There are mainly two types of Induction Furnace. They are channel Induction Furnace, and coreless Induction Furnace.
Advantages of Using An Induction Melting Furnace
- Less Heat Loss
- Produces High-quality Metals
- Fast Speed of Melting
- Less Environmental Pollution
- Cost-effective Way of Melting Metals
- Easy to Automate Operations
Disadvantages of traditional sintering method:
- Long sintering time.
Normal sintering time is about more than 23 hours. For every month, factory should arrange sintering for about 8-10 times, which would cost too long time and very difficult for producing arrangement. - High cost on mould.
Normal weight for mould is more than 1 ton. During sintering, the highest temperature could reach 1580℃ and would last for more than 2 hours. The mould would be melted and cannot be re-used, which would cause a high cost. - High power consumption.
Power consumption during sintering is about 3220 KW h. Long sintering time would cause a high power cost.
During recent years, silica ramming mass is widely used in induction furnace. With this new product, we have gotten a great improvement on sintering method. Compared with traditional sintering method, the advantages of new method are as follows. - Much more easily to operate.
- Shorter sintering time and lower power consumption.
Sintering time is only about 2.5 hours, got more than 20 hours shorter. Power is only about 700 KW h, far lower than traditional method. - Lower cost on mould.
With new sintering method, sintering temperature is much lower, thus influence for mould is also very low. Therefore, the mould can be used for 4-5 times. If the mould can be taken out after lining, service life for mould will be even longer.
Shall any question for refractory materials, please feel free to come to us. We would be your powerful and reliable partner!
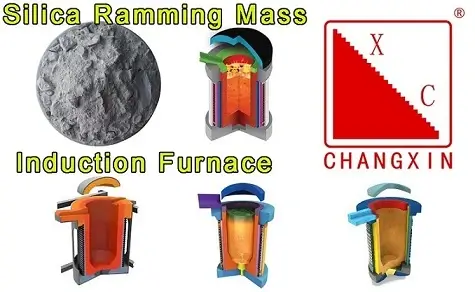
How does the Induction Furnace work?
An induction furnace is an electrical device used to heat metal or other conductive materials. An induction furnace consists of a crucible, which holds the material to be heated, and an induction coil installed around the crucible and is connected to an electrical power supply. The copper coil is energized with a high-frequency electrical current, which generates a fluctuating magnetic field around the crucible. Then, two options are possible: the crucible is made from a non-conductive material (e.g. ceramics), and the magnetic field induces an electric current in the material within the crucible, which generates heat through resistance. The second option is when the crucible is also made of a conductive material such as graphite. Then both the crucible and feedstock are heated with induction currents. The crucible material needs to be able to withstand high temperatures and prevent contamination of the heated material.
Additionally, induction furnaces offer the possibility of heating carried under various atmospheres. Depending on processed material and specific requirements, heating can be carried under vacuum, in an inert gas atmosphere (such as Argon, Nitrogen, or Helium), or an active gas atmosphere.
An induction melting furnace is efficient in melting most metals. Its versatility and efficiency make it the most preferable in today’s foundries. It is also energy-saving, making it a much better option than other traditional melting processes.
FAQ:
What is the process of induction furnace?
In the induction furnace, a coil carrying alternating electric current surrounds the container or chamber of metal. Eddy currents are induced in the metal (charge), the circulation of these currents producing extremely high temperatures for melting the metals and for making alloys of exact composition.
What is the process of induction furnace in steel manufacturing?
Power is put on through the power cables to induction coil which starts melting the charge. The Metallic charge melts to form liquid steel. As soon as the Liquid bath achieves a Temperature of around 1650°C, it is tapped into Steel ladle for further processing.
What are the different types of induction furnaces?
Induction furnaces are ideal for melting and alloying a wide variety of metals with minimum melt losses, however, little refining of the metal is possible. There are two main types of induction furnace: coreless and channel.
How heat is generated in induction furnace?
The rapidly alternating magnetic field penetrates the object, generating electric currents inside the conductor called eddy currents. The eddy currents flow through the resistance of the material, and heat it by Joule heating.