1.Refractoriness
When the refractory material is subjected to sufficient high temperature, it will gradually soften and melt into a viscous liquid. Therefore, refractoriness refers to the temperature at which a refractory material can resist high temperatures without melting. It is one of the main aspects of performance of refractory materials.
The refractoriness is measured with a sample of specified size and shape at a certain heating rate. This standard sample is a triangular pyramid with a height of 30 mm, a lower base of 8 mm and an upper side of 2 mm. Under the influence of high temperature, the sample gradually softens, and according to the reduction of viscosity after the formation of the solution, it tilts to the bottom under the action of its own weight. The temperature at which the apex of the sample is lowered to its bottom plane is used as the assumed “melting” temperature of the refractory material. The heating rate of the sample can affect this “melting” temperature, so a certain heating rate must be observed.
The determination of the sample temperature is compared with the standard temperature measuring cone under the same heating conditions. This “temperature measuring cone” is made of a mixture of kaolin, alumina and quartz, and fusible materials are added to the low temperature cone. In this way, temperature measuring cones with different bending temperatures are formed.
At present, the generally recognized refractory fire bricks should have a refractoriness above 1580°C.
2.Structural Strength at High Temperature
The high-temperature structural strength of refractory products is generally expressed by the temperature of a certain amount of deformation caused by refractory materials under the action of a static load of 2 kg per square centimeter. According to the amount of deformation, it is divided into 4%~10% deformation at the beginning deformation temperature and 20%~40% deformation at the end deformation temperature.
The load softening temperature of refractories mainly depends on the chemical-mineral properties of natural refractories (that is, the existence of certain crystalline phases), the characteristics of the crystalline structure of finished bricks, the ratio between crystallization and glass phases (amorphous) and glass The viscosity of the phase at a certain temperature. The generally visible granular structure of the product also has a certain influence on it. Denser and firmer articles have higher onset softening points. In addition, increasing the amount of fusible material will also reduce the deformation temperature of the refractory material. The amount of reduction in deformation temperature mainly depends on the chemical composition and proportion of the fusible. The most influential is the oxide that can increase the amount of liquid phase and reduce its viscosity. This oxide is Na2O for clay bricks and Al2O3 for silica bricks. However, oxides used as mineralizers to increase and improve the crystallization of bricks can promote an increase in softening temperature.
The actual load on the vertical wall of the industrial kiln is far lower than the load of 2 kg per square centimeter adopted during the inspection. Only in special cases, it reaches 0.5~1.0 kg per square centimeter. And when the brick lining side is heated, the weight of its load is borne by the cooler side of the masonry. The pillars and vaults have a greater impact. In most cases, slag, fuel ash, mineral powder, gas, etc. are the main factors that damage refractory bricks. Due to the action of these things, the chemical-mineral composition of refractory bricks can be changed, and its structural strength can be significantly reduced.
The heating conditions of the masonry on the coke oven are different from other industrial furnaces. The entire furnace body is composed of refractory masonry nearly 10 meters high, and its own weight is very heavy. The masonry is heated on both sides and is often subjected to mechanical friction. Therefore, it is necessary to maintain a low operating temperature, and the heating regime must be strictly followed to maintain the life of the furnace brick.
