purging plug are high-end functional refractory materials that do not work continuously during the entire ladle turnover cycle, so different physical and chemical corrosion will occur at different times. Damage to purging plug can be divided into the following categories:
1.Oxygen purging effect
From the completion of tapping the ladle to the next steel connection, the ladle will be hot repaired in the hot repair area. At this time, the purging plug need to be burned and purged with oxygen to clean the remaining steel and slag on the working surface. Oxygen lance purging is beneficial to the normal use of purging plug. This measure ensures the cleanliness of the working surface of the purging plug and the smooth flow of gas channels, so that the ladle turnover can proceed smoothly. However, because it is difficult to accurately grasp the thickness of steel and slag remaining on the working surface of the breathable seat bricks in the hot repair area, after the residues are removed, the purging plug may be misfired or over-fired. When the bottom is in poor condition, Or the situation may become more serious when the operator in the hot repair area makes a mistake in judgment. The temperature of the oxygen lance reaches above 2000°C. The high-temperature air flow is very fatal to the purging plug. The melting loss in these few minutes is often higher than that in normal use. 2~3 times.
2.Effect of thermal stress
The refractory materials on the working surface of the purging plug, especially the refractory materials around the air outlets of the purging plug, are in direct contact with high-temperature molten steel, and are affected by the high-temperature molten steel and the continuous flow of cold air, which will cause a large temperature gradient. Due to repeated use, the purging plug are subject to rapid cooling and heating effects, especially the areas close to the air outlet are subject to greater thermal stress, and are prone to ring cracks and then cracking.
3.Mechanical wear effect
During the tapping process, the high-speed and strong erosion of the molten steel on the bottom of the ladle will also accelerate the corrosion of the purging plug. Through hydraulic model tests, it was found that when the low-speed air flow is injected into the liquid phase molten pool, the air flow hits back and hits the front edge of the purging plug, giving a certain impact force to the refractory materials around the air outlet of the purging plug. . When the gas flow rate is further increased, the reverse pulse frequency decreases, but the reverse impact intensity further increases; in addition, when the blown argon enters the normal eruption state, intense bubbles form a gas eruption beam, and the eruption beam strengthens the stirring at the bottom of the ladle. The liquid phase movement at the bottom of the ladle is aggravated, and the two-phase flow causes the purging plug to be subjected to intense shear and impact stress effects. When the purging plug are higher than the seat bricks, they are particularly sheared and washed away by this flow. The part higher than the seat bricks is usually washed away after one use. Therefore, when the purging plug are newly replaced, this situation often occurs. It is easy to happen; in addition, if the valve is closed quickly after refining, the reverse impact of the molten steel will also accelerate the damage of the breathable brick.
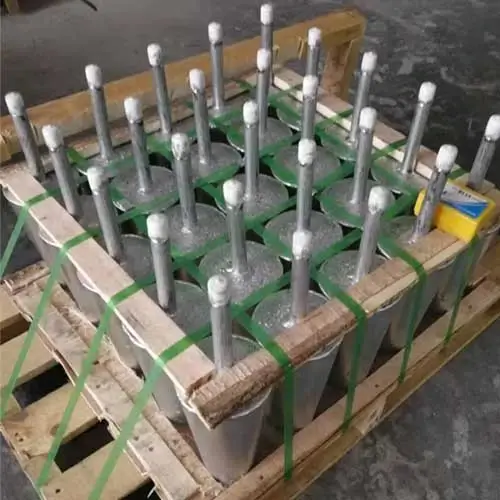
More details about Ladle purging plug:
What is purging in ladle?
Dual gas purging is often done in a ladle to accelerate the refining operations in steel industries. The purged gas, mainly argon imparts momentum to the molten metal and establishes a turbulent recirculating flow in the melt, which generates shear stresses on the ladle walls.
What are the different types of purging plugs?
There are two types of purging plugs, porous plug which is focused more on a reliable bubbling, and slit plug (through-bore type) which is more focused on service life. However it is essential to develop the good characteristic of it, and reduce the week point of both types.
What is argon purging in steel making?
The production of high-quality steel requires purging with argon to remove impurities, degas the molten metal, and optimize the alloying process. However, sealing challenges in steelworks result in variable argon losses. But accurate mass flow measurements are crucial for process optimization.