed as eco friendly in terms of steel production.
Does magnesia work in brick?
Magnesia: A small quantity of magnesia in brick earth imparts a yellow tint to the bricks and decreases shrinkage. But excess magnesia leads to the decay of bricks.
Why is C used in magnesia refractory?
As the wetting behavior between C and molten slag is low, C contained in the refractory can effectively protect it from chemical attack by molten slag.
How are magnesia carbon bricks manufactured?
The raw materials are prepared in a predetermined proportion and mixed in a strong sand mixer. The order of feeding is magnesia aggregate – Binder – graphite – fine powder and additives, and the mixing time is 15 – 45 minutes. In order to mix evenly, phenolic resin is usually heated to 35-45 C before mixing.