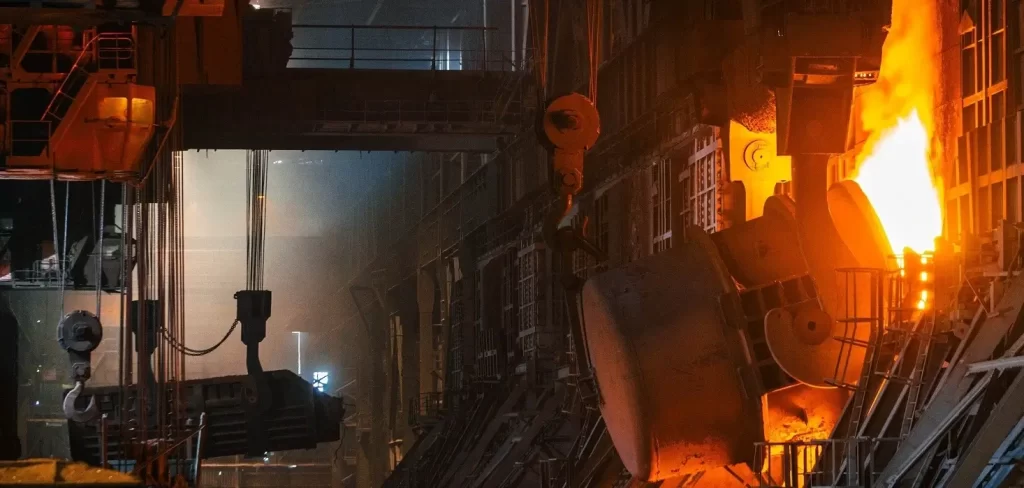
3.Volume fixity at high temperature
When refractory bricks are stored at high temperature for a long time, it will cause some remaining phase components and structures to continue to change, resulting in recrystallization and sintering. The appearance of these chemical changes causes changes in the volume of refractory products. These irreversible dimensional changes are called residual expansion or contraction of the refractory.
These residual expansions or shrinkages are caused by insufficient firing of the refractory products. Therefore, under sufficient firing temperature and firing time, the refractory material can achieve the highest volume fixity. However, when the bricks are fired at an excessively high temperature, it may cause deformation of the bricks and vitrification of the tissue. A large amount of waste is caused by the deformation of the brick, and the vitrification of the tissue will reduce its resistance to sudden temperature changes.
When the remaining shrinkage is too large, it will cause the cracking of the masonry brick joints, destroy the tightness of the masonry, and result in loosening and destruction of the masonry structure.
Residual bloat does less damage. However, when it is too large, it will also cause swelling of the masonry, destroying its geometric shape and uniform distribution of stress.
The remaining shrinkage and expansion of refractory materials are measured by repeated calcining at a certain temperature. The test temperature of each group and each product is determined according to the requirements and service conditions of this product. For clay and semi-siliceous refractory materials in various states, it is taken as 1250~1450 ° C, and for silica bricks. 1450°C. Measure the volume change before and after calcination, convert it into linear shrinkage, and express it in percentage. The allowable number of residual shrinkage or expansion of various refractory materials depends on the nature of their use, and generally should not exceed 0.5~1.0.
4.Resistance to sudden temperature changes
In intermittently operated industrial kilns, due to changes in heating temperature, or in continuously operated equipment, due to temperature fluctuations, cracks will occur in refractory products and even bricks parallel to the heating surface will peel off. The ability of refractory products to resist repeated temperature fluctuations without damage is called the resistance to sudden temperature changes.
The cause of this cracking is due to the stress generated by the temperature difference inside the product after the heating temperature changes. It is directly related to the thermal expansion performance and thermal conductivity of refractory products.
The use of computational methods to determine resistance to sudden temperature changes is complex and not always complete. Therefore, the direct measurement method is generally used. This method is to place one end of the standard-sized refractory product in an electric furnace and heat it to 850°C, and then cool it in flowing water. According to the standard method of OCT-3267, the rapid temperature change resistance of the refractory is indicated by the number of rapid cooling and rapid heating before the spalled part reaches 20% of the initial total weight.
Such a measurement method is obviously inconsistent with the operating conditions of industrial kilns. However, due to the limitation of test time, this method is generally used to test.
In addition, there are some other test methods. From the results of these tests, the performance of a certain refractory material in this respect can be provided, and it should be considered as one of the important conditions when selecting refractory materials used in various parts of the coke oven.
5.Main physical properties
1.Thermal expansion
Refractory products are like all physical objects – they expand when heated and contract when cooled. This kind of expansion is a reversible physical change, which is different from the aforementioned “residual expansion”. The expansion of the former is an irreversible change caused by changes in phase composition and structure, while thermal expansion depends on the chemical-mineral composition of the material, while the structural properties, density and strength of the bricks have no effect.
To evaluate the properties of refractory materials, not only the size of its expansion coefficient must be considered, but also the balance during the entire expansion process. Especially in coke ovens that require dense masonry structure, long service life, and are made of silica bricks, thermal expansion is even more important.
2. Thermal conductivity
The thermal conductivity coefficient of refractory products is expressed by “thermal conductivity”. Its unit can be calculated by technical unit – kcal/m•hour•degree, or physical unit – mcal/cm•second•degree.
The value of thermal conductivity λ increases with the increase of heating temperature. For example, the λ value of silica bricks at room temperature is about 1 kcal/m·hour·degree, and it increases to 1.5 kcal/m·hour·degree at 1000~1200°C. The values of clay bricks also change similarly. But for some refractory products with crystalline structure, when the temperature increases, the λ value shrinks instead. For example, the λ value of magnesia bricks at room temperature is 4~5, kcal/m•hour•degrees, and it is reduced to 2~3 kcal/m•hour•degrees at 1000°C. Silicon carbide bricks are particularly notable.
Thermal conductivity decreases with increasing porosity of refractory products. For example, the dense clay brick with a volume specific gravity of 1.95 has a lambda value of 0.9 kcal/m·hour·degree, but when the volume specific gravity increases to 2.2, the lambda value increases to 1.10 kcal/m·hour·degree.
Thermal conductivity is a very important technical indicator for the heating wall of the coke oven coking chamber.
3.Heat capacity
Heat capacity is expressed in kcal/kg, degree. It is useful in calculating the heat content of coke oven regenerator checker bricks and furnace wall bricks, which can indicate the ability of masonry to absorb heat from exhaust gas.
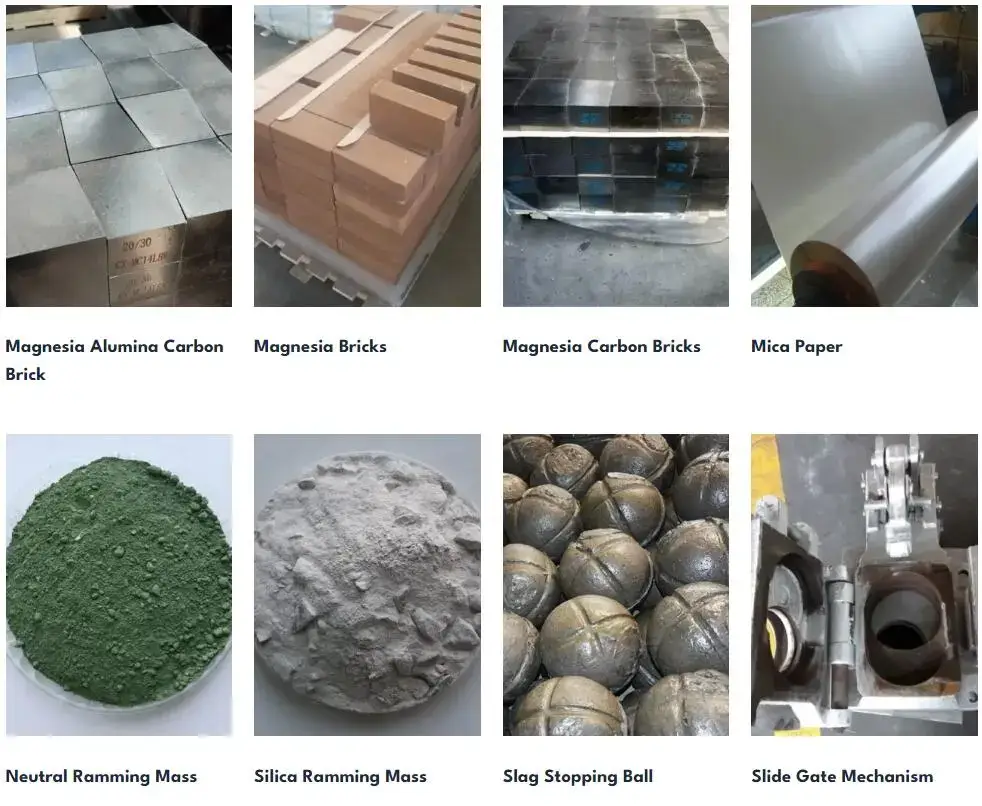